Swiss Engineers Develop Electric Airplanes

The goal of the H2 project is to equip a Swiss Light Wing AC4 with a fuel cell system that will allow a flight duration of more than two hours and a range of more than 250 kilometers.
Photo courtesy Kistler Instrument Group
Decarbonization presents a huge technical challenge for the aviation industry, especially for large aircraft and long-haul flights. On an average day, more than 100,000 commercial flights take off worldwide, making air traffic responsible for 2.5 percent of global CO2 emissions caused by people.
Engineers are addressing the problem in several ways. Besides developing sustainable aviation fuels and alternative fuels for turbines, such as hydrogen or liquid methane, work is under way on electric drives powered by batteries or hydrogen fuel cells. But, with longer flight durations and larger passenger capacities, it is becoming increasingly difficult to find adequate replacements for the high energy density of kerosene and aviation gasoline.
However, Cellsius, a Swiss team of young engineers, is providing impressive proof that decarbonization is already possible for small aircraft and short-haul flights. Founded in 2022 to focus on sustainable aviation, Cellsius offers college seniors the opportunity to test and expand their knowledge and skills on real aircraft. Cellsius is headed by a six-member executive board, with advisory support from professors at the Swiss Federal Institute of Technology in Zurich. All the association’s activities are financed and supported by various sponsors, including Kistler.

The Cellsius e-Sling is the world’s first four-seater electric airplane developed by students. Photo courtesy Kistler Instrument Group
Cellsius is based at an airfield in nearby Dübendorf, Switzerland. This airfield, now part of the Swiss Innovation Park, is gradually being expanded to create space for laboratories, workshops, offices and classrooms.
Cellsius’ first project, named e-Sling, was to equip a four-seater, low-wing aircraft with an electric propulsion system. After two years of development work, the all-electric e-Sling took off from Dübendorf for its maiden flight on Sept. 19, 2022—a huge success that was followed by an intensive flight testing phase.
At an early stage of the project, a torque sensor from Kistler was obtained to assist with designing the motor and developing the power electronics. The sensor was an integral element of the test stand for the motor.
Torque Measurements
Although the e-Sling was successful, the plane offered limited range and flight duration. So, Cellsius immediately embarked on another initiative, the H2 project, to develop an aircraft powered by hydrogen fuel cells. The objective is to equip a Swiss Light Wing AC4 with a fuel cell system that will allow a flight duration of more than two hours and a range of more than 250 kilometers.
In the new project, Frederic Huwyler is responsible for the electric motor in the fuel cell power train. Project sponsor e+a Elektromaschinen und Antriebe donated the motor for the project. Before the motor could be integrated into the aircraft, it was run on a test stand to optimize the load spectra and validate torque control.
“The 4520A torque sensor from Kistler really helped us to make sure that the torque present on the front of the propeller also corresponds to the torque applied to the rear,” says Huwyler. “The airplane has a variable-pitch propeller that requires appropriate control.”
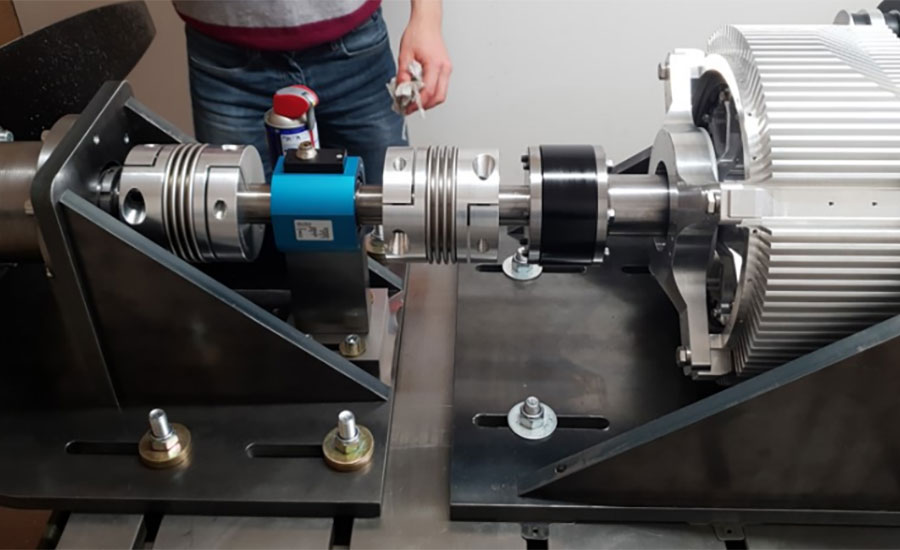
A torque sensor from Kistler—the blue device in the photo—was instrumental in developing the electric motors for Cellsius’ airplanes. Photo courtesy Kistler Instrument Group
The sensor operates on the strain gauge principle. It provides excellent dynamics with contact-free signal transmission (analog output signal: 0 to 10 VDC) at up to 1,000 newton-meters and speeds of up to 10,000 rpm.
