New Software Promises to Increase Quality, Flexibility and Resilience

Photo: gorodenkoff / iStock / Getty Images Plus
In the factory of the future, software will be every bit as important to product assembly as robots, riveters and nutrunners. Software is helping manufacturers with a range of applications, from error-proofing individual workstations to analyzing the performance of assembly lines or entire plants.
Whether you’re looking for enterprise resource planning software or digital work instructions, you’ll find it at The ASSEMBLY Show. Here’s a look at some of what’s on offer.
MOM Software Includes Lean Material Management Tools

FactoryLogix manufacturing operations management (MOM) software now includes a comprehensive manufacturing material management suite, “Lean Material Management Anywhere.”
A single web-based architecture supports any mix of cloud, hybrid and on-premises software services, with no need for software installation, configuration or maintenance on clients, eliminating significant risk and cost of ownership. Each client has an open choice of devices and operating systems as deemed appropriate for each user instance. Self-configurable interfaces focus on users’ specific roles, satisfying specific use-case requirements.
The software features many key material management functions within a single web-based environment, including material receiving, inspection, warehouse and local storage management, logistics operations decision and control, and automation of lean material management. Continuous monitoring of material consumption and spoilage enables the software to precisely govern inventory management levels, with accountability back to ERP for each individual piece of material, with full “digital thread” traceability. Booth 1323
Aegis Software Co.
www.aiscorp.com
Software Creates Work Instructions From PLM Data

Canvas GFX has released a new software development kit (SDK) for its flagship platform Canvas Envision. With the Envision SDK, users can build authoring and viewing experiences customized to their specific use-cases, and integrate those experiences into other platforms, including PLM, PDM and MES.
Envision integrates with PLM software, enabling anyone to create and consume interactive digital instructional documents that leverage up-to-the minute design data. Envision lets users turn CAD data and other information from PLM software into intuitive and easy-to-consume content that meets the unique requirements of all stakeholders in manufacturing. This desktop graphics application gives everyone the ability to leverage 3D CAD models to create interactive visual documents. With Envision, manufacturers get easy-to-use 3D visualization combined with text layout, 2D drawing tools, vector graphics and photo editing, and a host of smart tools and features to help them visually communicate information about their products. Booth 1241
Canvas GFX Inc.
www.canvasgfx.com
Software for Intelligent Curve Analysis

Many manufacturers rely on accurate measurement and evaluation of curve values and time series data for quality assurance and process optimization. However, traditional analysis methods often fall short. Curve Anomaly AI is an advanced, artificial intelligence-based system for curve analysis. By harnessing sophisticated AI algorithms, the software analyzes the entire progression of curve values and time series data, enabling early detection of anomalies and anticipating potential quality issues.
The software rapidly analyzes thousands of curve data points within minutes, automatically detecting anomalies and providing comprehensive evaluation beyond the capabilities of manual inspection. With this software, manufacturers can automate outlier detection, eliminating human error and ensuring no critical anomalies are overlooked.
Results are displayed on an intuitive dashboard for real-time monitoring and quick decision-making. The scalable system accommodates growing production demands without compromising accuracy or speed. Users can navigate from a panoramic view down to specific data points for precise information extraction and analysis. Booth 1548
CSP US Inc.
www.csp-sw.com
Assembly Work Instruction Platform
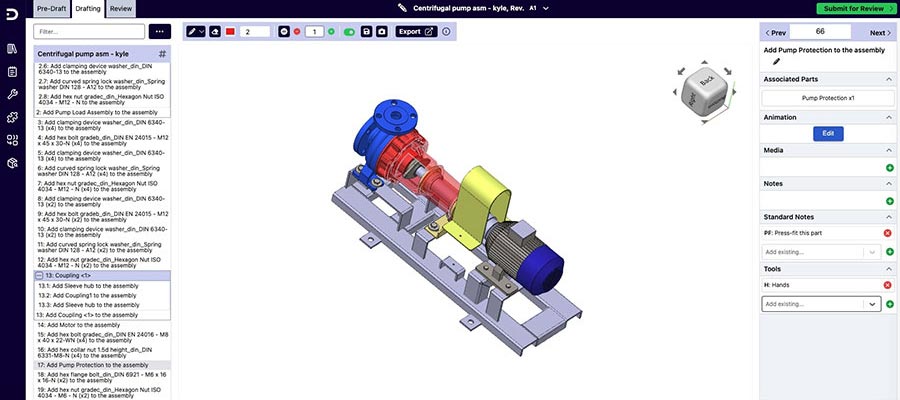
BuildOS software automatically generates assembly work instructions directly from CAD files. Traditional methods of creating assembly work instructions are often manual, time-consuming, and prone to error. BuildOS revolutionizes this process by reducing the time required to produce high-quality work instructions by a factor of 10.
BuildOS allows technicians to interact with 3D assembly models directly within the Technician Viewer, ensuring they have the most accurate, up-to-date information at their fingertips. Additionally, instructions can be easily exported to PDF, GIFs, or Word documents, offering flexibility in how teams access and utilize information.
The platform doesn’t just create work instructions—it optimizes them. The software assists in automatically determining the most efficient assembly order, reducing errors and ensuring that production runs as smoothly as possible.
The software goes beyond basic instruction creation by capturing and applying the tacit knowledge of your manufacturing team. It automatically associates notes, tools and best practices with specific parts, ensuring that this valuable information is preserved and utilized across the organization.
The software addresses the challenge of managing revisions and maintaining traceability. The platform’s ability to compare changes between models ensures that updates are accurate and that all team members are working from the latest information. Booth 839
Dirac Inc.
www.diracinc.com
Real-time Asset Tracking and Management

