Humanoid Robots Push the Bounds of Collaborative Manufacturing
July 3, 2024
Humanoid Robots Push the Bounds of Collaborative Manufacturing
July 3, 2024This humanoid robot at an EV factory in China performs quality checks on door locks, headlights and seat belts.
Photo courtesy UBtech Robotics
Humanoid robots were once the stuff of science fiction. Now, after years of development, human-sized machines equipped with two arms and two legs are slowly making their way into assembly plants and warehouses. They feature state-of-the-art actuators and sensing technology powered by artificial intelligence.
Faced with severe labor shortages, automotive manufacturers and suppliers have expressed a keen interest in humanoids. In fact, legacy OEMs such as BMW and Mercedes-Benz are testing the technology in their factories.
Some automakers, such as Hyundai and Tesla, are going a step further by developing their own general-purpose robots. Tier One suppliers such as Magna International Inc. are also jumping on the bandwagon.
The sudden interest in humanoids appears to be more than just a fad. Indeed, Goldman Sachs recently issued a report on the topic, claiming that the cost of the machines has decreased by 40 percent over the past year. That trend is expected to continue in the future and help spur rapid growth, resulting in a $38 billion market by 2035.
Gartner Inc. predicts that by 2027, 10 percent of new intralogistics smart robots sold will be next-generation humanoids.
Those bold predictions have fueled the hype cycle, leading to both wild projections and rampant fears. However, the reality is that humanoids will play a niche role in automation for the foreseeable future.
While humanoids may be a long-term solution to a variety of manufacturing woes, they are not going to replace traditional cobots, six-axis robots and other machines in factories anytime soon.

Neura Robotics’ 4NE1 humanoid was recently displayed at the Automate show in Chicago. Photo by Austin Weber
The Role of Humanoid Robots
Interest in humanoids has hit a new high during the past 12 months, due to a slew of provocative announcements from start-up companies such as Agility Robotics, Apptronik, Boston Dynamics, Figure AI, Neura Robotics and Sanctuary AI.
Looking for a reprint of this article?
From high-res PDFs to custom plaques, order your copy today!
But, humanoids have actually been capturing widespread attention for decades. For instance, almost a century ago engineers at Westinghouse Electric Co. developed a 7-foot tall machine dubbed “Elektro the Moto-Man” that became a star attraction at the 1939 New York World’s Fair.
Two decades ago, Honda Motor Co.’s ASIMO made headlines with human-like feats of its own. The humanoid even graced the cover of ASSEMBLY in July 2005. That same year, the Robonaut machine created by engineers at General Motors and NASA made a special appearance at the Assembly Technology Expo in Rosemont, IL.
Humanoids have come a long way since then, due to a variety of technological advancements.
“We’re seeing robots of all forms become more commercially available for a few reasons: An increase in safety, an increase in demand and an increase in feasibility,” says Brian Zakrajsek, specialist leader for smart manufacturing at Deloitte Consulting LLP.
“Automotive and global logistics companies are experimenting with humanoid forms, believing [they] will be the most adaptable to the human world,” explains Zakrajsek. “As humanoid robots and other technologies become safer to use, they become more appealing to organizations looking to transform and evolve.
“In the past five years, we have seen big steps made in the capabilities, power and scalability of humanoid technology,” notes Zakrajsek. “General communication with robots has been simplified through the development of generalized interfaces like chatbots and low- or no-code programming. The ability to move AI and advanced processing right to the edge, in the chip, enables very low latency adaptable workflows.

Recent advancements in artificial intelligence are making humanoids more fact than fiction. Photo courtesy Boston Dynamics Inc.
“Materials, especially in grippers, can more closely model the human hand, allowing advanced articulation and [touch] capability,” Zakrajsek points out. “Hydraulics win out for overall strength, but electric-powered servos are more feasible and responsive in the humanoid form factor.
“Today, there is multi-layer application of AI within robots, which includes synthetic data generation, product simulation, vision identification, mechanical and end effector design,” says Zakrajsek. “In addition, increased axes in robot hardware enable more fine-tuned, human-like movements.”
