Testing High-Voltage EV Components

This multi-axis shaker table simulates real-world vibrations.
Photo courtesy TÜV SÜD America Inc.
As electric vehicles become more popular on land, sea and air, it’s becoming increasingly necessary to ensure the safety, performance and reliability of batteries, chargers, drive systems, power electronics and other components. High-voltage testing, analysis and validation is more important than ever.
TÜV SÜD AG is an independent organization that tests and certifies a variety of products for a diverse group of manufacturers. Every day, its team of engineers carefully examine everything from amusement park rides to robots and boilers to wind turbines. They’re also increasingly busy submitting EV components to rigorous environmental and functional testing protocols.
“Electric vehicles need to be energy-efficient as well as extremely safe, particularly where their high-voltage components are concerned,” says Benjamin Sommer, senior account manager at TÜV SÜD. “At our testing facilities, we guarantee that components such as on-board chargers, inverters and e-motors comply with strict functionality and safety specifications under even the most extreme conditions. With the advantages of our years of experience and state-of-the-art equipment, we can address individual needs and contribute to the development of high-quality and safe products.
“Understanding of the failure mechanism in the event of damage is a crucial aspect in the development of high-voltage components,” explains Sommer. “We view our role as a provider of future-facing testing, inspection and certification services to industry. By developing new testing processes, we aim to continuously improve the safety and performance of electric vehicles and accelerate the introduction of innovative technologies.”
According to Sommer, TÜV SÜD uses digital tools and connected testing methods to continuously optimize its testing processes. “Tests are monitored and analyzed in real time using integrated data analysis and evaluation tools,” he points out. “As well as reducing testing time, this allows manufacturers to respond more rapidly to technical challenges and speed the time to market of their innovative products.”
TÜV SÜD is based in Munich, Germany, with U.S. headquarters in Wakefield, MA. The 158-year-old organization prides itself on providing rigorous testing protocols that ensure compliance with strict specifications and standards.
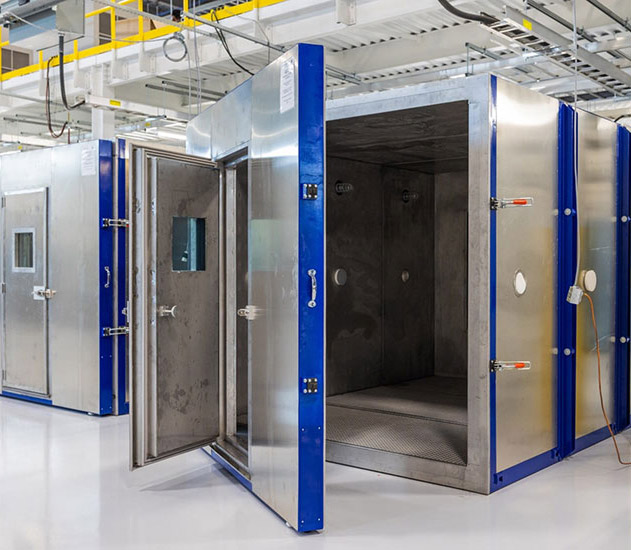
Walk-in environmental chambers subject EV components to high and low temperature extremes. Photo courtesy TÜV SÜD America Inc.
Last year, TÜV SÜD America Inc. opened a 82,530-square-foot facility in Auburn Hills, MI. The North America Transportation Electrification Laboratory features a variety of state-of-the-art equipment and chambers for testing lithium-ion batteries.
The facility is equipped to handle batteries up to 1,200 volts. It boasts an electrodynamic vibration table capable of generating forces up to 350 kilonewton, as well as an electrodynamic MAST (multi-axis shaker table) system for six degrees of freedom testing and high-frequency response. Another device can crush EV batteries with forces of up to 1 meganewton.
Autonomous & Electric Mobility recently asked Sommer to explain how TÜV SÜD is helping EV automakers and suppliers produce reliable products.
