Mixed-Model Lines Enable Multiple Power Train Configurations

Flexible assembly lines enable automakers to quickly ramp up or cut back electric vehicle production as market conditions dictate.
Photo courtesy Stellantis
Automakers around the world are faced with an unprecedented production challenge. They’re scrambling to operate flexible assembly lines that can produce both gas- and battery-powered vehicles simultaneously, while ensuring productivity and quality goals.
Flexibility has become strategically important today, enabling companies to quickly ramp up or cut back electric vehicle production volume.
Assembling different power train variants demands efficient use of floor space and parts, in addition to cross-trained operators. As EVs evolve, market conditions will fluctuate over the next decade, so automotive engineers must be prepared to tackle continuous line balancing issues.
According to Drew Locher, a lean manufacturing expert and director of Change Management Associates, “mixed-model assembly” is defined as producing relatively short runs or low volumes of different products on the same production line or equipment in the same shift or day.
“It poses a challenge for most organizations, due to the relatively high variability that arises,” claims Locher. “One of the key characteristics of a lean, mixed-model assembly line is outstanding workplace organization, and the ability to change over quickly. This isn't always just about equipment changeover, but also materials and staffing.”
Mixed-model automotive assembly plants must have the workstations, tools and components necessary to efficiently build hybrids in the same facility as electric and internal combustion engine (ICE) vehicles. However, assembling cars with different power trains is much harder than making multiple types of pens, syringes or toothbrushes on the same assembly line.
“Conceptually, mixed-model assembly is the same in all industries,” says Art Smalley, president of the Art of Lean Inc., and a former engineer at Toyota Motor Corp. “You are trying to assemble different models of the product on the final assembly line as smoothly and efficiently as possible.
“The size and scope of an automotive assembly line tends to present some unique challenges,” warns Smalley. “There are up to 10,000 parts in an automobile, and many of them are quite large and heavy. There are also usually many subtypes of the same product being manufactured.”
“While the fundamental concepts are similar, mixed-model automotive manufacturing tends to look significantly different than other sectors,” adds Michelle Drew Rodriguez, a partner at consulting firm Roland Berger. “This is due to the higher complexity from high variation at the material and process level, a higher volume of suppliers and limited ability to make quick adaptations in existing lines.
“It’s important to achieve high process standardization while working within existing plant layout constraints,” explains Rodriguez. “Another consideration is obtaining the required capital to develop truly agile mixed-model lines, especially because mixed-model lines need much higher expenditures than dedicated lines.
“Even with these challenges, more automotive players will develop mixed-model assembly lines, as they increasingly will need flexible production to meet changing customer and regulatory needs,” says Rodriguez.
“Mixed-model assembly is used regularly across industries, most notably the discrete electronics industry where products such as smart phones with multiple form factors and internal configurations are manufactured,” notes Khalid Sebti, executive vice president and managing director of Capgemini Engineering. “Use in the auto industry is different, but not necessarily more complex, due to designs shifting to multi-use platforms to accommodate different power train options.
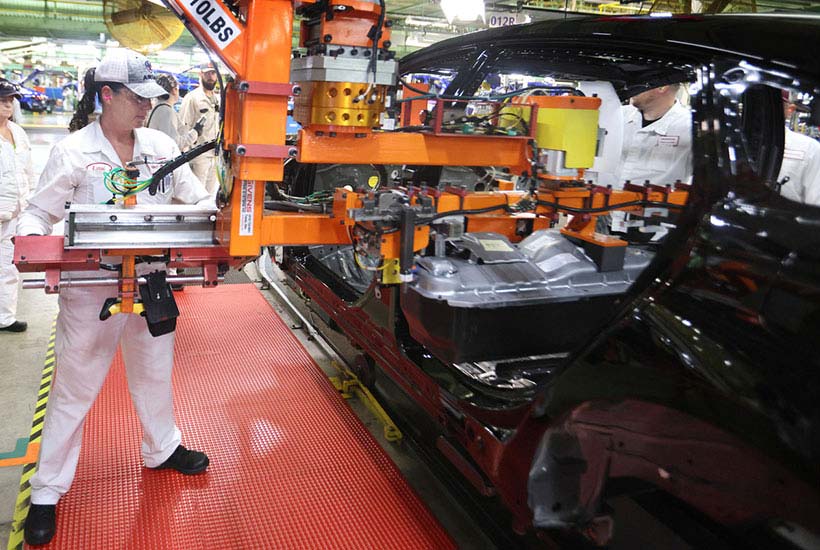
Assembling different power train variants demands efficient use of equipment and floor space. Photo courtesy Honda Motor Co.
“The shift from traditional [in-floor, chain-driven] assembly lines to automated guided vehicles allows for flexibility in handling different vehicle platforms, ultimately making strides in error proofing and operator training across the assembly landscape,” Sebti points out.