“Until recently, there were no successful examples of humanoid robots that used arms and legs to navigate, pick up and manipulate items,” adds Dwight Klappich, vice president of research at Gartner. “What makes next-generation [machines] different is their ability to eventually obtain the level of adaptability that humans have, which will allow robots to be used and repurposed for many different activities without programming.
“Next-generation humanoid robots will compete with the current cost of labor for similar functions, and will provide higher availability and reliability than the human workforce,” predicts Klappich. “These robots can flexibly support the needs of a business by dynamically moving from process to process and taking on new activities without special programming.
“These developments are very exciting to [companies that] have struggled with chronic labor challenges,” says Klappich.
Recent advancements in AI have helped make humanoids more fact than fiction.
“AI plays a massive role in humanoid robot technology,” notes Zakrajsek. “Not only is it the tool that enables robots to fulfill tasks, but it also can be deployed to determine the most valuable areas of the manufacturing process that robots can support. We are seeing a mixture of traditional AI and, more recently, generative AI implemented into robots to increase their use cases on factory floors.
“In the future, we will see companies use robotics and AI to automate the ‘long tail’ of manufacturing,” predicts Zakrajsek. “We will see manufacturers layer technologies to increase outsized gain. This comes from simplified interfaces and orchestrated processes.
“This is not about talking to a robot through a chatbot,” says Zakrajsek. “This is about how we can use a voice-to-text interface as the first step in a structured workflow to accomplish a complex task in the most optimized way. The adoption is honestly very far out, but the value is high.
“If we believe humanoids can provide a broad set of generalized applications traditionally served by a human (or supported by a human), we will have a higher expectation for AI (specifically deep learning) to support these use cases for collaboration,” claims Zakrajsek. “I believe we will see increased investment in enabling infrastructure and avoiding ‘instantaneous tech debt’ from rigid system integration.”
Recent Breakthroughs in Humanoid Robots
Until recently, the cost of building a humanoid was prohibitive. It typically required anywhere from $750,000 to $1 million. In that same time period, however, the typical cost of industrial robots was less than $100,000.
“Within the past decade, there have been several breakthroughs in robotic technology, such as collaborative robot arms, open-source programming and mobile robots,” says Melonee Wise, chief technology officer at Agility Robotics Inc. “The development of autonomous mobile robots (AMRs) a decade ago started to drive down the cost of some of the key components of humanoids. For instance, when AMRs took off, it reduced the cost of actuators and sensors.
“Now, the cost of building a humanoid robot is closer to $100,000, which is 10 times less than it was in the past,” claims Wise. “That’s driven a belief that the technology is ready for commercialization.”
Unlike most other humanoid companies, Agility actually has machines currently deployed with customers. Its Digit robot is already in use at an Amazon Inc. warehouse near Seattle picking up and moving bins that weigh up to 35 pounds and placing them on conveyors. Agility is also in the process of deploying the five-foot, nine-inch robot in several automotive factories.
Digit’s “backward” legs enable it to maneuver in tight spaces and get closer to shelves, conveyors and other infrastructure. The unique design also allows the machine to reach deeper and maintain an operational pick range from floor level up to six feet.
“We are finally reaching a point where most of the key ingredients needed for a humanoid robot are cost-effective, energy-efficient, lightweight and small enough to be integrated into a package that is practical to sell as a commercial product,” says Brendan Englot, Ph.D., an IEEE senior member and associate professor of mechanical engineering at the Stevens Institute of Technology.
“This includes electromechanical arms and legs, batteries, onboard computing, and perception and motion sensors,” explains Englot, who serves as interim director of the Stevens Institute for Artificial Intelligence. “Today’s humanoids are lighter, smaller, untethered and increasingly all-electric. They can also be equipped with onboard sensors and computing capabilities that are much more compact and energy efficient than was possible 10 to 15 years ago.

BMW plans to use humanoid robots like this at its flagship assembly plant in Spartanburg, SC. Photo courtesy FigureAI Inc.
“Some of the key advances have been in the perceptual capabilities of humanoid robots, such as how they see and interpret the world around them, and use that data to navigate and make decisions,” Englot points out. “[Plus, we now have the] ability to stabilize and control their motion using data-driven approaches, such as reinforcement learning, which can leverage modern computing capabilities to permit robots to learn through trial and error.”
