2024 Plant of the Year
GE Appliances Uses Advanced Automation to Dish Out Productivity
October 1, 2024
2024 Plant of the Year
GE Appliances Uses Advanced Automation to Dish Out Productivity
October 1, 2024The 2024 Assembly Plant of the Year recently launched new products to keep up with changing market conditions.
Photo courtesy GE Appliances
As anyone who has ever cleaned up after a family party knows, dishwashers are one of the unsung heroes of the American home. The machines magically transform dirty glasses, plates and silverware into spotless specimens of domestic hygiene.
Many of those dishwashers are produced at a sprawling assembly plant in Louisville, KY, operated by GE Appliances, a Haier company. Ever since Dwight D. Eisenhower was president, Appliance Park’s building 3 (AP3) has housed a state-of-the-art factory.
Today, the 1-million-square-foot facility produces more than 70 dishwasher models. It also excels at launching new products to keep up with changing market conditions and consumer tastes.
The flexible, vertically integrated facility recently underwent a digital transformation that has improved productivity, boosted quality and reduced time to market.
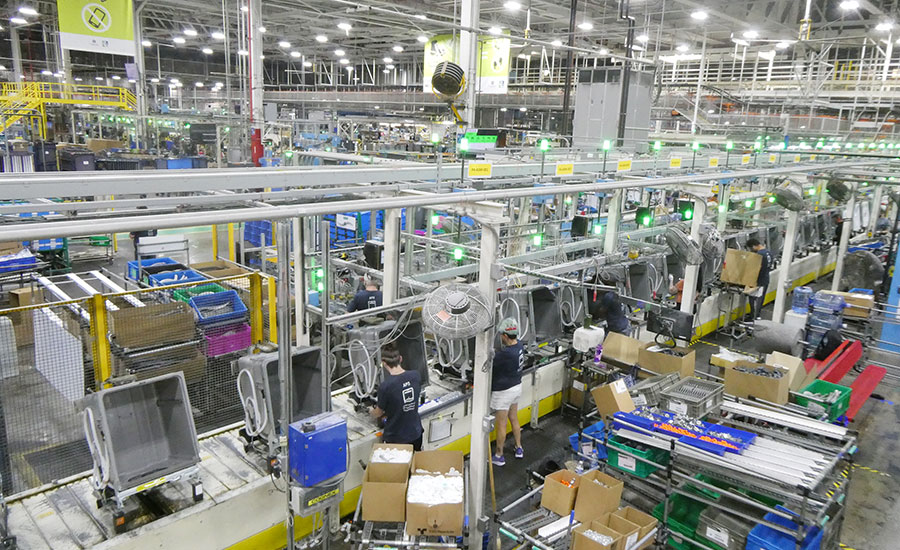
The 2024 Assembly Plant of the Year produces more than 70 different types of dishwashers. Photo by Austin Weber
Old Plant, New Lines
Two new dishwasher assembly lines complete a $450 million investment announced in late 2021 at Appliance Park. The 750-acre complex, which serves as GE Appliances’ headquarters, comprises a product development center, five large factories and a huge warehouse. In addition to dishwashers, the campus mass-produces dryers, refrigerators and washing machines.
The assembly plants have received significant upgrades over the past two years with new top-load washer models and four-door refrigerators added, as well as new production lines and fabrication equipment. The dishwasher expansion alone positions AP3 to become the largest plant of its kind in the United States. Over the past six years, GE Appliances has significantly increased volume at the dishwasher factory.
“We are committed to U.S. manufacturing,” says Kevin Nolan, president and CEO of GE Appliances. “From design to production, our team is always finding a better way to bring the latest appliance technology to homes and families across America. Together, with our state and local partners, we are building a stronger economy and community.”
Looking for a reprint of this article?
From high-res PDFs to custom plaques, order your copy today!
The technology upgrades have benefited workers too, leading to a 47 percent decrease in ergonomic injuries. GE Appliances’ investments have been fueled by a heavy use of data to identify growth constraints and drive investment projects.
“The appliance industry is crowded and often-times commoditized,” explains Bill Good, vice president of supply chain at GE Appliances. “That can lead to promotion-driven revenue battles. With our focus on variable cost productivity and assembly operations improvement, we are generating year-over-year improvements that enable our sales teams to compete and grow the business.

