2024 Capital Spending Survey: Spending Levels Off
December 4, 2024
2024 Capital Spending Survey: Spending Levels Off
December 4, 2024The ongoing transition to EV production is spurring investment in the automotive industry.
Photo courtesy General Motors
2024 has been an up-and-down year for U.S. manufacturing. Some major manufacturers announced major layoffs. Tesla has slashed more than 14 percent of its workforce so far this year, while another EV start-up, Rivian, laid off 10 percent of its workforce. Stellantis North America laid off 400 employees in March, while General Motors let go roughly 1,000 people globally in November. Most of the latter were white-collar jobs at the automaker’s Global Technical Center in Warren, MI.
In February, German automotive supplier Continental announced plans to cut 7,150 jobs worldwide by 2025. And in March, tractor manufacturer Deere & Co. let go some 2,600 white- and blue-collar workers in Illinois and Iowa.
Strikes, too, dominated headlines. The machinists strike at Boeing this fall lasted 53 days, sending shockwaves throughout the aerospace supply chain. In July, production at GM’s assembly plant in Wentzville, MO, was halted after a four-day strike at supplier Lear Corp.
And yet, despite all that, the number of manufacturing jobs has essentially been flat. According to the Bureau of Labor Statistics, the year began with 12,966,000 people employed in manufacturing, the highest number since November 2008. In October, there were 12,873,000 manufacturing jobs, a decline of just 0.7 percent.
Presidential election years are typically slow in terms of capital investment, and 2024 was no exception. Uncertainty over economic policies and interest rates appears to have put a damper on spending.
Fewer industrial capital projects were begun in the U.S. and Canada this year compared with 2023, according to IMI Sales Leads, a consulting firm that tracks facility expansions, new plant construction, and modernization projects. The first 10 months of 2024 saw 1,412 new capital projects, compared with 1,502 new projects during the same period in 2023.
Nevertheless, the past year brought some eye-popping investments in U.S. manufacturing:
- In August, Natron Energy Inc., a manufacturer of sodium-ion batteries, said it will invest $1.4 billion to build a new “gigafactory” in Kingsboro, NC. At full capacity, the 1.2 million square foot factory is expected to employ more than 1,000 people and produce 24 gigawatts of sodium-ion batteries annually. The facility will enable Natron to increase its current production capacity by a factor of 40.
- In February, Toyota announced that it is investing $1.3 billion at its flagship assembly plant in Georgetown, KY, to produce new EVs, including an all-new, three row battery-electric SUV for the U.S. market. Four months later, the automaker said it will spend $282 million to increase production at its engine assembly plant in Huntsville, AL. The automaker is also adding more than 350 new jobs at the plant.
- In March, GE Aerospace unveiled plans to invest more than $650 million in its worldwide manufacturing facilities and supply chain to improve production and strengthen quality. Nearly $550 million will be allocated to the company’s U.S. facilities and supplier partners.
What will the coming year bring? The results of our 29th annual Capital Equipment Spending Survey point to a modest increase in investments next year.
Looking for a reprint of this article?
From high-res PDFs to custom plaques, order your copy today!
Equipment Category | % of plants to buy 2025 | % of total spending 2025 | Estimated total spending 2025 | % change in spending 2024-25 |
---|---|---|---|---|
Dispensing | 29 | 3 | 229.3 | 9 |
Multistation systems | 19 | 15 | 983.7 | 5 |
Single-station machines | 51 | 17 | 1209.9 | 13 |
Parts feeders | 22 | 2 | 103 | 1 |
Conveyors & MH | 30 | 3 | 128.3 | -24 |
Power tools | 37 | 4 | 256.8 | -3 |
Bar coding & auto ID | 42 | 4 | 257 | 6 |
Motion control | 16 | 3 | 137.4 | -20 |
Welding, brazing, soldering | 21 | 3 | 188.7 | 11 |
Robots | 26 | 13 | 719.4 | -10 |
PCB assembly | 9 | 1 | 67.9 | 13 |
Computers & software | 55 | 9 | 528.3 | -8 |
Test equipment | 40 | 4 | 277 | 7 |
Inspection equipment | 59 | 6 | 434.7 | 10 |
Wire processing | 10 | 1 | 87.4 | 3 |
Workstations | 45 | 2 | 107.3 | 5 |
Packaging | 35 | 4 | 178.7 | -21 |
Tooling | 45 | 2 | 103.4 | -14 |
Additive mfg | 45 | 3 | 204.4 | 10 |
Other | 5 | 1 | 37.4 | 1 |
Total | 100 | 6240 | 1 |
Spending to Increase
Just 29 percent of respondents will spend more on assembly technology next year than they did this year. That compares with 34 percent in last year’s survey, and it’s the lowest percentage since 2014. In fact, in the 29-year history of our survey, the “spend more” ratio has been less than 30 percent just three other times, two of which were the recession years of 2001 and 2009.