AEM: What is TÜV SÜD’s role in ensuring the safety and performance of electric vehicles and high-voltage technologies?
Sommer: As an independent partner, we offer a wide range of testing services to help companies identify and understand weak points. With our highly qualified personnel and modern testing facilities, we support our customers with electrical testing according to LV123, LV124 and other customer-specific requirements. We also provide various types of environmental testing for things such as vibration, climate, corrosion, temperature change, iced water shock, IP protection class testing and durability. In addition, TÜV SÜD performs high-voltage testing to ensure the durability and performance of EV components under extreme conditions. Through these extensive testing procedures, we support the automotive industry in meeting the highest safety standards and ensuring the reliability of electric vehicles on the market.
AEM: How many high-voltage testing facilities does TÜV SÜD operate?
Sommer: We operate a large number of testing centers and laboratories worldwide to ensure the safety and performance of electric vehicles. The most important high-voltage testing facilities are located in Germany, particularly in Mannheim and Straubing. We also have laboratories in China, India, Italy, Japan, South Korea and the United States.
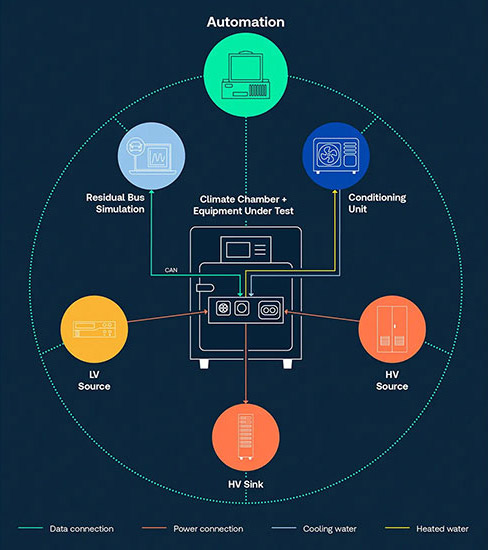
Fully automatic high-voltage tests record data in real time, enabling immediate response to all boundary conditions. Illustration courtesy TÜV SÜD AG
AEM: Does TÜV SÜD operate separate facilities dedicated to batteries or other EV technologies?
Sommer: Yes, we operate specialized labs for various key areas of electromobility, including batteries, drive systems and charging infrastructures. Some of our facilities offer all services at a single location, while others focus on specific topics. This enables us to offer customized testing for the respective requirements. The laboratories are also well connected internationally, which is particularly advantageous for global projects.
AEM: What are some of the challenges associated with testing EV components vs. other types of products that you have traditionally tested in the past?
Sommer: High-voltage components present specific challenges that go beyond the requirements of traditional testing. One of the biggest challenges is to operate the test objects with their complex functionality at a wide range of operating points. This requires both highly qualified personnel and modern test facilities. We rely on an automation system that controls and communicates with all test subjects via the CAN protocol. All data is also collected via this dynamic system, which connects the test object itself, climate chambers, and cooling and energy units. This allows us to create individual test procedures for customers to test components under real-world conditions and extreme loads.
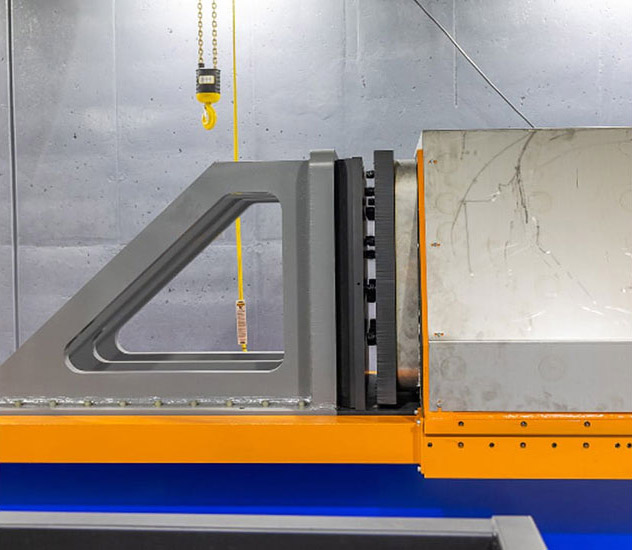
This battery crusher can smash EV batteries with forces of up to 1 meganewton. Photo courtesy TÜV SÜD America Inc.