Over the past six years, the plant has experienced a significant increase in volume. Photo courtesy GE Appliances
“Additionally, given the innovation of our new products and improved quality, our brand strength continues to grow, which will position us well in future business cycles,” says Good. “Major investments in new product launches, assembly lines, presses, robotics and automation, and digital technology have yielded impressive gains in safety and employee experience, product quality, capacity, efficiency and cost reduction.
“The transformation was driven by two major new product introductions,” notes Good, who previously served as plant manager at GE Appliances’ refrigerator factory in Decatur, AL. “For both programs, the AP3 manufacturing team (operations, quality, advanced manufacturing engineering, advanced quality and materials) integrated closely with our technology team.
“They reduced total part count, developed common parts used for multiple brands and platforms, reduced complexity and improved ergonomics for our operators, and installed best-in-class assembly lines and automation,” notes Good.
That’s why GE Appliances’ dishwasher factory is the recipient of the 2024 Assembly Plant of the Year award sponsored by ASSEMBLY Magazine. The world-class facility was chosen for the 21st annual award because the 71-year-old plant has been modernized with a variety of state-of-the-art production tools and technology. The innovative facility excels at using automation and robotics, in addition to deploying the latest digital manufacturing processes.
“We may exist in the same building, but everything about the process and layout has changed,” says Tim Vibbert, executive director and plant manager. “Every inch of this factory has been improved and renovated in the last eight years. Today, there are more assembly lines, more complexity and more material movement than in the past.
“One thing that makes AP3 unique is its designation as a ‘supersite,’ meaning that the vast majority of all dishwashers we sell, and all five brands under the GE Appliances House of Brands, are made right here,” notes Vibbert. “Versus our peers within GE Appliances, we have a similar number of operators and output, but have a significantly higher amount of automation.
“AP3 is currently being used as a benchmark within GE Appliances with respect to productivity, manufacturing process elimination and operational cost,” adds Vibbert, a U.S. Army veteran and West Point graduate who previously served as plant manager of the nearby laundry products facility. “We’ve organized our teams and developed a distinct set of collaborative metrics to tackle industry pressures, while still delivering cost out. In addition, we are the pilot site for new systems, like our latest activities in material flow.”

Dishwashers today are more complex than ever. Photo courtesy GE Appliances
Proud Heritage
GE Appliances and its legacy companies have been making appliances for more than 110 years. In the early 1900s, engineers at General Electric Co. began developing newfangled devices to improve dreary household chores related to cleaning and cooking.
Around the same time, a pair of brothers in Syracuse, NY, created the world’s first electric dishwasher. After receiving widespread interest in the contraption, Forrest and Willard Walker began manufacturing the machine in the back of their small hardware store.
In the late 1920s, the Walkers sold their fledgling company to GE, which moved dishwasher production to its Hotpoint division factory on the West Side of Chicago.
The first GE-branded dishwashers debuted in 1933 at the Century of Progress world’s fair in Chicago. They featured a square tub, a single control handle, a rubber-coated steel dish rack and an automatic water level measuring valve. The top-loading machines wowed visitors to the GE pavilion and the popular House of Tomorrow.
GE’s first front-loading dishwasher appeared in 1936. That trendsetting product was eventually followed by many other innovations, such as the Mobile Maid automatic dishwasher in the mid-1950s, which boasted “roll-around convenience.” Other machines with names such as Empress and Princess soon became available in trendy coral color schemes.
After World War II, GE correctly anticipated that there would be unprecedented demand for dishwashers, ovens, refrigerators, washing machines and other types of electric appliances. To address the issue, it purchased more than 900 acres of farmland on the southeast side of Louisville in 1951 and created Appliance Park.
In early 1953, the complex began assembling dishwashers and dryers. Later that year, electric ranges and washing machines were added to the mix, while a refrigerator plant opened the following year. In 1958, after completion of a $40 million expansion, GE also began assembling air conditioners on the campus.
By 1961, Appliance Park employed more than 10,000 people and could produce 60,000 major appliances a week. At the end of that decade, the sprawling facility included a power plant, a fire department and an R&D center, in addition to assembly plants and warehouses connected by a network of conveyors, railroad tracks and roads. The complex was so big that it was even assigned its own zip code.
The dishwasher factory has a long track record of investing in the latest production tools, equipment, processes and technology. For instance, in the mid-1970s, GE engineers developed the appliance industry’s first molded thermoplastic dishwasher tub. Among other things, the PermaTuf design reduced the number of fabricated parts required.
