Conveyors Make Batteries Go Round
Automating battery assembly can improve throughput and boost yields

Conveyors enable battery components to efficiently travel between workstations.
Photo courtesy Dorner Manufacturing Corp.
Electric vehicle batteries are bulky items that demand automation to address ergonomic risks and meet throughput requirements. Whether it’s a battery cell, module or pack, conveyors can address these concerns while making assembly lines faster, flexible and efficient.
Conveyors enable battery components to efficiently travel between workstations. These automated transportation systems are reliable workhorses in the age of severe staffing shortages.
Engineers can choose a wide variety of options for routing, handling and positioning electric vehicle batteries, which increase in weight and complexity with each step in the production process.
Scalability Is Important
Today, conveyors are more than just a moving belt. They often feature a high level of intelligence. For instance, shuttles can communicate with each other and prevent upstream bottlenecks. Conveyors also support a variety of automatic identification technologies for process control and tracking.
Running a production line requires cooperation from many moving parts. With tremendous growth in the battery industry projected to come over the next decade, every conveyor system needs to be scalable.
The most straightforward growth that companies need to anticipate is additional throughput. However, pallets that hold products as they travel along conveyors can only take so much weight.
Once that capacity is reached, operators will either need to add more pallets to the line, which takes up more space, or upgrade the weight capacity of the pallets they use. This consideration is particularly important for EV batteries as they quickly add more weight and size per unit. By anticipating future growth and building a system that can accommodate it, engineers can increase the longevity of their investments.
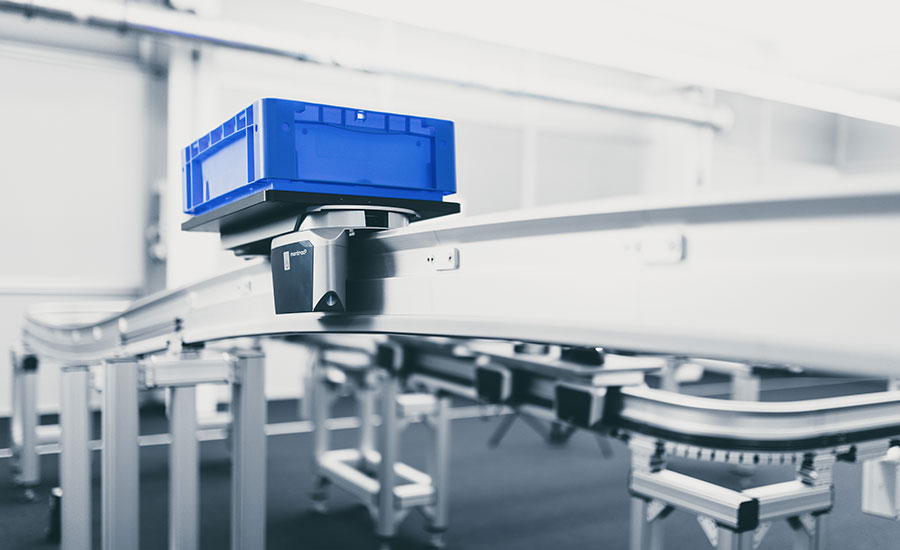
To enable future production volume, every conveyor system should be scalable. Photo courtesy Dorner Manufacturing Corp.
Incorporating additional capabilities into the line is another area where a conveyor needs to anticipate future needs. Many industries have found that consolidating construction into as few facilities as possible is a considerable time and money saver. Battery manufacturers looking to add future capacity after they ramp up production should anticipate this possibility when selecting a material handling system.
A conveyor with an aluminum rail profile can be ideal in these situations. These devices require minimal additional components to expand, especially compared to the supplementary motors and structures necessary for a typical conveyor. They may require a larger upfront investment, but the more the operation expands, this robust option will pay off.
While a conveyor system needs to be big enough to handle the products it processes, it also needs a small footprint to fit in the allotted space. Some assembly plants have found creative ways to make the most of smaller spaces, specifically by taking advantage of the open real estate available on ceilings. Sending units up in between stations to make more room on the floor can be an ideal option for facilities with limited space.
However, the weight of the objects being transported is an important consideration before moving forward with this conveyor style. Unlike ground-based systems that can be built to support nearly any product weight, ceiling-mounted conveyors are a bit more limited.