On a more positive note, 51 percent will spend the same in 2025 as they did in 2024. That compares with 44 percent in last year’s survey, and it’s the second highest percentage in survey history. In short, 80 percent of plants will spend no less next year than they did this year.
Twenty percent of respondents will spend less in 2025 than they did 2024, which is about average for our survey.

U.S. assembly plants will spend $6.24 billion on new equipment in 2025, an increase of 1 percent from 2024 spending.
Of those plants that will spend more, the average budget increase is 23 percent. Of those that plan to spend less, the average budget decrease is 23 percent.
Overall spending will not increase that much, however. Our data indicate that U.S. assembly plants will spend $6.24 billion on new equipment in 2025, an increase of 1 percent from the $6.18 billion projected to be spent in 2024.
On average, manufacturers will spend $1,194,297 on assembly technology in 2025. That compares with $1,970,582 in 2024, and it’s marks the fourth straight year that the average budget has topped $1 million. The median budget total is $250,000, which is significantly more than the $200,000 figure in 2024. In fact, it’s the largest median budget in survey history.

For the first time in survey history, the number of plants with budgets over $250,000 will exceed the number of plants with budgets under $250,000.
Aggregate budget data indicate growth in spending. For example, 42 percent of plants have 2025 capital budgets of at least $500,000, the second highest percentage in survey history. That percentage has now exceeded 30 percent for seven straight years. At the same time, 28 percent will spend between $100,000 and $499,999, about the same as in 2024. Only 30 percent will spend less than $100,000 on assembly technology in 2024. That percentage has been under 40 percent for five straight years.
“Investment was slow in our industry in 2024,” reports Glenn Nausley, president of Promess Inc., a manufacturer of servo-presses. “But, even with the slowdown, Promess was able to have a strong 2024.
“We expect an industry rebound in 2025. The main driver of this will be clarity. Uncertainty drives indecision. 2024 was a year of uncertainty, with many global influences, not the least of which was the U.S. elections. 2025 will be a year of clarity. Good or bad, things will become clearer, and businesses like clarity.”

Companies with at least 1,000 employees will account for 68 percent of total spending in 2025.

Medical device manufacturers will account for 43 percent of total spending next year. It’s the first time in survey history that the industry will account for the lion’s share of capital spending.

Any increase in spending next year will be driven by manufacturers of large products. Assemblers of products larger than 3-foot cube will account for 56 percent of total spending next year, the most since 2016.
Medical Device Industry to Increase Spending
In April, European medical device company Schott Pharma said it will invest $371 million to build a new assembly plant in Wilson, NC, to make glass and plastic syringes. At capacity, the plant is expected to employ 400 people. The new site will triple Schott’s production of glass and plastic syringes in the United States by 2030. The company hopes boosting U.S. production will reduce lead times and slash transportation costs.
Investments like that should continue next year. In fact, the medical device companies are expected to account for 43 percent of total spending next year, marking the first time in survey history that the industry will account for the lion’s share of capital spending.
On average, medical device assemblers will spend $4,220,357 on capital equipment next year, the highest average of any industry and more than three times the national average.
Certainly, sales of medical devices are expected to increase. Consulting firm Grand View Research estimates that the U.S. market for medical devices will total $256.2 billion in 2024, and it predicts that sales will grow at a cumulative annual rate of 5.9 percent from 2025 to 2030. Rising sales will be due to factors such as the growing geriatric population, high adoption of minimally invasive procedures, the increasing number of sports and road accidents, and the growing geographic reach of the market players.
Tariffs may also help prop up domestic manufacturing of medical devices and could lead to some reshoring of production. In April, the White House announced new tariffs on $18 billion of Chinese goods imported annually to the U.S. Some tariff increases that were increased this year include:
- 50 percent on syringes and needles, up from zero.
- 25 percent on respirators and face masks, up from 0 to 7.5 percent.