The first robot at Appliance Park was installed in late 1979. It was used to remove uncoated dishwasher racks from a 600 F oven, dip them into a bed of polyvinyl powder, and place them onto a conveyor, which moved the racks to bake in another oven.
In the early 1980s, GE embarked on a $38 million initiative to automate the dishwasher assembly line. The project included robots, ultrasonic plastic welders, point-of-use stamping presses, inventory control systems, bar code scanners and other productivity-enhancing technologies.
The project was a great success. Thanks to automation, the line operated at prerecession levels with two-thirds the workforce. The changes improved manufacturing efficiency and quality so profoundly that sales of GE’s dishwashers skyrocketed and service calls were cut in half.
Encouraged by the success of the project, GE embarked on a $1 billion program to adapt the lessons learned on the dishwasher line to the rest of the company’s appliance assembly operations.
In the mid-1990s, those improvements were followed by the world’s first “smart” dishwasher, which featured auto-sensing gauges to detect soiled dishes.
General Electric’s appliance division was acquired by Haier Smart Home for $5.6 billion in 2016. Part of the deal was a long-term agreement to continue use of the GE name, including its famous monogram logo.
Since then, GE Appliances has reinvested more than $2 billion to upgrade its U.S. manufacturing operations, including its flagship operation at Appliance Park.
The 2024 Assembly Plant of the Year sits in the middle of the complex, which is laid out in a linear fashion. It is surrounded on one side by a plant dedicated to producing injection-molded plastic parts. A metal fabrication and paint facility is located on the other side of AP3.

Appliance Park is a huge complex that features five factories laid out in a linear fashion. Photo courtesy GE Appliances
Unique Products
All dishwashers perform the same basic function, and most machines appear similar from the outside. In fact, most share the same dimensions: countertop height and 24 inches wide.
But, inside, it’s a much different story. Unlike other major appliances, such as refrigerators and washing machines, wire racks are unique to dishwashers. The machines are equipped with either two or three racks that securely hold items during the washing and drying cycles.
Dishwashers also contain a variety of hydraulic components, such as pumps and rotating spray arms that move water around. In addition, dishwashers use unique types of heating and air flow elements. And, many controls are located on the top or front of doors.
The heart of a dishwasher is its tub, an inner box made out of either polypropylene plastic or stainless steel. The latter is much thinner and is typically used on high-end products.
Dishwashers today have become more complex than ever, because they contain a variety of electronic components. That creates some unique challenges for assemblers, such as making sure that printed circuit boards, sensors and other sensitive devices are protected from electrostatic discharge.
The 2024 Assembly Plant of the Year produces five brands of dishwashers: Hotpoint, GE, Profile, Café and Monogram. Machines are produced in a wide variety of styles to meet the unique needs of different consumers. In addition to stainless steel finishes, some dishwashers are available in up to nine colors. Retail prices typically range from $300 to more than $2,400, depending on brand and features.
Some finished goods are shipped directly to customers, ranging from major retailers to contractors, home builders and multifamily housing projects. Products not shipped directly to customers are sent to one of GE Appliances’ distribution centers located throughout the United States.
Hotpoint is GE Appliances’ value brand, while the GE brand is aimed at the mass market. Profile, Café and Monogram products are targeted at the mass-premium and ultra premium segments. Dishwashers in the latter categories feature optional attributes such as customizable accent handles and hardware, glass doors, designer colors and performance features like Dual Convection Ultra Dry.
“Every dishwasher we make performs extremely well at cleaning and drying dishes due to the multiple design features that we use,” says Vibbert. “Hotpoint is a tough unit. ‘Tougher than Life’s Everyday Challenges’ is our slogan on that brand. It gets it done, and at a great price.
“Our GE, Profile, Café and Monogram brands all come with additional features from Dry Boost technology, which gets hard-to-dry items like plastics three times drier than standard heated-dry dishwashers, to wash performance features like bottle jets,” explains Vibbert.
“Generally, as the features increase, part count does as well,” Vibbert point out. “The higher featured products typically have more labor associated with them. Stainless steel dishwasher lines also require more production processes.”
To keep up with demand, GE Appliances recently launched two new dishwasher products. An $80 million project on the plant’s highest volume assembly line last year produced a new tall tub model that drove transformational change by creating a new product architecture and platform.