“The timing is a confluence of technological maturity, economic demand and societal readiness,” adds David Reger, CEO of Neura Robotics GmbH, which has developed a humanoid robot called 4NE1.
The machine uses AI technology that enables it to understand and respond to human commands naturally and effectively. With an advanced sensor suite, it performs tasks with high precision using state-of-the-art sensors for vision, touch and force.
“Designed to complement human workers, 4NE-1 enhances collaboration and productivity rather than replacing human roles,” claims Reger.
Neura was the only robotics company displaying a humanoid at the recent Automate show in Chicago. The static machine did not operate, but it provided a popular photo op for attendees.
“For years, humanoid robots were confined to laboratories due to technological and cost limitations,” explains Reger. “However, recent advances in AI, sensors and materials have made these robots more reliable, versatile and cost-effective.
“The economic pressures of labor shortages, and the need for efficiency in factories and warehouses, have also driven demand for such solutions,” says Reger. “In addition, social acceptance of robots has grown, making it an opportune time to introduce humanoids into commercial environments.
“Today’s humanoid robots are exponentially more advanced than their predecessors of a decade or more ago,” Reger points out. “They benefit from cutting-edge AI that enables more intuitive interaction and problem solving. The integration of advanced sensors provides better situational awareness and task precision.
“Recent advances in humanoid technology have been very exciting,” notes Reger. “Improvements in AI and machine learning now allow robots to make smarter decisions and adapt to different environments more effectively. Improved force sensors allow them to perform delicate tasks with precision, while advanced vision sensors improve their ability to recognize objects and navigate their surroundings.
“And, new high-efficiency motors and actuators give them smoother, more precise movements, reducing wear and tear,” says Reger. “Together, these advances make humanoid robots more functional, efficient and practical for a wide range of applications.”
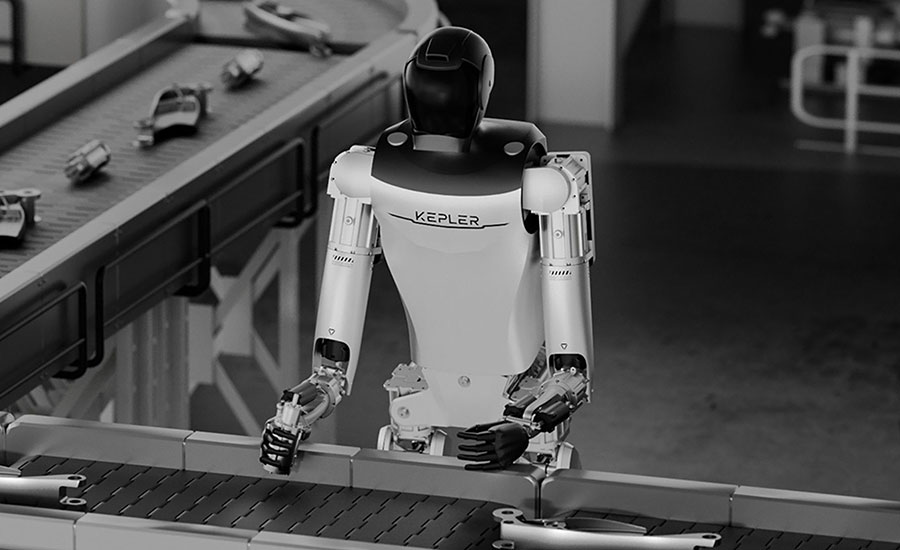
This humanoid features an intelligent and dexterous hand with 12 degrees of freedom. Its 187-pound body boasts up to 40 degrees of freedom. Photo courtesy Kepler Exploration Robot Co.
Humanoids vs. Traditional Robots
Manufacturers around the world have already invested billions of dollars in traditional industrial robots. So, despite what some folks think, they’re not about to scrap all their Cartesian, SCARA and six-axis machines overnight and suddenly invest in humanoids. Indeed, the adoption curve will be much more gradual.
Neura Robotics has a unique perspective on the issue, because unlike many other humanoid companies, it also makes traditional industrial robots such as AMRs and six-axis cobots.
