Automotive Stamping Line Is Fast and Flexible

When Toyota chose to set up shop in France, it wanted to design a 21st century factory that was “green, clean and lean.”
Photo courtesy Toyota Motor Corp.
The Yaris is one of Toyota Motor Corp.’s most successful vehicles. In fact, Toyota has sold more than 10 million of the subcompacts since the model debuted 25 years ago. The Yaris joins the Corolla, RAV4, Hilux, Camry and Land Cruiser as the only vehicles in the company’s portfolio to have reached the 10 million unit mark.
The 10 millionth vehicle was assembled in March 2023 at Toyota Motor Manufacturing France (TMMF) in Onnaing. Toyota’s only production site in France, the factory is located 138 miles north of Paris, near the country’s border with Belgium. Since production began in 2001, TMMF has assembled more than 4.5 million vehicles.
Employing nearly 5,000 people in three shifts, the plant assembles the Yaris and the Yaris Cross, a subcompact crossover SUV. In 2023, it assembled some 280,000 vehicles.
TMMF integrates many of the processes needed to manufacture a vehicle, from stamping to final assembly. Bumpers, dashboards and plastic trim parts are produced on site. Key components such as seats and roof linings are assembled less than 18 miles from the site. The wheels and windshields are produced at the same business park, and many other parts come from suppliers located in the region. In fact, the Yaris Cross has earned Origine France Garantie certification, meaning at least 50 percent of the unit cost price of the vehicle has been acquired in France.

The press shop produces 87 different parts. Photo courtesy Toyota Motor Corp.
Efficient Press Shop
The press shop produces 87 different parts and is one of the most impressive parts of the plant. It’s made up of four stamping presses and two cutting lines, which transform steel coils into body parts. The largest press weighs 1,567 tons and is 46 meters long. It can exert a maximum force of 4,600 tons on cold steel, 80 percent of which is produced in France.
Despite their size, the presses are fast and precise, stamping out 17 million parts annually with an accuracy of ±0.1 millimeter. A hair or a grain of dust in the die is enough to cause a defect on a part. The stamping operation consumes 300 tons of steel per day.
One of the stamping lines was designed and built by AP&T Group of Ulricehamn, Sweden, in 2019.
“We were looking for a European partner for this project, and AP&T’s modern, but mechanically uncomplicated, products were very appealing,” says Rémi Delimal, project manager of the press shop at TMMF.