Another initiative brought a second wave of transformation to AP3. This project included two new flexible assembly lines and new presses to produce five brands of steel tub dishwashers.
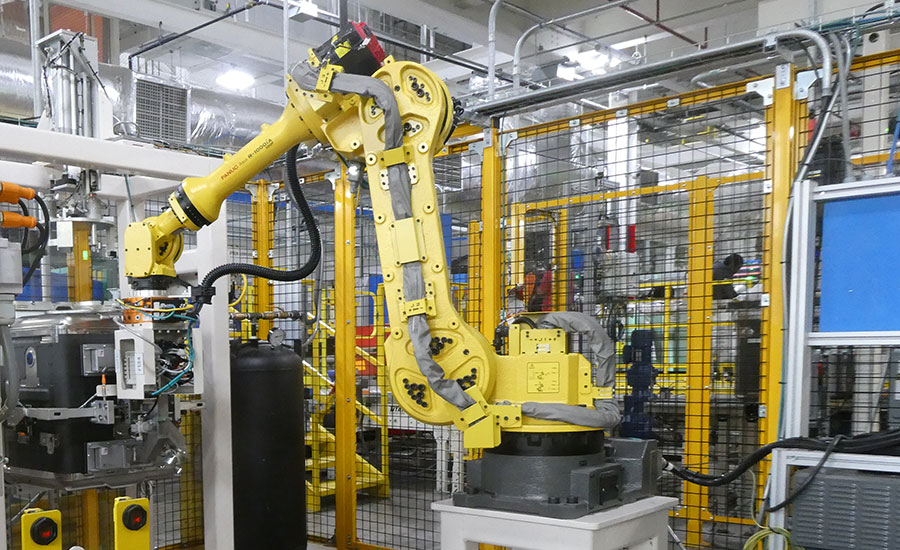
The 2024 Assembly Plant of the Year excels at using automation and robotics. Photo by Austin Weber
Productive Plant
The 2024 Assembly Plant of the Year is a vertically integrated facility. It produces many parts in-house to guarantee quality and meet delivery deadlines. For instance, the facility boasts a large plastic injection-molding operation and a metal fabrication department.
Production begins with rolls of coiled steel and bins of resin pellets. Major components, such as doors, racks, spray arms and tubs are made onsite. That strategy has decreased overall material and transportation costs, and enabled the plant to respond more quickly to changes in customer demand.
“We make the vast majority of components assembled in our dishwashers,” says Vibbert. “What we buy from outside vendors is centered on electrical components, but just about everything else is made in-house.
“Cost and quality make vertical integration a critical part of the plant’s success,” explains Vibbert. “By making components and subassemblies in-house, our inventory on hand is reduced, and we can control quality and be much more effective at making improvements.
“In addition, it’s much easier to change a part for productivity’s sake or quality’s sake,” claims Vibbert. “Without having a long supply chain, we can make changes instantly. For instance, a change can take effect in a day or two, as opposed to 12 weeks.”
AP3 runs three shifts per day, five days a week.
“We operate five separate assembly lines and they are quite flexible,” says Vibbert. “Multiple lines have the capability and capacity to run the products made on other lines. That is part of our strategy for both internal factory agility to meet changing demand, and from a design perspective to have a common architecture and bill of process that enables production processes and equipment to be standardized.”

The vertically integrated factory operates five assembly lines that produce dishwashers equipped with both plastic and steel tubs. Photo by Austin Weber
Visual communication, lean management, digital tools and data analytics play a key role in the plant, especially when it comes to improving ergonomics, quality and safety.
“Our assembly lines provide us with a mountain of data to tell us how well they’re running or, if we have issues, exactly where those issues are and how we can quickly solve them,” explains Vibbert. “That has enabled us to be more productive, boost quality and control costs.
“Many of the subcomponents of a dishwasher are attached via screws of various sizes and strengths,” Vibbert points out. “Having the certainty of the presence, torque and rotation of each of these fasteners is critical to the quality experience we expect for our customers.
“We use DC electric and pneumatic tools to ensure that our units are made correctly every single time,” says Vibbert. “And, we can look at the data from these joints to study the design, supplier quality, operational performance and even difficulty that operators may have to increase the opportunity for productivity in our process. We’re now using artificial intelligence technology to help us further.
“Using DC tools on our assembly lines and interlocking them to our production operations has dramatically improved our process quality,” claims Vibbert. “By ensuring that our fasteners are at an appropriate torque and angle, our risk of leaks for critical joints has dropped significantly.