- 25 percent on certain steel and aluminum products, up from 0 to 7.5 percent.
Additional tariff increases are set to be phased in, including a 25 percent tariff on rubber medical and surgical gloves, up from 7.5 percent, by 2026.

Some industries are more willing to deploy used or rebuilt equipment than others. Not surprisingly, 93 percent of the equipment purchased by manufacturers of batteries, solar panels and other alternative energy products is new. Conversely, only 59 percent of the equipment purchased by manufacturers of hinges, leaf springs and other fabricated metal products is new.
Compared with other industries, medical device manufacturers are less concerned about reducing costs (38 percent vs. 53 percent for all U.S. plants) and replacing old or worn-out equipment (13 percent vs. 48 percent for all U.S. plants). But, they are more concerned about assembling new products (50 percent vs. 34 percent for all U.S. plants) and increasing capacity (63 percent vs. 53 percent for all U.S. plants).
As for cost targets, medical device manufacturers are more concerned about the cost of materials (50 percent vs. 36 percent for all U.S. plants) and scrap (75 percent vs. 46 percent for all U.S. plants) than other industries. They are less concerned about the cost of indirect labor (38 percent vs. 48 percent for all U.S. plants) and in-process inventory (13 percent vs. 23 percent for all U.S. plants), which makes sense since many medical device companies are low-mix, high-volume manufacturers.
Given the nature of their products, medical device manufacturers are not too keen on used or rebuilt equipment. On average, 84 percent of device manufacturers’ budgets will be spent on new equipment. That compares with 73 percent for U.S. plants.
When asked which processes they were most likely to automate in the coming year, medical device manufacturers are more likely to automate dispensing (63 percent vs. 27 percent for all U.S. plants), assembly (75 percent vs. 36 percent for all U.S. plants), and material handling (63 percent vs. 42 percent for all U.S. plants).

Manufacturers today are employing sophisticated materials in their products, including high-strength steel, aircraft-grade aluminum, composites and engineering plastics. Small wonder, then, that assemblers are increasingly concerned about the cost of scrap and materials.
Automotive Continues to Lead
In June, GF Casting Solutions said it will invest more than $184 million in a new manufacturing facility in Augusta, GA. The project will create 350 new jobs.
GF produces parts made from aluminum, magnesium, iron and superalloys for light vehicles, trucks, aerospace, energy, off-highway vehicles and industrial applications. The new factory will produce cast aluminum parts, with a special focus on large structural components for electric vehicles. Operations are expected to begin in 2027.
Our data indicate that capital spending should continue to be robust in the automotive industry. On average, automotive assemblers will spend $2,698,929 on capital equipment next year—more than double the national average. All totaled, the industry will account for 33 percent of all spending next year.
That said, only 21 percent of automotive assemblers will spend more in 2025 than they did in 2024, which is 8 points lower than the figure for all U.S. plants.

The automotive industry doesn’t need to add capacity. Only 33 percent of plants will buy equipment next year to increase capacity. That compares with 53 percent for the nation as a whole, and it’s the lowest percentage of any industry. In fact, the industry has held that distinction in four of the past five surveys.
Certainly, the industry doesn’t need to add capacity. Only 33 percent of plants will buy equipment next year to increase capacity. That compares with 53 percent for the nation as a whole, and it’s the lowest percentage of any industry. In fact, the automotive industry has held that distinction in four of the past five surveys.
Given the industry’s transition to EVs, it’s no surprise that 53 percent of plants will be purchasing equipment to assemble something new. That compares with 34 percent for all US plants, and it marks the second straight year in which that ratio has topped 50 percent.
Last year’s deal with the UAW might be reflected in the costs automotive assemblers are targeting for investment. Eighty percent are looking to reduce the cost of direct labor. That compares with 70 percent for the nation as a whole.
Compared with other industries, automotive manufacturers are more likely to automate welding (27 percent vs. 23 percent for all U.S. plants) and assembly (60 percent vs. 36 percent for all U.S. plants) in the coming year.