AEM: Does TÜV SÜD focus on any particular type of tests?
Sommer: We perform a wide range of specialized testing tailored to the requirements of automotive manufacturers. Our engineers can perform almost any factory-specific standard test. These include all types of electrical and environmental simulation tests.
AEM: Do you test components used in all types of electric vehicles?
Sommer: We test high-voltage components not only for passenger cars, but also for buses, tractors and trucks. In addition, we test products used in other sectors, including aviation, marine and rail transport. With this broad focus, we can ensure the safety and reliability of high-voltage technologies in various industrial applications and support customers in bringing their products up to the highest standards.
AEM: How are you testing high-voltage components for various temperature extremes?
Sommer: We test EV components under extreme temperature conditions to ensure their reliability and performance in a wide range of environments. Tests cover temperature ranges from -50 C to 220 C, simulating freezing cold as well as extreme heat, as can occur near high-energy systems or in intense sunlight. These tests also include rapid temperature changes and long-term exposure to simulate real-life operating conditions.
AEM: How are you testing high-voltage components for various types of moisture and water tightness?
Sommer: Tests are based on the ISO 20653 standard, which provides detailed specifications for testing moisture and water resistance. The tests not only examine whether a unit is waterproof, but also where water enters if it is not. We use modern technologies for this, such as endoscopes that allow the interior of the unit to be examined in real time. This enables precise identification and evaluation of potential weak points.
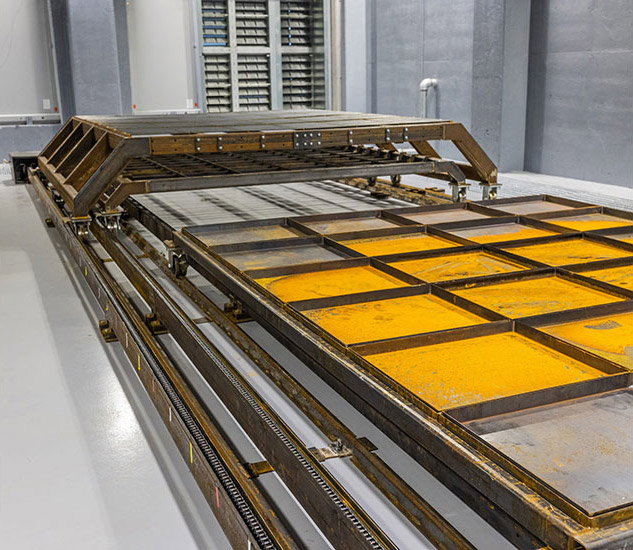
This fire testing rig checks EV batteries for flammability and combustibility. Photo courtesy TÜV SÜD America Inc.
AEM: How are you testing high-voltage components for various types of vibration and shock?
Sommer: Specially developed fixtures, designed for optimal vibration behavior, are used for the tests. Thanks to our extensive equipment, we can supply the unit with power during the test, cool or heat it, as well as carry out measurements and communicate via CAN interfaces, all according to the customer's requirements. These versatile testing options enable a precise evaluation of the resilience and functionality of components under realistic conditions.
AEM: How does TÜV SÜD use digital tools and connected testing methods to optimize your high-voltage processes?
Sommer: The centerpiece of our test stands is an automation system that acts as the “brain” of the entire test environment. All test components are integrated into this system and controlled centrally. At the same time, it collects all the data, enabling us to make the test set-up smarter and safer. This digital networking enables more precise and efficient execution of complex tests and contributes significantly to the optimization of our high-voltage processes.
Looking for a reprint of this article?
From high-res PDFs to custom plaques, order your copy today!