“Additionally, the interlock feature of the 70 DC guns on our assembly lines ensures that operators perform work per the standardized work manuals and in the appropriate order of operation, if and when andons start to climb,” notes Vibbert.
GE Appliances’ manufacturing quality engineers recently harnessed the power of cloud data and AI technology, using Google Cloud to improve the efficiency of the plant’s DC electric tools by monitoring the yield of screwdriving operations to validate quality goals. As a part of the broader production leadership team that meets three times per day in an obeya room on the plant floor equipped with large boards, they review charts and graphs in minute detail. It enables them to monitor assembly line activity, improve productivity, address quality issues and implement continuous improvement initiatives.
“It’s one of many elements in our Brilliant Factory system that provides our front-line leaders with the ability to know what’s happening on the plant floor,” says Vibbert. “We can determine what’s happening on a particular line or track a piece of equipment that’s having an issue. It provides analytics about how our DC tools are performing, which enables engineers and floor-focused leaders to address potential quality issues.
“We rotate operators around workstations every two hours,” explains Vibbert. “As that occurs, we sometimes experience low torque or off-angle fastening parameters. By monitoring analytics, we can see if any abnormalities are occurring and correct them. And, it’s not always just a matter of operator error. Sometimes, there’s an issue with the tool, the screw or the part that we weren’t aware of.”

This end-of-line test loop was recently developed in-house. Photo by Austin Weber
All assembly lines in the plant are equipped with end-of-line test loops. One of the newest features is a home-grown test sequence and software that was developed in-house. It performs a full functional and mechanical check on 100 percent of production output, testing 40 dishwashers at a time, including electrical, hydraulic and leak testing.
Last year, the plant also invested in a new flexible assembly line. It’s unique, because the line is capable of building dishwashers equipped with either plastic or stainless steel tubs.
“Reducing the amount of complexity by streamlining our bill of process and investing in automation, we can differentiate at the latest point possible to meet demand,” says Vibbert. “In the last few years, we’ve learned that you sometimes don’t know where the market is moving.
“The new line enables us to be flexible and quickly move product around to address market opportunities,” claims Vibbert. “It gives us the ability to pivot and add either additional plastic volume or stainless steel volume. It requires a lot of intelligence from our automation and controls systems, which is where our investment in digital tools really pays off.”
Advanced Automation
GE Appliances’ dishwasher factory has invested heavily in automation to address ergonomic issues and improve material flow. For instance, the plant uses a fleet of autonomous guided vehicles to deliver parts line-side.
“We have launched and continue to trial multiple AGVs to assist in part flow through the shop,” says Vibbert. “Our dish racks move on continuous routes through the factory from their production areas to the intended assembly lines. Also, we are performing trials with an automatic trailer unload robot that reduces fork truck movement on and off trailers. These processes alone have reduced downtime and operational costs by 5 percent per year.
“One of our most recent building expansions was a 30,000-square-foot warehouse to receive and flow parts to our assembly lines,” Vibbert points out. “This space was kitted with a 12-bay receiving dock, a four-story shelving system and a supermarket, and blanketed in digital coverage.”
As parts are received, they are not only physically moved into the building, but they are also digitally moved in separate discrete inventory designations from truck to dock, dock to warehouse, warehouse to supermarket and supermarket to line side.
“We use a dynamic address system to optimize space within the warehouse and ensure our material movement systems operate at maximum efficiency,” explains Vibbert. “This digital system has improved our material accuracy by well over 7 percent, ensuring we can improve cash flow and turns in our production operation. There are currently more than 250 robots in use throughout our dishwasher manufacturing operations, including six-axis and SCARA machines. In fact, the plant now has up to three times as many robots as it had just five years ago.

New dishwasher production lines were designed with operator input. Photo courtesy GE Appliances
“We use a lot of robots for large part maneuvering, such as changing the orientation of steel tubs 180 degrees so that operators can work inside, above or behind,” says Vibbert. “Robots help address ergonomic issues related to parts that are heavy or have sharp edges.”
One of the plant’s newest robotic applications is a wire rack subassembly line that supports the highest volume assembly line. It automatically cuts, fabricates and coats wire-formed dish racks.