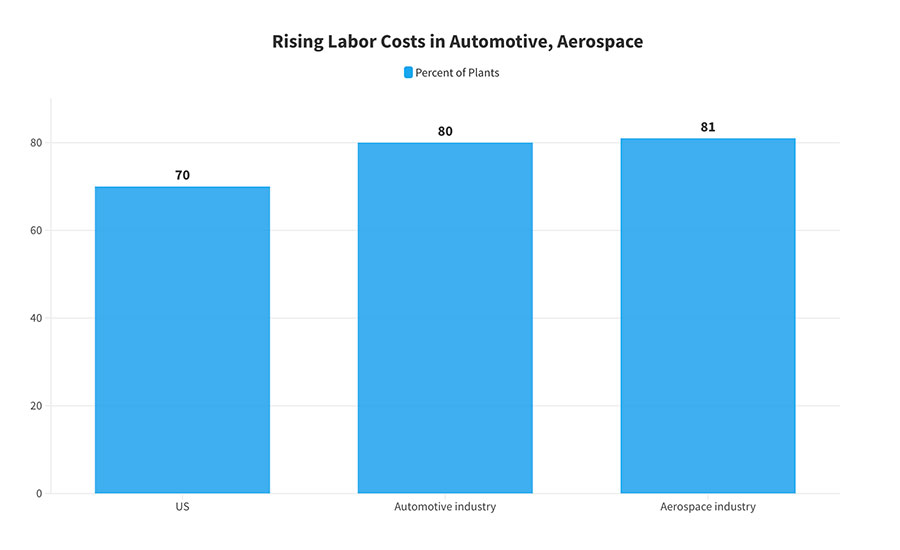
Given the recent strikes in the automotive and aerospace industries, labor costs are a growing concern. For example, 80 percent of plants in the auto industry are looking to reduce the cost of direct labor. That compares with 70 percent for the nation as a whole.
Machinery Industry Rebounds
In May, Toyota Material Handling, a manufacturer of forklifts, pallet jacks and other material handling equipment, began construction on a nearly $100 million expansion of its assembly plant in Columbus, IN. The 295,000-square-foot facility will be dedicated to assembly of electric forklifts. The investment will create 85 new jobs.
While sales of agricultural machinery may be wilting, sales of other types of machinery are doing well. For example, Grand View Research values the worldwide market for construction equipment at $207.1 billion in 2023, and it predicts global sales will increase at a compound annual rate of 8.4 percent from 2024 to 2030. Rapid urbanization in developing countries, coupled with increasing investment in infrastructure, is expected to increase demand for excavators, loaders and other construction machinery. Technological innovations, such as electric tractors and autonomous tractors, are also expected to boost sales.
After accounting for just 2 percent of total equipment spending in 2024, assemblers of lawn tractors, printing presses, photocopiers, pizza ovens, elevators, turbines and other machines will account for 12 percent of total spending in 2025. On average, machinery makers will spend $1,316,000 on new equipment next year—four times the 2024 average.
Forty-one percent of plants in this industry will spend more in 2025 than they did in 2024, the most of any industry. Only 18 percent will spend less.
Seventy percent of machinery makers, more than in any other industry, will buy equipment to cut costs, while 65 percent, another industry high, are replacing old or worn-out equipment. Like the auto industry, machinery makers are not looking to add capacity. Only 43 percent will purchase technology next year to increase output.
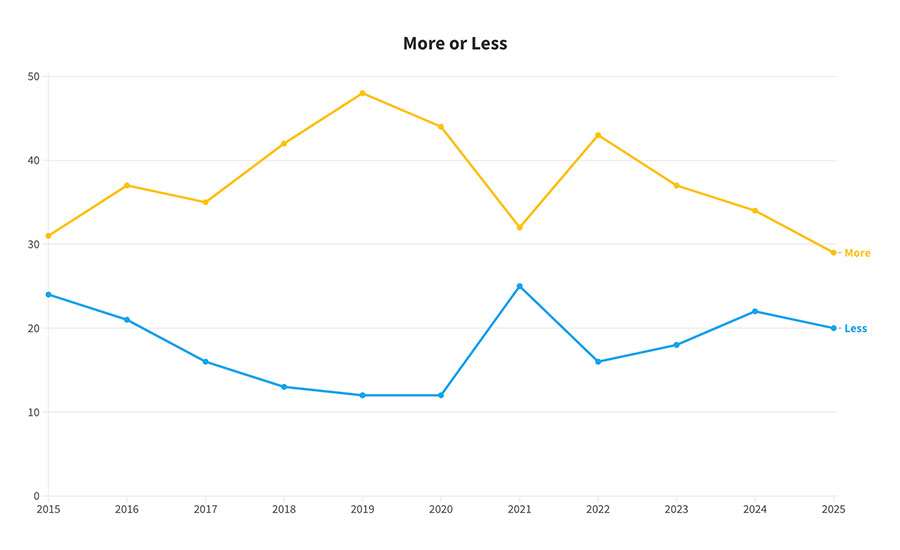
Just 29 percent of respondents will spend more on assembly technology next year than they did this year. That compares with 34 percent in last year’s survey, and it’s the lowest percentage since 2014.