“Humanoids offer a unique blend of versatility and human-like interaction that other robot types may lack,” says Reger. “While AMRs excel at navigation and transport tasks, humanoids can perform a wider range of functions that require complex manipulation and interaction in human-centered environments.
“Cobots are designed to work safely alongside humans, and humanoids can also fulfill this role, but with the added benefit of being able to perform tasks independently when required,” Reger points out. “Humanoids bring an additional layer of adaptability and intuitive operation due to their human-like form and capabilities.”
“The value proposition of humanoids is all about versatility,” adds Jeff Cardenas, CEO of Apptronik Inc. The company’s Apollo machine can lift 55-pound payloads and work alongside humans in environments designed for people.
“Mobile cobots will increasingly compete against humanoids,” says Cardenas, who spoke at the recent Automate show. “However, humanoids will not take the place of every robot. I think all different types of robots will work together.
“Today, we have thousands of robots that can each do one thing,” explains Cardenas. “But, what if we had one robot that could do thousands of things? Humanoids are the next major robotic form factor.”
According to Cardenas, the world is built for humans. He believes the holy grail for robotics is slotting a smart machine into the work environment to perform tasks the same way that humans already do.
“What has constrained automation up until this point has been task switching and retrofitability,” says Cardenas. “To change the unit economics of these systems, multipurpose functionality becomes really important. We need a robot that can do more than one thing and can be more utilized over a 24-hour period.

Engineers at Tesla are developing a general-purpose robot called Optimus. Photo courtesy Tesla Inc.
“The same thing that happened in computing is going to happen in robotics,” predicts Cardenas. “[In the 1980s, there was a] shift from mainframes to personal computers. Robots are like mainframes; we’re now entering the era of general-purpose platforms that are much more versatile and scaled to much greater degrees than what robotics did in the past.”
“I think there’s always going to be purpose-built robots,” adds Aaron Sanders, chief technology officer at Boston Dynamics Inc. The company makes a two-legged machine called Atlas, in addition to its popular Spot robodog. “Humanoids make more sense for general-purpose applications. They’ll be valuable in applications where fixed automation can’t go.
“I don’t think there’s going to be a lot of value in humanoids simply replacing what fixed automation does,” says Sanders. “We need to be careful that we don’t mix things that humanoids could do with things that they should do. We’ll need [applications] that rely on complexity and dexterity to see the full benefits of the humanoid form factor.”
“We’re not going to dismantle all of the purpose-built automation and insert humanoids,” notes Agility Robotics’ Wise. “In many cases, they’ll be used as flexible connectors between pieces of automation that were never built to talk to each other.
“A humanoid is a mobile manipulator that has legs,” explains Wise. “However, it offers more benefits than an AMR, which has some limitations. For instance, there’s a limit in terms of how far away from its center of gravity it can reach and balance things. Humanoid robots equipped with two arms and legs that are dynamically stable open up new applications.
“Humanoid [offer a type of] flexible automation technology that doesn’t tie you to large capital equipment long-term,” claims Wise. “They allow manufacturers to utilize the resource in many different capacities at different times throughout the workday. There’s a lot of flexibility and capability that comes with these machines.”
Despite several promising pilot projects, many experts believe that widescale deployment of humanoids in assembly plants is still three to five years away.
“Labor shortage issues have spurred interest in humanoid technology,” says Joe Liu, managing director and global lead for advanced automation and robotics practice at Accenture, which recently invested in Sanctuary AI, a Canadian start-up that is developing a general-purpose human-like robot called Phoenix. “The goal is to automate the last 20 percent to 30 percent of tasks that have been impossible to automate with traditional robots.”
Instead of competing against traditional types of robots, Liu envisions humanoids being used in factories along with AMRs and cobots. “There are still a lot of use cases that we cannot automate with traditional robots,” he point out. “Humanoids are part of the evolutionary process that will enable us to apply robotic technology to complement, collaborate and interact with humans.”
Balancing Automation Needs
Benchmark Electronics Inc. is a contract manufacturer that specializes in low-volume, high-mix complex assemblies. “In many cases, designing an automated and dedicated solution for these types of [products] is not economical, because the lower volumes cannot justify the investment,” says Jan Janick, senior vice president and chief technology officer at Benchmark.