“However, there are several key challenges associated with implementing mixed-model assembly lines,” says Sebti. “The biggest challenge is the effort required to upskill the existing workforce to handle a different product mix.
“Organizations also struggle with the availability of consistent and single-source truth in product data across CRM, ERP and MES systems,” claims Sebti. “That issue is not unique to mixed-model production environments, but is amplified [more than with dedicated vehicle assembly lines].”
Flex Quest
Key characteristics of a lean, mixed-model assembly line include low changeover time (ideally zero) at all workstations; the ability to present or sequence all parts to the line just in time; level scheduling practices; efficient material handling routes with short replenishment times; responsive suppliers; and a skilled labor force.
“For a high performing mixed-model assembly line, high flexibility and the ability to respond to product mix demand changes are table stakes to better utilize resources and ultimately drive business success,” says Sebti. “Other characteristics include more sophisticated production scheduling and planning systems, modular and flexible workstations, and an adaptable workforce.”
“The big challenge is materials,” adds Locher. “How different are they between power trains and how do you get them to the point of use? Presentation of parts to the line is critical. If possible, it’s a good idea to keep variations to a minimum.

Increasing complexity on assembly lines can cause workload imbalances. Illustration courtesy Boston Consulting Group
“Line balancing and line layout are also important things for engineers to consider,” says Locher. “All of the different scenarios need to be worked out ahead of time. You need to maintain balance to maximize flow and minimize waste.”
“Small mixed-model lines with fewer parts to assemble often take the shape of an L- or U- shaped cell,” adds Smalley. “That allows operators to work more closely together and allows parts to be delivered to the outside of the line so their work is not impeded. However this is [typically used] for smaller subassembly and for teams of 10 people or less.
“The layout for a final car assembly line can be thousands of yards in length and is moved by a conveyor system of some type,” explains Smalley. “In this case, there is no U-shaped cell and hundreds of people broken up into teams work in different sections. On these longer assembly lines, workers are more spread out, so much thought has to be given to different takt times and material presentation options.”
Mixed-model assembly lines typically also need to be laid out differently than lines that only produce one type of vehicle.
“To accommodate for the potential wide variation in the manufacturing process for different models and avoid impact on cycle time, [production] lines need to have flexibility to quickly adapt layout,” says Rodriguez. “[This] often is through adjacent workstations (either horizontal or vertical) that allow for increased time required, completing additional steps needed or managing new material flows required.”

A new “marriage” workstation and automated screwdriving system enables vehicles equipped with multiple power trains to be assembled in the same facility. Photo courtesy Porsche AG
“A concept that is rising in prominence in automotive manufacturing is ‘unboxed’ assembly, which prioritizes complete build-out of key systems and then brings them together for final assembly,” Rodriguez points out. “This supports [smaller] footprint requirements and more efficient manufacturing.”
Rodriguez believes that one of the biggest mistakes automotive engineers can make when setting up mixed-model assembly lines is not building enough layout flexibility. “Space availability and layout flexibility are needed for adding in required additional substations to maintain consistent cycle times,” she explains.
“An additional mistake would be not planning for increased quality focus,” says Rodriguez. “Rework rates are typically higher for mixed model lines vs. dedicated lines.
“There is no limit on how many different car models can be made on the same assembly line,” claims Rodriguez. “The constraining factor is how much time product changeovers take, the impact on overall line productivity, and the ability of the workforce to manage different models.”
“Engineers with a lack of understanding around the manufacturing bill of process are likely to produce an over-constraining design that requires complexity in tools, fasteners and torques,” adds Sebti.
“Engineers may also face inadequate production planning for material handling and assembly processes, improper production process sequencing and scheduling, insufficient quality control systems during production processes, insufficient attention to line balancing and even insufficient time budgeted for changeovers,” notes Sebti.
“Keeping a close eye on these issues can make all the difference in the overall success of a mixed-model assembly line,” says Sebti.
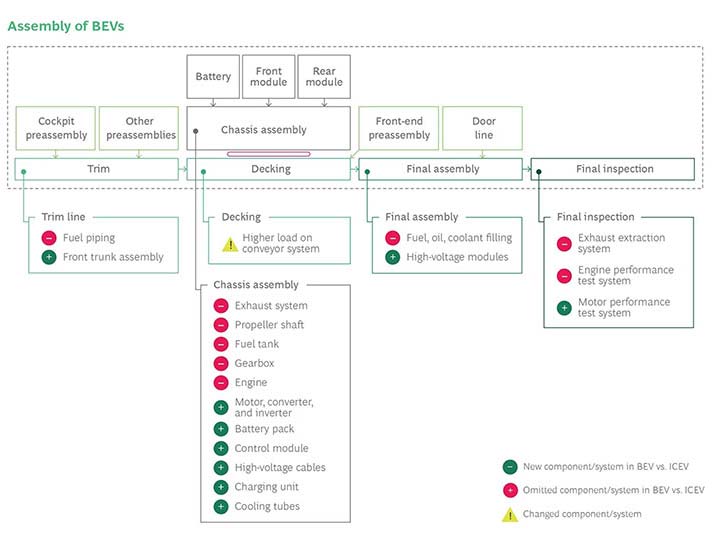
There are key differences between assembling gas- and battery-powered vehicles, such as a unique set of components. Illustration courtesy Boston Consulting Group
Mixed-Model Assembly in Action
Making different types of vehicles on the same assembly line is nothing new. Automakers such as Toyota mastered the art of flexibility several decades ago by applying lean production principles.