Largest Companies Drive Investment
Looking at spending by company size, our data indicate that our largest manufacturers will once again dominate capital spending.
For example, 56 percent of companies with 2,501 to 5,000 employees and 41 percent of companies with more than 5,000 employees will spend more next year than they did this year. Conversely, only 25 percent of companies with 26 to 100 employees and 11 percent of companies with 25 employees or less will spend more.
All totaled, companies with at least 1,000 employees will account for 68 percent of total spending in 2025.

Large companies will be more likely to increase spending next year than small ones. For example, 41 percent of companies with more than 5,000 employees will spend more in 2025 than they did in 2024. Conversely, only 11 percent of companies with 25 employees or less will spend more.
Spending by Region
The Midwest has traditionally been the epicenter of U.S. manufacturing, and next year will be no exception. The region will account for 40 percent of spending in 2025, more than any other part of the country. In fact, the Midwest has held the lion’s share of spending for all but two years in our survey, and the region has accounted for at least 40 percent of total spending for 10 of the past 26 years.
On average, Midwestern manufacturers will spend $1,130,262 on assembly technology in 2025, the fourth straight year in which the average budget has topped the million-dollar mark.

The Midwest will account for more spending in 2025 than any other region. The Midwest has held that distinction for all but two years in our survey.
On the other hand, there’s little doubt that manufacturing investment is increasingly shifting to the South. The region will account for 32 percent of total spending next year, marking the seventh straight year the region has accounted for at least 30 percent of capital spending in the U.S.
On average, Southern assemblers will spend $1,486,000 on assembly technology next year, the largest average of any region. In fact, the South has held that honor for five of the past seven years, and the average capital budget in the region has topped $1 million for four straight years.
Single-Station Automation
Manufacturers may be less inclined to spend big dollars on assembly technology next year, but that doesn’t mean they are foregoing automation altogether. Indeed, we expect sales of single-station assembly machines—presses, riveters and automatic screwdrivers—to increase 13 percent next year, from $1.07 million in 2024 to $1.2 million in 2025.
Demand should be particularly strong for presses. Thirty-eight percent of plants—a record high—will buy presses next year. Fourteen percent of plants will buy riveters, up from 8 percent in 2024. And, 28 percent will buy automatic screwdriving equipment.
Demand should be particularly strong in the automotive, electronics and medical device industries.

When asked which processes they are most likely to automate in the coming year, assemblers overwhelmingly picked material handling.
Test and Inspection to Increase
Twenty percent of assemblers will buy technology next year to increase the quality of their products. That compares with 15 percent in 2024, and it’s the most since 2022. That goal translates to increased demand for test and inspection equipment.
Fifty-nine percent of plants—a record high—will buy inspection technology next year, up from 51 percent in 2024. We expect sales of vision systems, sensors, gauges and other inspection technology to increase 10 percent, from $395.5 million in 2024 to $434.7 million in 2025.
“2024 presented challenges due to global economic uncertainty, the automotive sector’s transition between EVs and combustion engines, and shifting dynamics in the semiconductor market,” says Frank Jakubec, global market segment sales manager for the semiconductor and electronics industry at Balluff Inc. “Despite these headwinds, we are optimistic about 2025. In machine vision, in particular, we anticipate our strongest year yet, as Balluff plans to launch the largest number of new products to date.”
Demand should be particularly strong in the aerospace, machinery and fabricated metal products industries.
Similarly, 40 percent of plants will buy test equipment next year, up from 35 percent in 2024. We expect sales of leak test instruments, function testers, wire harness testers, and other technology to increase 7 percent, from $259.4 million in 2024 to $277 million in 2025.
Demand should be particularly strong in the electronics, appliance, alternative energy and medical device industries.