Servo-driven grippers speed changeover on the press line. Photo courtesy Toyota Motor Corp.
The equipment consists of a shuttle system that receives parts from an existing transfer line and a SpeedFeeder with a servo-driven gripper for fully automatic changeover between different products. The SpeedFeeder takes parts from the shuttle system and stacks them in a fully automated pallet system. The equipment was delivered complete with a line and safety integration. The press runs at 25 strokes per minute; dual parts are produced at 23 strokes per minute. The cycle time puts high demands on the equipment.
“The high speed makes it difficult time-wise to move each part individually. Instead, several parts are stacked in a fixture, and then all are moved in a single step. The entire cycle is not allowed to take more time than it takes to fill up the fixture again,” says Peter Karlsson, key account manager at AP&T.
The short cycle time was not the only challenge posed by the project. More than 30 different parts are manufactured in the line, and changeover from one product to another must be fast. A gripper change may not take more than 180 seconds.
“We solved this issue by simply using one gripper for all of the different products. Instead of physically changing the gripper, the operator can change the programs for different products through the line’s HMI, which simplifies the process and significantly shortens the customer’s changeover timing,” says Karlsson.
AP&T did not have much time to get the operation up and running.
“For us, it was key that the installation be done when the factory was closed, so it wouldn’t impact manufacturing,” says Delimal. “We only had three weeks to get the automation equipment in place and to integrate it into our existing press line. Everything went smoothly and was finished according to plan. The equipment has truly delivered since day one of operations. It has exceeded our expectations for productivity and reliability. This was our first project together, and I must say that AP&T has done it well, from the system design to the support we get in the form of service, spare parts and technical support.”
600 Robots
The body shop is the most automated part of the assembly plant. Some 98 percent of the body-in-white line is automated with 600 robots. At certain stations, up to 12 robots work simultaneously around the same body.
The body of a Yaris consists of 300 parts assembled by the robots. In total, 3,850 weld points are made on each Yaris. On average, it takes 15 hours to produce a Yaris or Yaris Cross.
Painting is the longest step. In fact, half the production time for each vehicle is for painting. Each vehicle receives three coats of paint: a primer, the base color (a water-based paint), and a clear varnish. The workshop has 12 solid colors and 19 two-tone colors. To limit the environmental impact and waste, the robots are equipped with cartridges containing just the right amount of paint, a system patented by Toyota.
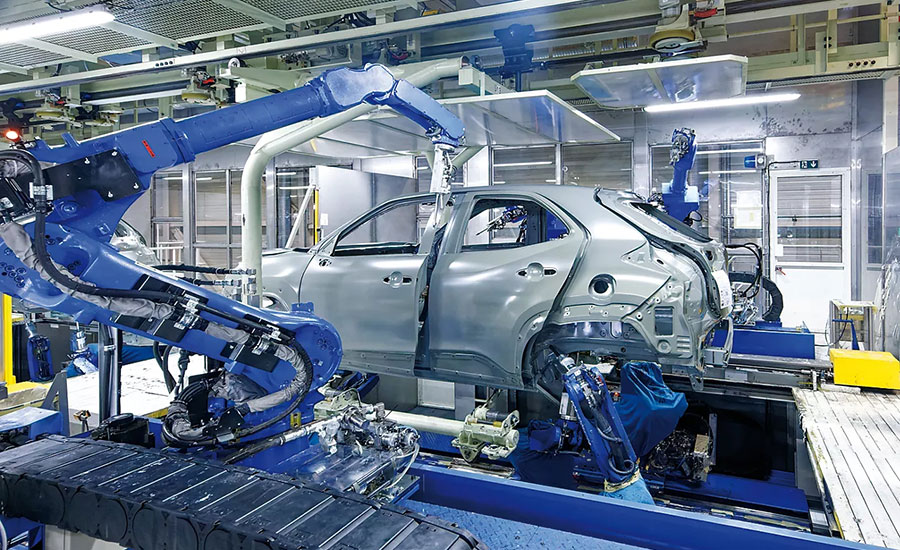
Half the production time for each vehicle is for painting. Photo courtesy Toyota Motor Corp.
Rare in the auto industry, TMMF molds many of its plastic parts. In fact, the molding shop has doubled its size and workforce with the production of the new Yaris and Yaris Cross models. The molding shop manufactures dashboards, bumpers and other parts. All these elements are painted on site. Each month, 160 tons of plastic beads are transformed into parts. The bumper is produced with a mold that weighs 25 tons and is manually adjusted to within 0.1 millimeter. The thickness of the paint is ensured to the micron.
Final Assembly
When it arrives at final assembly, the Yaris is just an empty shell, but it will leave as a finished vehicle, complete with wire harnesses, hoses, brakes, engine, windows, bumpers, wheels, seats, steering wheel, and other components. There are around 3,000 components to assemble on each vehicle. The assembly line is equipped with 1,450 screwdrivers that install 1.4 million screws daily.
Of all the areas in the plant, final assembly employs the most people. Interestingly, 30 percent of the staff in final assembly are women.