The belt itself is not a major concern, as those can be engineered to be very lightweight. So, the bulk of the weight comes from what the shuttles are carrying. Ceiling mounts need to be able to support more than the expected capacity to accommodate growth and unexpected congestion.
Robots need ample space to move around work envelopes and must allow access for any required maintenance. Line-side parts storage can also take up a lot of space as well, so conveyors must be strategically placed to feed automated elements of assembly lines. A good conveyor system will match all these features and an application’s required capabilities to the size of its space.
Traffic Direction
Conveyors can be designed with multiple diverters that work similarly to the railroad switches that direct trains. These check points can automatically scan items or manually be controlled to move products onto the correct track and send them off where they need to go. Often, this means either sending them into an automated storage system or to the next stage of the assembly line.
Once an item reaches a workstation, the conveyor system can automatically lift and locate it correctly for robots to perform automated tasks. This keeps an incorrectly positioned item on a conveyor from causing the robot to malfunction and disrupt the operation.
Other equipment can also support the overall flow of the line. In battery manufacturing, many applications require filling machines that continuously insert electrolytes into cells. In these situations, an accumulation table helps position the puck or the cell before filling and automatically feeds all stations at once. This is just one of many options that can be added to a conveyor to provide the speed and accuracy that’s required.
However, part of the challenge of adding conveyors to a battery assembly line is the required conditions for operation. Some steps in the production process take place in a clean or dry room. If a conveyor is used to transport components to that room, it must be made with materials compliant with the environment.
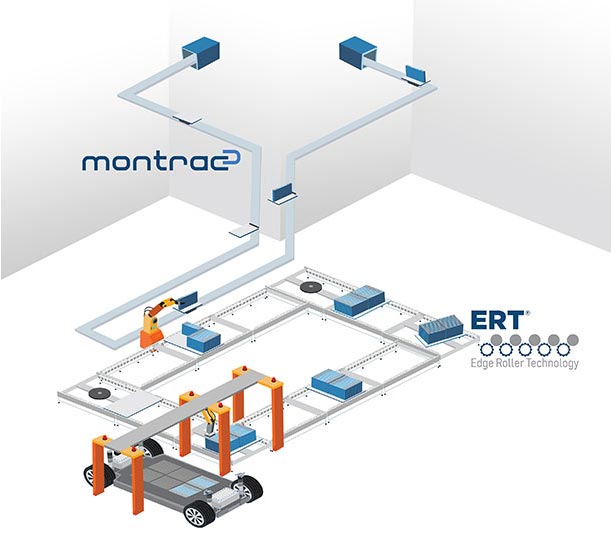
A variety of conveyors are required to assemble EV battery cells, modules and packs. Illustration courtesy Dorner Manufacturing Corp.
A conveyor system is almost never made up of one single type. Battery assembly plants require a variety of products that can run at different speeds, support different weights and move products as needed at each phase of production.
Determining the Right Conveyor
Battery manufacturers can choose a variety of conveyors. And, modular components enable engineers to design flexible assembly lines.
Traditional belt conveyors can be easily customized to achieve specific designs and assemblies, such as straights, curves, inclines, declines and Z-frames. Modular belts are available in surfaces that include flat top, flush grid and raised rib. Several materials are available for modular belts, including acetal, nylon, polyethylene and polypropylene. Materials for fabric belts include nylon, polyester, polyvinylchloride, silicone and thermoplastic urethane.
Flexible chain conveyors offer a variety of options with unique features, such as cleats, rollers, friction pads, steel top, anti-static and fabric belts. The easily reconfigurable systems are capable of multiple turns and inclines in one line. And, a low-profile design is ideal for tight spaces.
Pallet systems are an ideal fit for a number of operations because of the ability to run with the highly sensitive battery mounted to the pallet. These systems also offer a precise way for battery cells, modules and packs to interact with other steps in the operation. In addition, pallets can be placed in the right place and the right time to interact with assembly robots.
Pallet systems include timing belt, flexible chain and edge roller technology designs. Each system offers advanced pallet traffic management and is specifically designed to increase efficiency, reduce downtime in automation processes and provide accurate product placement.
Accumulation systems allow battery cells to accumulate before and during the jelly roll insertion process. This ensures that each workstation handles a steady flow of product.
Looking for a reprint of this article?
From high-res PDFs to custom plaques, order your copy today!