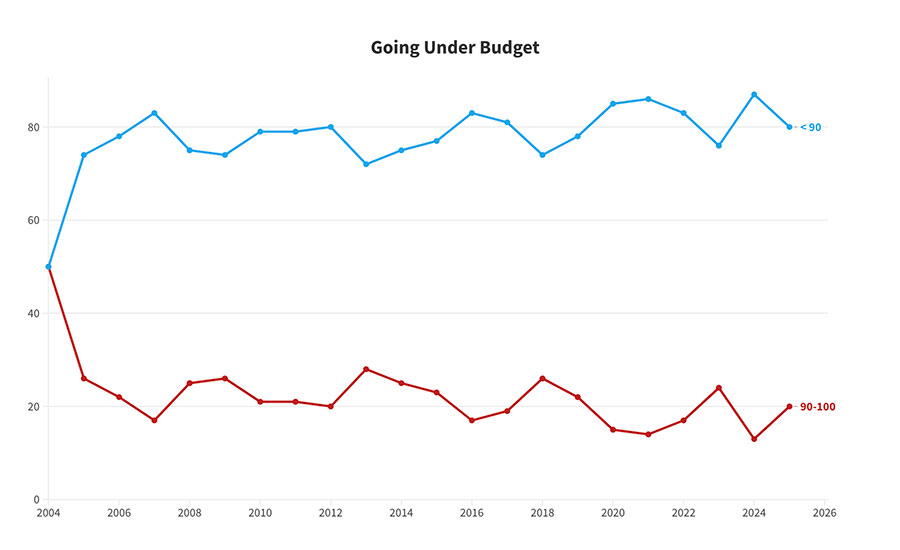
Fewer and fewer companies are spending all of the money they’ve allocated to capital projects in a given year. This year, for example, just 20 percent of plants spent more than 90 percent of their capital budgets.
Increased Demand for Auto ID
Automatic identification technology has become critical for supply chain management, warranty and recall management, and asset tracking.
2025 could be a banner year for suppliers of auto ID technology. Some 42 percent of plants will buy auto ID technology next year. That compares with 36 percent in 2024, and it’s the highest percentage in five years. We expect sales of label printers, laser engravers, bar code scanners, RFID tags and other auto ID technology to increase 6 percent, from $242.5 million in 2024 to $257 million in 2025.
“Our 2024 should be 10 percent higher than our 2023, and I would expect 2025 to increase as much as 50 percent,” says James E. Heurich, president of RFID Inc. “However, our example is an anomaly with changes in our competitors’ decisions and new product launches.”
“We are seeing a strong industry shift toward enhanced automation and quality control,” says Rob Kline, product marketing manager at Balluff. “While capital spending has been slow, we are witnessing expanded adoption of Auto ID, RFID and smart vision technologies as manufacturers seek higher levels of efficiency from their existing equipment.”
Demand for auto ID technology should be particularly strong in the automotive, appliance and electronics industries.
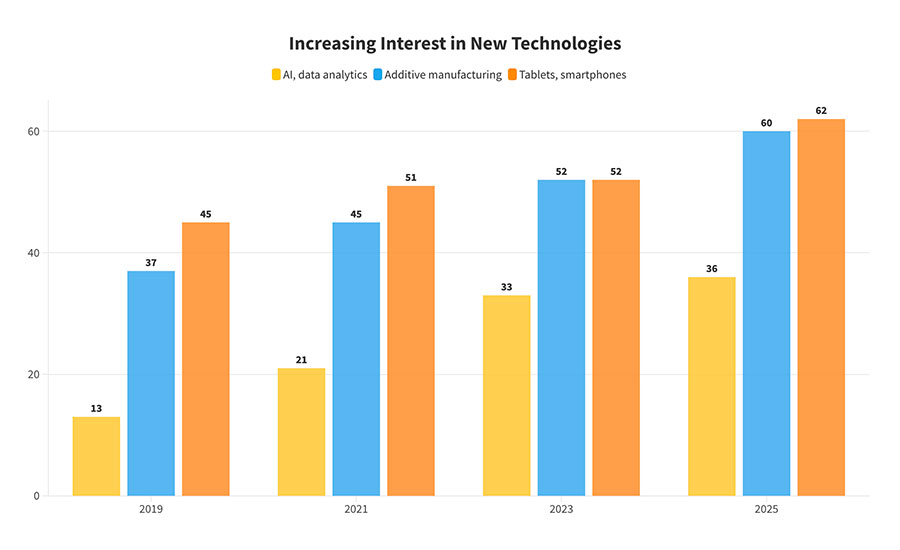
Manufacturers are increasingly adopting new technologies on the assembly line. Since 2019, the number of plants implanting AI, additive manufacturing, and tablet computers has steadily increased.