Huwyler adds that the plane’s propeller requires a maximum torque of 400 newton-meters. “In the cruise phase, this is around 340 newton-meters at about 2,300 rpm,” he says. “That’s why our predecessors opted for a sensor with a measuring range of up to 500 newton-meters.”
Michael Haslinger is a member of the power electronics team in the H2 project. His focus is on the inverter and DC-DC converter systems that control energy transmission from the batteries to the power train. He, too, was favorably impressed by the torque sensor from Kistler.
“The excellent documentation makes it easy to set up and program, and it’s very reliable during handling and use,” Haslinger notes.
Thanks to the sensor, he and his team were able to verify the inverter control. “It also has practical advantages, such as integrated speed measurement and simple readout of the values. What’s more, we didn’t have any electromagnetic interference problems with the 4520A, which was not the case with certain other sensors,” he says.
Kistler technology is also playing a key role in developing the fuel cell system.
“A power train with a fuel cell is a complex system that requires a large number of individual components. We have developed many of them ourselves,” says Cedric Mägli, the engineer working on the fuel cell system.
The two hydrogen tanks are located under the wings of the AC4; then there is the fuel cell system, which includes three circuits for the air and hydrogen supply, as well as the cooling, buffer batteries, power electronics and, of course, the electric motor.
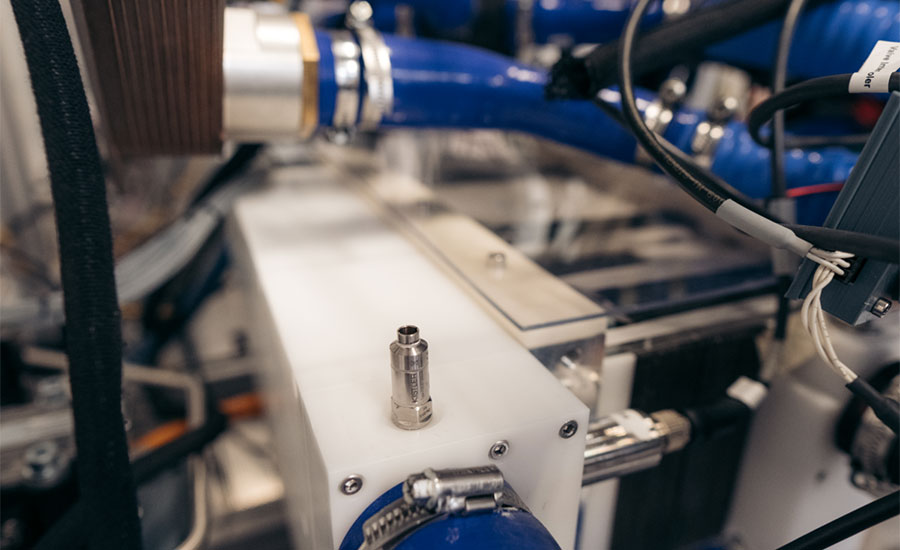
Pressure and temperature sensors from Kistler are installed in the first prototype of the Cellsius fuel cell system. Photo courtesy Kistler Instrument Group
All of these components add to the aircraft’s weight. The temperature, pressure and humidity of the media also need constant monitoring, and that requires additional measurement technology.