Multiple robots are used in the upper and lower cells to move strands of wire coil from one location to another during a precise process that welds pieces together to form a dish rack. Each rack is then coated with a protective layer of polyvinyl chloride plastic.
“The wire rack assembly line uses a variety of robotic welding cell that enabled us to consolidate approximately 10,000 square feet of floor space into a footprint of less than 2,000 square feet,” notes Vibbert. “It improves productivity and increases first-pass yield. We’ve also instituted multiple vision systems that improve the wire forming and welding process.”
Another recent investment is a stainless steel tub fabrication line that has been in operation for two years. The fully automated line enabled a significant reduction in labor content and part consolidation.
“The automated line eliminates a lot of ergonomic and quality risks while delivering a tremendous product.”
– Tim Vibbert
The robotic cell uses clinching and spot welding, working in conjunction with a stamping press, to make a complete tub. It also installs sealant and attaches clips, gaskets and other components.
“What comes out at the end of the line is a finished tub that we can immediately leak test and inspect, then send straight to the dishwasher assembly line,” explains Vibbert. “The automated line eliminates a lot of ergonomic and quality risks while delivering a tremendous product.”
The 2024 Assembly Plant of the Year also recently implemented a robotic cell that installs sumps into the bottom of dishwasher tubs. In the past, this process was done manually.
Operators would pick up a sump assembly, which weighs about 5 pounds, then reach under the tub, install the device blindly and then flip a couple of latches to securely hold it in place. To reduce the risk of leaks, assemblers had to ensure that the sump was level and seated correctly.
“Doing that up to 1,600 times per shift presented several ergonomics risks, such as awkward reaches, in addition to potential quality risks,” says Vibbert. “A six-axis robot now ensures that sumps are installed correctly every time.”
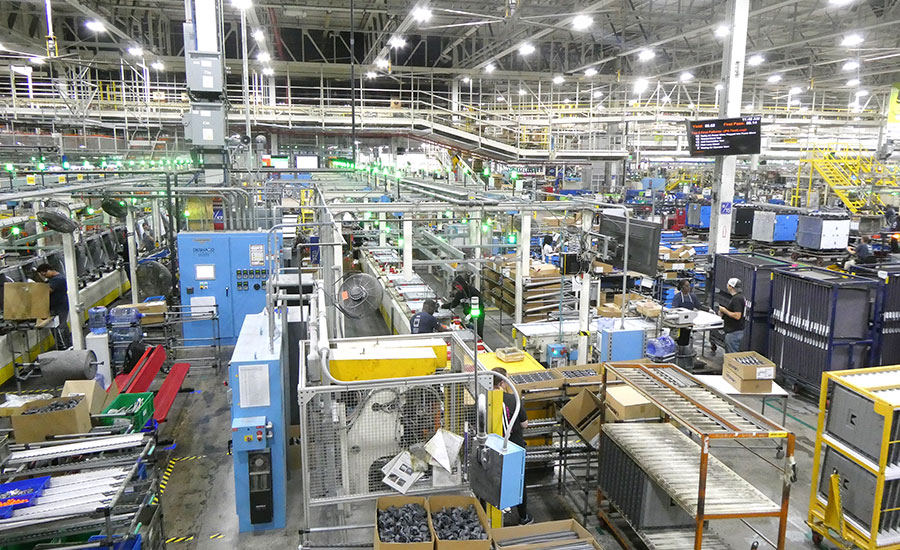
Every inch of the factory has been improved and renovated in the last eight years. Photo by Austin Weber
Continuous Improvement
In addition to automation, people also play a valuable role in the plant’s daily operations. Assemblers are asked to generate ideas related to production methods, new equipment, new process development, kaizen, material presentation improvements and process elimination. This keeps employees focused on high-value tasks.
“Last year alone, using operator-driven kaizen, we delivered nearly a 10 percent improvement in process, and we increased our output by 3 percent of assembly yield,” claims Vibbert.
“In AP3, we take the lean concept of visual management seriously to include not only production metric visibility to the shop floor, but also real-time tracking of operational efficiency of our assembly lines,” says Vibbert. “Our Brilliant Factory production system collects, aggregates and displays equipment and station performance by operations area.
“This enables our manufacturing leaders to effectively investigate their lost-starts through pareto analysis down to the second,” explains Vibbert. “This improvement in visibility, which we really see as an effort to ‘democratize data’ has enabled our factory to increase assembly output by more than three points in the last two years, and more than six points in the last four years.”
