Formaspace Producing Workbenches for GM’s Ventilator Manufacturing
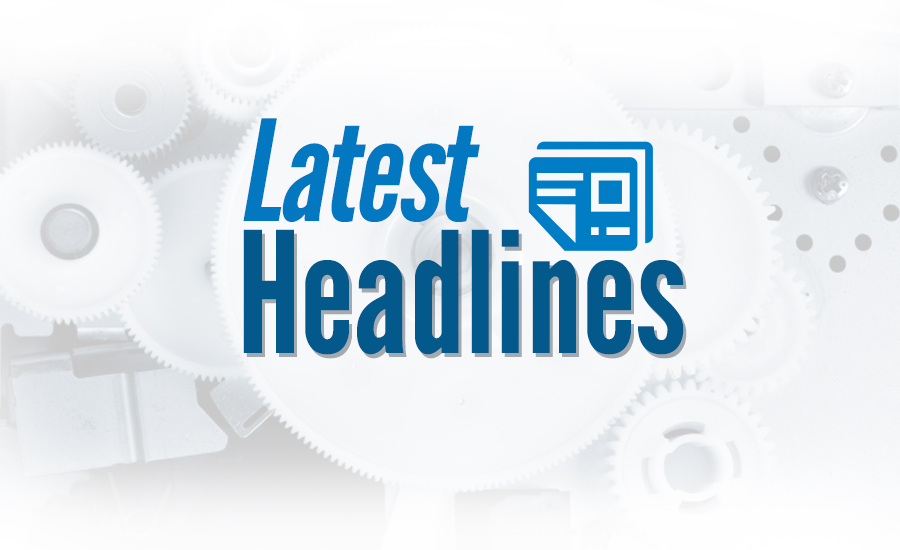
AUSTIN, TX — Formaspace, a company that designs and manufactures unique furniture solutions, completed an initial order of 500 new ESD workbenches to be sent to the General Motors manufacturing facility in Kokomo, Indiana.
Formaspace said it received the request from GM in late March and put the resources of the entire company toward the goal of delivering the benches as quickly as possible. The first truckload of ESD workbenches departed the Formaspace factory in Austin for Indiana three days later, with subsequent truckloads shipping out each day until the initial order was completed on April 9.
The assembly operations at the 100,000-square-foot facility in Kokomo span three floors of the building and feature a cleanroom area and two production lines. The 500 new workbenches supplied by Formaspace will be used for assembling the delicate electronic components.
Each of the workbenches features work surfaces with full coverage ESD protection to suppress static electric shocks that could damage sensitive microelectronics, built-in parts bins, heavy-duty white powder-coated steel frames, integrated overhead lighting and 8 plug power strips.
“We were able to respond quickly to this urgent request from GM because we manufacture all our custom industrial furniture using American-sourced steel and other raw materials from the USA at our factory headquarters in Austin, Texas,” says Jeff Turk, Formaspace CEO.
“Now that this initial order is complete, we are utilizing our newly increased production capacity to speed up delivery of non-healthcare critical projects, and expect those orders will be completed within a few days. I hope you will support us as we do our part to help healthcare providers respond to the COVID-19 pandemic,” adds Turk.
“Every ventilator we build can help save lives, and GM’s global supply base and manufacturing teams, the UAW, and the Kokomo community are working with passion and unwavering commitment to get the job done,” says Gerald Johnson, GM executive vice president, Global Manufacturing. “People have moved mountains to help increase the production of Ventec’s critical care ventilator. I have never seen anything like it in my career.”
“Our production facility is open and able to respond to the needs of our customers who are constructing new facilities or making changes to their existing operations, including manufacturing facilities, material handling, and distribution centers, pharma and healthcare laboratories, or primary, secondary, and university educational facilities,” says Frank Bucher, Formaspace Executive Vice President of Sales and Marketing. “We have added an additional work shift to keep up with current demand, and we are taking special care to ensure all hygiene precautions are in place to allow our facilities to operate safely during this difficult time.”
Looking for a reprint of this article?
From high-res PDFs to custom plaques, order your copy today!