“Humanoid robots with AI…can be trained to build assembly A in the morning and assembly B and C in the afternoon, then a completely different [product] tomorrow,” explains Janick. “In this case, the investment can be shared and the robot can be fully utilized across multiple manufacturing programs.
“Robotics and automation have been used in factories for years,” notes Janick. “They are typically optimized and deployed for a single task. They offer flexibility in tasks provided, but are typically optimized to do a single task and that task is defined to reduce the variables for the robotic automation.
“For example, if you have a robotic arm designed to pack boxes, when it runs out of cardboard it may electronically request more,” says Janick. “With a humanoid, you would expect the robot to request more cardboard, but it would also have the ability to go get the additional cardboard.”
According to Janick, AI is the technology that will make humanoid robots more commercially viable than alternative forms of automation. “[It] will allow humanoid robots to not only learn, but to provide a broader range of capabilities than a single-use automation design,” he points out.
“However, humanoid won’t replace the automated solutions available today,” claims Janick. “They will open up a broader set of applications that can take advantage of mobility, dexterity and AI intelligence.”
Gartner’s Klappich believes the immobile, inflexible and programmed single activity architecture of traditional industrial robots is too limiting for a majority of mobile and varied work tasks increasingly required in many factories. That’s why they’re primarily useful for addressing repeatable tasks with minimal variance from activity to activity or for moving things around from one location to another.
“Moving around and picking up individual items of varying sizes, shapes and orientations is difficult for robots, but easy for humans,” says Klappich. “As a result, humanoid robots will evolve during the next several years to address the limitations of previous generations of automation. [They] will provide the necessary cost savings, flexibility, adaptability and scalability that will generate large-scale investments from a range of different organizations.
“The potential for humanoid robots is clearly alluring, but it would be a mistake for…operations with high-volume, predictable and consistent processes to delay investments in more widely available smart robots today,” warns Klappich. “These organizations should consider some of the current generations of robots to enhance or supplement their human workforce.”
Before pursuing humanoid robots, Klappich recommends that companies map their functional processes to determine which, if any, can be addressed with traditional robots and which will benefit most from human-centered design.
“To do this, [engineers] should identify those processes that need high degrees of flexibility and adaptability, and focus on learning how your human workforce performs these tasks to understand what capabilities a humanoid robot will need to support,” says Klappich. “Because next-generation humanoids are a nascent technology, companies must develop a structured methodology for conducting effective proofs of concept.”
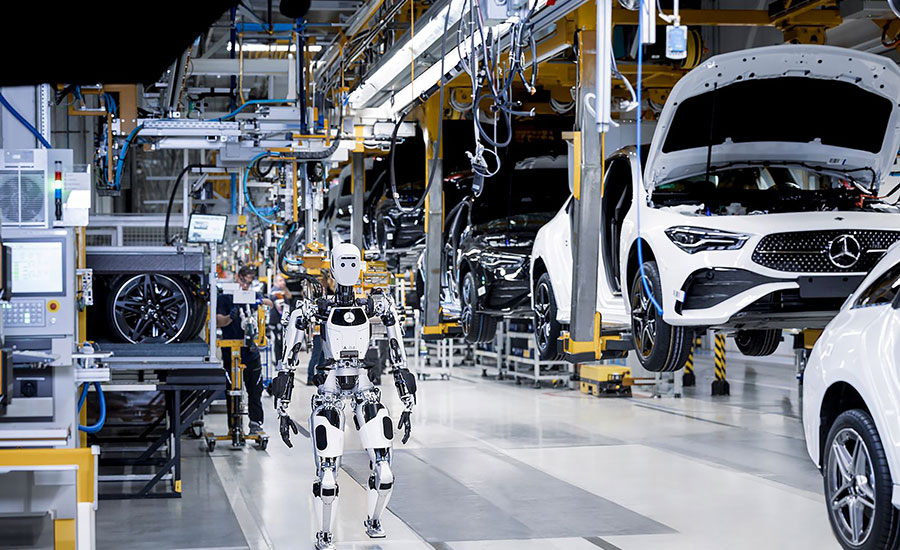
Automotive manufacturers and suppliers have expressed a keen interest in humanoids. Photo courtesy Apptronik Inc.