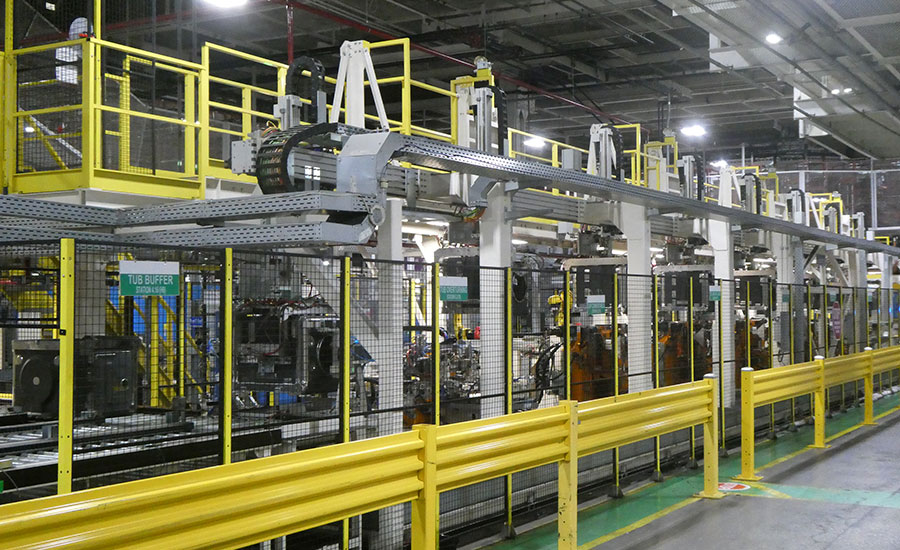
This stainless steel tub fabrication line is fully automated. Photo by Austin Weber
One recent success story revolved around the launch of the GE Profile UltraFresh System dishwasher with Microban antimicrobial technology, which is now being added to other models produced at the plant. The built-in system is designed to provide a 99 percent cleaner dishwasher.
“Through the latest new product introduction program, we saw a 47-part count reduction, usage of 23 common parts and 17 assembly methods improved as a result of our architecture efforts,” says Vibbert. “This commonality and reduction in complexity enables a stronger supply chain, more factory agility to maintain flexibility to meet market demand, and operational familiarity so operators approach the same process conceptually no matter the assembly line they work on.”
Several recent projects consolidated parts and reduced complexity using Design for Manufacture and Assembly principles. The applications involved the use of snap-fits and twist locks to reduce insertion forces and screw counts.
“We used to ask operators to take six parts in one hand and press them from the inside to the outside of the rack mount unit inside the tub, then insert and fasten screws to hold it together,” explains Vibbert. “Our design engineers worked tirelessly to improve the process, and in doing so, they changed that into just two snap-fit parts—one on the inside and one on the outside.
“Another project changed the geometry of a previously fastened plastic part with a twist lock,” adds Vibbert. “The new part easily snaps into place. It resulted in a significant part count reduction, as well as improved ease of installation. It was a great ergonomic win for the operators.”
A major focus throughout Appliance Park is improving the work experience for employees. The new dishwasher manufacturing lines at AP3 were designed with experienced production employee input and virtual reality technology to ensure the jobs and workstations were ergonomically optimized prior to construction.
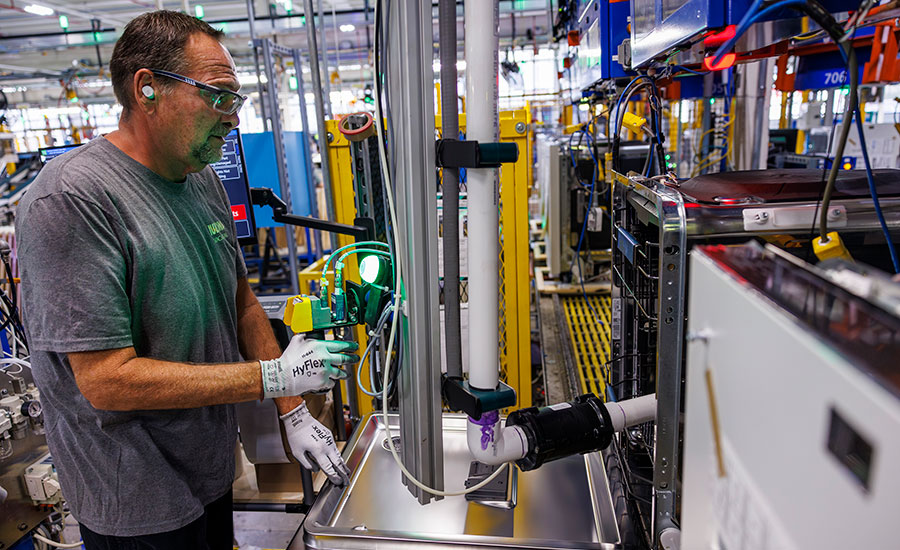
Recent initiatives have reduced product complexity and improved ergonomics for operators. Photo courtesy GE Appliances
Nine filtration and cooling towers, plus a new employee cafeteria, have also been incorporated into the plant footprint to improve the employee experience.