Kinexon RTLS Air is a highly scalable industrial asset tracking and management system. It enables a wide range of use cases from “search and find” to complex inventory management and offers centimeter accuracy due to ultra-wideband (UWB) technology. Its adaptive energy profiles ensure best-in-class efficiency and minimal maintenance. With indoor and outdoor options available, the system provides real-time location, streamlining end-to-end industrial asset tracking and inventory management in a cost-effective manner.
Thanks to its cloud-based nature, Kinexon RTLS Air is a plug-and-play system requiring minimal IT integration efforts. With an “as-a-service” business model, it ensures an ROI payback period under 12 months with 70 percent less costs than other RTLS systems
Seamlessly integrated with the Kinexon OS software platform, Kinexon RTLS Air enables automated operations and seamless integration with ERP and warehouse management systems. Booth 905
Kinexon
https://kinexon.com
MES Software Works With ERP Systems
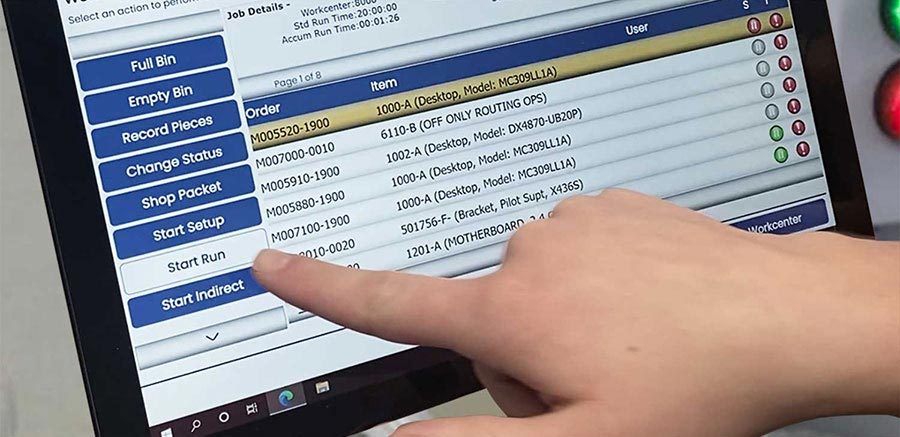
The MV2 manufacturing execution system brings together disparate systems on the plant floor. By being the central hub of information, MV2 can increase production efficiency by coordinating functions and consolidating information in one location.
MV2 is compatible with enterprise resource planning systems. The MES takes in order details, worker information, bills of materials, routings, schedules, and warehouse and inventory information directly from the ERP system to help managers plan. The software also returns shop-floor information to the ERP system, including labor tracking, machine tracking, inventory usage and movement, receipts, and production status. This information is critical for forecasting and estimating jobs, as well as to keep sales and purchasing up to date on manufacturing performance.
MV2 brings together data from sensors, people and machines for a holistic analysis of plant operations. The system’s inherent interconnection capabilities digitally unite departments with real-time data exchange.
Managers can visually plan production operations with drag-and-drop capability; see the status of jobs as they move through production; and filter orders and operations to identify operational performance issues.
With an electronic kanban system, engineers can manage the “pull” process and analyze historical performance data. Digital kanban boards are updated in real time, and managers receive notifications immediately when thresholds or events are met. Through dashboards, managers can monitor work center conditions and productivity in real time. They can review historical changes in production metrics to locate trends or issues as they develop. Dashboards can be viewed on a desktop or on production boards throughout the facility.
MV2 provides the ability to manage work instructions from a single location to reduce errors and confusion. Instructions can provide 3D files, videos and other information at the touch of a button. Work instructions travel with jobs automatically, eliminating paperwork routing and version control.
Downtime reporting can be done by end users or directly from machines. The software can notify key personnel immediately when downtime starts, and it retains historical records of downtime events for future analysis.
The software’s quality module records and manages testing operations across the shop floor, including components and materials testing during receiving, finished goods quality control, and testing during production. The software can notify personnel when testing metrics exceed thresholds. Booth 1638
Paper-Less LLC
www.paperlessllc.com
Looking for a reprint of this article?
From high-res PDFs to custom plaques, order your copy today!