However, the concept of building a full line-up of vehicles on the same line is a newer phenomenon. Ford Motor Co. pioneered an integrated production strategy at its Michigan Assembly Plant more than a decade ago, when it became the first facility in the auto industry to build three different types of electrified vehicles alongside traditional gas-powered cars.
BMW claims that its 101-year-old flagship factory in Munich is even more flexible. It can produce gas, hybrid, electric and hydrogen fuel cell models on a single assembly line.
Companies such as Honda, Stellantis and Volkswagen are currently investing in flexible factories. That’s because it’s typically cheaper to operate a flexible factory than to build a new facility that only builds EVs.
Stellantis recently announced that it plans to invest more than $406 million in three Michigan facilities to support its multi-energy strategy and confirmed that the Sterling Heights Assembly Plant will be the company’s first U.S. factory to build a fully electric vehicle. Starting next year, the Ram 1500 REV and the 1500 Ramcharger will be built alongside existing ICE models.
Stellantis partnered with equipment suppliers to carefully plan and execute the installation of a new conveyor system and new automation for EV-specific production processes. It also retooled and rearranged workstations to be able to produce multiple pickup truck models on the same assembly line.
In addition, Stellantis invested more than $97 million in its Warren Truck Assembly Plant for production of a future electrified Jeep Wagoneer, one of four EVs that will be launched globally by the brand before the end of 2025. Electrified models will be built on the same line as ICE versions of the Jeep Wagoneer and Wagoneer L, as well as the Jeep Grand Wagoneer and Grand Wagoneer L.
After Honda finishes retooling its flagship facility in Marysville, OH, it will have the flexibility to produce both ICE and EVs on the same assembly line. A key part of the transformation has involved line consolidation.
“Our efforts…are not focused simply on EV production, but on fundamentally reimagining our approach to manufacturing,” says Mike Fischer, executive chief engineer and Honda EV Hub lead.
“The Marysville Auto Plant recently consolidated its two production lines, tearing out much of line to enable production of both EVs and ICE vehicles on the same line,” Fischer points out. “The additional space will be used to improve the ease of movement for people on the line and the efficiency of line-side parts delivery and staging for assembly of both ICE vehicles and EVs, as well as the expansion of the vehicle quality area to verify software-dependent vehicle functions.”

This flexible factory can produce gas, hybrid, electric and hydrogen fuel cell models on a single assembly line. Photo courtesy BMW AG
“[We are] transforming the production environment by reducing complexity on the main production line, which enables process layouts that reduce walking required for [operators],” explains Fischer. “By changing the flow of certain installation processes, the team is increasing the space allotted for parts delivery and staging to create an optimized, associate-friendly environment.”
Volkswagen Group’s Porsche division has retooled its 22-year-old factory in Leipzig, Germany, to produce three different drive types on a single assembly line: gas, hybrid and electric. The biggest change involved the workstation that performs the “marriage” between the chassis and body of Macan and Panamera models.
“We realized we would have to completely revise the existing marriage and many other workflows at the plant,” says Sebastian Böttcher, an engineer who worked on the project. “An additional type of power train is like a little world of its own, with new requirements, special procedures and special tools.”
One complex problem that Böttcher and his colleagues had to solve involved fastening. The marriage of a gas or hybrid vehicle requires the underbody and chassis to be screwed together in 20 places. However, in the all-electric variant, there are 50 joints that need to be tightened.
To address the challenge, the Porsche engineers had to reinvent the marriage process. What was previously four assembly stations stretching across 79 feet of floor space became nine stations across 197 feet. Six additional robots and 18 automatic screwriving stations were incorporated.
The engineers also developed an automatic screw loading system that, depending on the product line and fittings, can handle any screw size and shape, torque and angle at high speeds. A measuring device regularly passes along the assembly line to check the screw spindles during ongoing production operations. As a result, there are virtually no idle times or delays.
In addition, a special camera system was installed to examine the surface of the electric vehicles’ high-voltage batteries for foreign objects like mislaid washers or nuts.
“All in all, we have created a highly productive system which has been seamlessly incorporated into all the plant workflows,” says Böttcher.
Learn more about mixed-model assembly:
Mixed-Model Assembly Is Key to Profitability
How to Balance Assembly Lines
Lean Plant Layout
Looking for a reprint of this article?
From high-res PDFs to custom plaques, order your copy today!