“Operators are at the heart of our plant,” claims Vibbert. “One very successful and recent adaptation was to staff hourly team leaders on new product programs at the start of the initiative. Their input influenced product and component designs, manufacturing process development, material flow efficiency and standardized work creation.
“Their inclusion also accelerated the program timelines, whereas they performed assembly process confirmation in stride with product design confirmation,” says Vibbert. “Finally, this process helped to accelerate line launch and assembly output ramp expectations.
”Like all manufacturers today, finding and retaining employees has been a challenge for GE Appliances. The company has redoubled efforts to focus on the employee experience, offering ride credits for employees having transportation issues and an on-site primary care clinic. Other recent initiatives included renovating cafeterias and restrooms, and offering flexible schedules to attract hourly employees. GE Appliances also launched the Every Voice program, an initiative aimed at providing career paths for non-native English speakers.
The company recently started a program that pairs new hires with experienced manufacturing employees.
“Ambassadors work with our recruiting and new hire orientation team to serve as a contact point during the first few days that a person is on the job,” explains Vibbert. “They check up on new hires to make sure that they have what they need to be successful and to be a strong contributor to the GE Appliances team. Every new hire is assigned an ambassador.”
About the Award
The Assembly Plant of the Year award was initiated in 2004 to showcase world-class production facilities in America, and the people, products and processes that make them successful. There is no entry fee. All manufacturers that assemble products in the United States are invited to nominate their plants. The winning plant receives a crystal award and a commemorative banner.
The Assembly Plant of the Year award is sponsored by ASSEMBLY Magazine. The goal of the award is to identify a state-of-the-art facility that has applied world-class processes to reduce production costs, increase productivity, shorten time to market or improve product quality.
All nominees were evaluated by ASSEMBLY’s editorial staff, based on criteria such as:
- Have assembly processes been improved through the use of new technology?
- Has the plant improved its performance by making more effective use of existing technology?
- Has the plant taken steps to reduce production costs?
- Have new or improved assembly processes resulted in increased productivity?
- Has the plant used assembly improvements to reduce time to market?
- Has the plant boosted bottom-line profits and competitive advantage?
- Did operators play a role in the successful implementation of new assembly strategies?
- Has a product been effectively designed for efficient assembly?
- Has the plant attempted to protect the environment and conserve natural resources?
As winner of the 21st annual Assembly Plant of the Year competition, GE Appliances received an engraved crystal award and a commemorative banner.
Previous recipients of the Assembly Plant of the Year award were Taylor Guitars (El Cajon, CA); Brose Tuscaloosa Inc. (Vance, AL); GKN Automotive (Newton, NC); Murakami Manufacturing USA Inc. (Campbellsville, KY); GE Appliances (Decatur, AL); Ford Motor Co. (Sterling Heights, MI); AGCO Corp., (Jackson, MN); Bosch Rexroth Corp. (Fountain Inn, SC); Polaris Industries Inc. (Spirit Lake, IA); STIHL Inc. (Virginia Beach, VA); Northrop Grumman Corp. (Palmdale, CA); Ford Motor Co. (Wayne, MI); Philips Respironics (New Kensington, PA); Eaton Corp. (Lincoln, IL); Batesville Casket Co. (Manchester, TN); IBM Corp. (Poughkeepsie, NY); Schneider Electric/Square D (Lexington, KY); Lear Corp. (Montgomery, AL); Xerox Corp. (Webster, NY); and Kenworth Truck Co. (Renton, WA).
A nomination form for the 2025 Assembly Plant of the Year award will be available on ASSEMBLY's website in early January.