“That’s why we were keen to make the sensor technology as simple as possible, and accommodate it in one connection block with no additional fixtures. The Kistler sensor fits excellently into this concept,” says Mägli.
The 4080BT combined pressure and temperature transmitter is a miniature piezoresistive sensor with a diameter of 12.5 millimeters and a weight of less than 12 grams. The built-in PT1000 probe measures both pressure (up to 20 bar) and temperature (up to 150 C).
“Thanks to the very compact 4080BT, we were able to reduce the number and weight of the sensors we needed,” says Mägli. “On top of that, this sensor easily meets the requirements for the temperature and pressure ranges, and ensures the accuracy that is essential for the air supply.”
The emission-free AC4 is set to take off in the near future, although the exact date of its maiden flight is still “up in the air.”
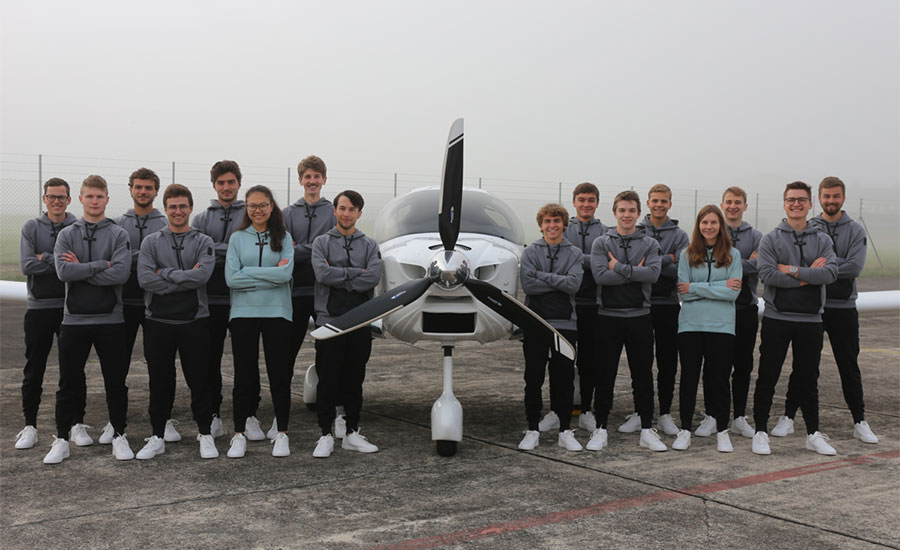
Cellsius, a Swiss team of young engineers, is providing impressive proof that decarbonization is already possible for small aircraft and short-haul flights. Photo courtesy Kistler Instrument Group
As the project proceeds, the students are acquiring valuable knowledge about handling alternative power trains. And, with their proofs of concept, they are also demonstrating what is already possible today.
Martin Stierli, business development manager for aviation at Kistler, has visited the Cellsius site on many occasions.
“As an innovative measurement technology provider, we’re delighted to support young engineers with their research projects—especially when the aim is to improve sustainability in aviation,” he says. “There are still quite a few measurement technology challenges to be overcome in the course of the H2 project, so we’re very happy to remain in close contact with the Cellsius team. Whether it’s thrust measurements on the propeller, tensile tests on the wing, or a wide variety of vibration measurements, we’re standing by to help overcome all these challenges, and we’re able to find solutions thanks to our diverse portfolio.”
For more information on sensors, visit www.kistler.com.
ASSEMBLY ONLINE
For more information on sensors for force, torque, pressure and other variables, read these articles:
Get Objective for Vehicle Dynamics Testing
Miniature Force Sensors Aid in Testing Touchscreens and Consumer Electronics
Servo Presses Improve Assembly of Diesel Engines
Looking for a reprint of this article?
From high-res PDFs to custom plaques, order your copy today!