Focus on Ergonomics
Another technology that should see a gain in sales is workstations and ergonomic products. Forty-five percent of assemblers will purchase workstations next year, up from 35 percent in 2024 and the highest ratio since 2012.
Sales of workstations, lift-assist devices, supply racks and other ergonomic products are expected to increase 5 percent, from $102.2 million in 2024 to $107.3 million in 2025.
“2024 has been a good year for us,” reports Bob Simmons, vice president of Proline. “We have exceeded 2023 sales, and we still have six weeks to go. It was an odd year, however. We would have a couple of quiet days, and then several busy days. It was not smooth, but the averages were up.
“I think 2025 will be an interesting year with the new administration. If they do push for more manufacturing in the USA and put tariffs in place on imports, I think the percentage of plants that require capital equipment will be much higher than 29 percent. But, we may see a decrease in spending on the government side, as they try to get handle on deficit spending. These two factors may offset each other.”
Demand for workstations should be particularly strong in the automotive, medical device and alternative energy industries.

Manufacturers increasingly expect a quick return on capital investments. Since 2007, the percentage of plants with an ROI period of two years or more has steadily decreased.
Demand for Robots Slows
After several years of record-breaking sales, demand for robots slowed this year, according to the Association for Advancing Automation (A3). Some 15,705 robots valued at $983 million were ordered by North American companies during the first half of 2024. This marked a 7.9 percent decline in units and a 6.8 percent drop in revenue year over year.
The association blamed the decrease in significant declines in the automotive and semiconductor industries. Other industries, such as food, consumer goods and pharmaceuticals, continued to invest in robots.
“After the first quarter, members we spoke with were generally optimistic about the rest of the year,” says Alex Shikany, vice president of membership and market intelligence at A3. “While it appears there were still headwinds…in the second quarter, we continue to hear from companies [that] are optimistic about the second half of the year relative to the first half.”
Our own data indicate that robot sales will decrease next year. Between 2020 and 2024, at least 35 percent of assembly plants had robots on their shopping lists for the coming year. In 2025, just 26 percent will purchase robots. We expect sales of six-axis robots, SCARAs, grippers and other robotic technology to decrease 10 percent, from $799.4 million in 2024 to $719.4 million in 2025.
Demand for robots should be particularly strong in the automotive, medical device and electronics industries.
Survey Methodology
ASSEMBLY magazine is sent to 39,138 assembly professionals, almost all in the U.S.
The survey was conducted in conjunction with myCLEARopinion, an affiliate of BNP Media, ASSEMBLY magazine’s parent company. MyCLEARopinion is a full service, B-to-B market research company. Custom research products include brand positioning, new product development, customer experiences and marketing effectiveness solutions. MyCLEARopinion offers a broad portfolio of primary, syndicated research reports and powers the leading B-to-B panel for corporate researchers, myCLEARopinion Panel, in the architecture, engineering, construction, food, beverage, manufacturing, packaging and security industries. Learn more here.
Questionnaires were e-mailed in mid-August to a random sample of 12,254 subscribers in management positions. Thirty-seven percent of respondents were engineers; 35 percent were management; 18 percent were in quality assurance; and 10 percent were classified as design, purchasing or “other.”
The cutoff date for returning the surveys was Sept. 10. Some 234 surveys were returned for a response rate of 2 percent.
The survey was sent to manufacturers in the following industries: aerospace, electronics, appliances, fabricated metal products, furniture, machinery, medical devices, plastics and rubber products, automotive, energy and miscellaneous manufacturing.
Geographically, 16 percent of respondents were located in the Northeast, 52 percent were in the Midwest, 20 percent were in the South, and 12 percent were in the West.
Twelve percent of respondents had 25 employees or less. In addition, 22 percent had 26 to 100 employees, 26 percent had 101 to 500 employees, 10 percent had 501 to 1,000 employees, 12 percent had 1,001 to 5,000 employees, and 17 percent had more than 5,000 employees.
Twenty percent of respondents assemble products that can fit inside a 12-inch cube, 20 percent make products that can fit inside a 24-inch cube, 17 percent make products that fit inside a 36-inch cube, 22 percent make products that fit inside a 6-foot cube, and 20 percent make products that are larger than a 6-foot cube.
To purchase and download the entire capital spending report, please click here.