The assembly line is equipped with 1,450 screwdrivers that install 1.4 million screws daily. Photo courtesy Toyota Motor Corp.
The logistics department receives all the parts for manufacturing, stores them and supplies them to the line in a just-in-time manner. This is TMMF’s largest department. Spanning 40,747 square meters, it’s as large as six soccer pitches. Some 250 trucks pass through its 28 unloading docks daily.
Parts come from 200 suppliers and are delivered in standardized blue plastic boxes, which travel back and forth between suppliers and the plant. This eliminates the need for cardboard boxes and wooden pallets. The logistics prep area has a reserve of parts for less than two hours of production. All totaled, the plant receives some 3.8 million parts daily.
At the end of the line, inspection teams perform various static checks and dynamic performance tests. Each vehicle is checked throughout each manufacturing stage. The process includes 2,500 inspection points.
In addition, 2,400 vehicles are sampled each year at the end of the line for a more in-depth check. During this operation, 6,000 points are checked. This check lasts, on average, 1 hour 40 minutes per vehicle.
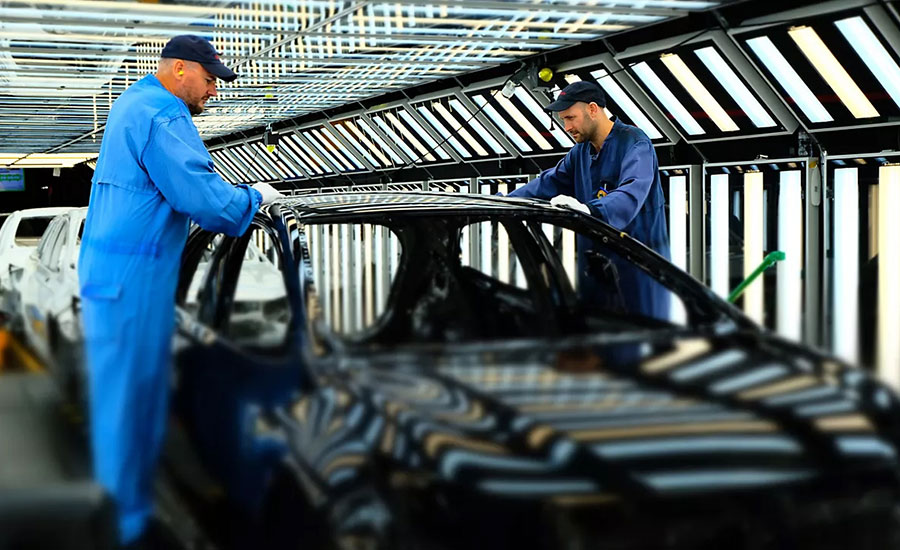
At the end of the line, inspection teams perform various static checks and dynamic performance tests. Photo courtesy Toyota Motor Corp.
Green and Lean
When Toyota chose to set up shop in France, it wanted to design a 21st century factory that was “green, clean and lean.”
The campus buildings cover just 17 hectares, 30 percent less than a comparable site. The campus has its own water treatment plant capable of managing the annual effluent equivalent to a town of 15,000 inhabitants. Four regenerative incinerators make it possible to reduce atmospheric pollution by 99 percent.
Since 2007, all of the company’s waste has been recycled. Whether industrial or domestic waste, all waste produced by the site has a second life. This is the case for scrap steel, which goes back to the steelworks to be recycled, or even for sludge generated by the paint shop, which is recycled in a cement plant. Since the release of the first Yaris, no waste has gone to landfill.
TMMF has two, large rainwater collection basins of 16,000 cubic meters, the equivalent of six Olympic swimming pools. This equipment allows it to optimize its water needs. In 20 years, water consumption per vehicle produced has fallen by more than half, falling below the symbolic bar of 1 cubic meter of water per car. This makes it one of the most successful European automotive sites in this field.
In 2013, for 333 days, TMMF achieved a feat. Its installations were able to operate without purchasing industrial water from the public network, only using rainwater reserves and water recycled by the factory.

Since January 2019, TMMF has consumed 100 percent renewable electricity. Photo courtesy Toyota Motor Corp.
Heating of the painting and plastic shops is carbon neutral, thanks to the use of green energy. In the plastics workshop, painting booths are powered by four heat pumps.
Since January 2019, TMMF has consumed 100 percent renewable electricity, just like eight other European Toyota sites. In 20 years, TMMF has reduced its energy consumption and carbon emissions by more than half.
For more information on stamping presses, read these articles:
Hydraulic Presses Form Eco-Friendly Hangers
Press Hardening Forms Strong, Lightweight Parts
New Automotive Press Line Will Be Accessible for Disabled Workers
Looking for a reprint of this article?
From high-res PDFs to custom plaques, order your copy today!