Leak Testing Fuel-Related Components

These test fixtures are used for fuel-related components.
Photo courtesy InterTech Development Co.
Batteries and fuel cells are cutting-edge applications in the world of automotive leak testing. But, traditional fuel-related systems are still important for internal combustion engine (ICE) vehicles.
That became evident recently in the wake of a recall order issued by Honda Motor Co. More than 700,000 cars, including Accord, Civic and CR-V models, may experience a fuel leak because of a crack in a high-pressure fuel pump.
According to the automaker, “due to a defective high-pressure fuel pump core, cracks may form inside the fuel pump. During vehicle operation, these cracks can grow, leading to possible fuel leaks; fuel smell while idling or driving; and the risk of fire, crash or injury.”
Two years ago, Ford Motor Co. issued a recall of more than 500,000 Bronco and Escape sport utility vehicles because of a fuel injector that could crack and leak fuel.
Despite increasing electrification in the auto industry, gas- and diesel-powered vehicles will continue to be produced for decades in most parts of the world. That means pumps, valves, fuel rails, fuel injection systems, storage tanks, supply lines, gas caps and other components will need to be tested for leaks on assembly lines.
“We’re seeing quite a bit of activity in this area, especially when it comes to testing components such as fuel injectors,” says Jacques Hoffmann, president of InterTech Development Co. “In particular, there’s been a lot of renewed interest and equipment upgrading associated with dry-air leak testing methods.
“We currently have a number of projects related to fuel systems,” claims Hoffmann. “That’s because fuel efficiency is critical for ICE vehicles.”
“Internal combustion engines are not dead,” adds Thomas Parker, automotive market sales manager at Inficon Inc. “In fact, some companies are actually investing in more production capacity. One of our major engine customers recently made a big investment in leak testing equipment to check high-pressure connections from the pump to the fuel rail.
“However, fuel system testing is a mature technology,” Parker points out. “The basic metallurgy and product designs behind fuel rails and connections have not changed much in the last 15 years.”
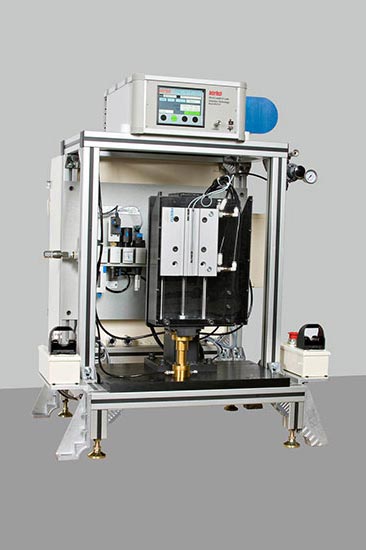
This fuel injector test stand can handle more than 350 parts per hour. Photo courtesy InterTech Development Co.
Two-Sided System
Whether they’re gas or diesel, fuel systems are composed of a storage side and a delivery side. Each has different leak rates and challenges.
The fuel storage side includes gas caps, filler pipes, level indicators and plastic injection-molded tanks. The delivery side includes fuel pumps, fuel rails and fuel injectors. Leak rates are typically tighter for those type of components, so testing processes tend to be more complex.
“Most of our customers assemble and test fuel rails in clean room environments, because particulate matter can cause these sensitive parts to clog or malfunction,” notes Parker. “Fuel rails and fuel injectors trend to be more complex than a lot of other automotive components, since gasoline is typically at a working pressure of 2,000 to 4,000 psi.”
According to Parker, helium is widely used for most fuel system leak testing applications. That’s why Inficon’s LDS3000 system is popular with many automotive suppliers.
“The need for lower fuel consumption drives the need for high-pressure fuel injection,” says Parker. “Injection pressures have significantly increased over the past few years. While gasoline fuel injection usually uses pressures up to 300 bar, diesel fuel injection pressures can reach up to 2,500 bar.”
Gasoline fuel pumps are usually spring driven, while diesel injection pumps typically use gear drives.
“Fuel pumps need to be tested for leaks by suppliers,” explains Parker. “Later in the production process, connections from the fuel pump to the fuel system must be tested after final assembly.
“Traditionally, fuel pumps have been tested in helium vacuum chambers for high reliability and high throughput,” notes Parker. “However, accumulation testing has become more popular, because it offers the same reliability and throughput at significantly lower cost.
“For accumulation testing, the fuel pump is evacuated and the evacuation pressure is held for about 2 seconds to check for gross leaks,” says Parker. “The fuel pump is then backfilled with tracer gas to an overpressure of several atmospheres and placed in a simple chamber afterwards.
“Test gas escaping through any leaks is accumulated in the chamber,” explains Parker. “The rise of concentration is converted into a leak rate by the system’s software.”

High-pressure fuel systems need to be tested for leaks to prevent safety risks and loss of engine power. Photo courtesy Marelli
Fuel Injection
Gasoline direct injection (GDI) systems offer improved fuel economy, lower emissions and enhanced engine performance, making them a preferred choice among automakers aiming to meet stringent environmental regulations.
Whether it’s a compact sedan or a pickup truck, GDI technology injects fuel into engine cylinders, where fuel is burned to produce power. A leaky fuel injector, which is a common fuel injection system problem, can significantly compromise engine performance and produce a variety of symptoms.
In a worst case scenario, an excessive fuel leak onto the hot surfaces of an engine intake manifold or engine block can cause the fuel to ignite and create a fire.
“Fuel injection components often demand 100 percent leak testing to limits as low as 0.01 sccm with cycles as fast as 2.5 seconds, while also displaying significant part temperature variations,” says Hoffmann. “Fuel injectors have been around a long time, but the designs have evolved so that they can operate at higher pressures and tighter tolerances. We see applications up to 100 bar and 3,000 psi.”
InterTech’s downstream test process features a patented mass-flow transducer to provide 10 times greater leak sensitivity than any other dry-air test method. A test part is enclosed within a test chamber and pressurized. Leakage is measured as a flow increase into the test circuit outside the part, eliminating the need and time for pressure stabilization inside the part.
“The test circuit is precisely engineered for minimum volume, enabling the sensor to almost instantaneously measure flows with a resolution of 0.0001 sccm,” explains Hoffmann.
“Critical for fast small-leak testing, all fixtures and clamping devices are designed and built for absolute stability to prevent part movement during testing,” claims Hoffmann. “Seal positioning mechanisms consistently address the test part squarely and firmly, stabilizing their closure forces quickly to shorten cycle times.
“Seals are designed for high durability to run thousands of parts per day without replacement,” says Hoffmann. “With these unique features, micro flow dry-air test systems deliver 0.01 sccm testing with less than 10 percent R&R.”
For more information on leak testing, read these articles:
How to Specify a Leak Test System
Dealing With the Helium Shortage
Leak Testing Batteries
Looking for a reprint of this article?
From high-res PDFs to custom plaques, order your copy today!