Linear vs. Torsional Ultrasonic Welding
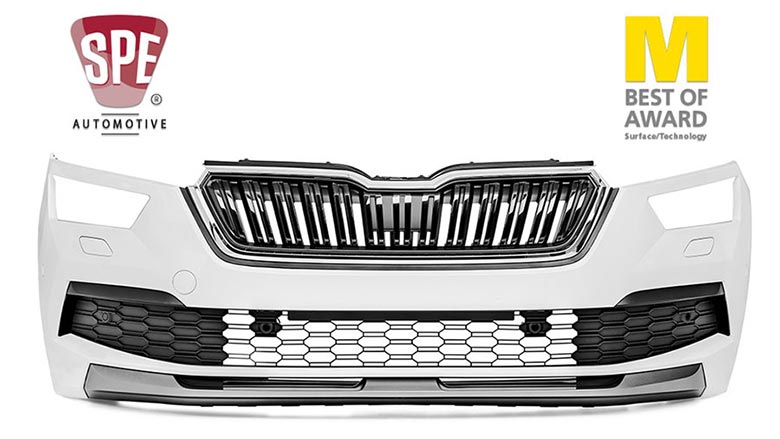
Torsional welding won’t mar Class A surfaces.
Photo courtesy Telsonic Ultrasonics Inc.
Ultrasonic welding has long been a proven process for welding plastics and nonferrous metals.
There are two techniques for ultrasonic welding, longitudinal and torsional, which differ based on how vibrations applied to the parts.
Longitudinal, or linear, ultrasonic welding is the more common technique. However, the process has limitations in terms of the size, shape and orientation of parts that can be welded. The process also has issues with welding in restricted areas and the effects of vibration on peripheral components. These limitations are particularly evident in the electromobility and medical device industries.
Torsional ultrasonic welding overcomes some of the limitations associated with longitudinal welding. Torsional ultrasonic welding, known as Soniqtwist, was developed by Telsonic in 2006 and quickly established itself as the preferred joining process for a wide range of plastics and metals. Using Soniqtwist, torsional energy is gently exerted at the joint interface, making it suitable even for sensitive parts. Although it can be used on delicate parts, the process can apply a large amount of force over a short time.
Torsional welding can be used in applications that were deemed either impossible or unacceptable over the last decade. Even painted plastic parts can be joined securely and safely without leaving visible indentations.
Today, technology is increasingly being used in EV manufacturing. To reduce weight, class A surfaces are becoming thinner. Linear ultrasonic techniques have traditionally been used to weld substrates greater than 3 millimeters thick. Now, however, those same substrates are as thin as 2.5 millimeters thick. This is where torsional welding has proven to be particularly advantageous.
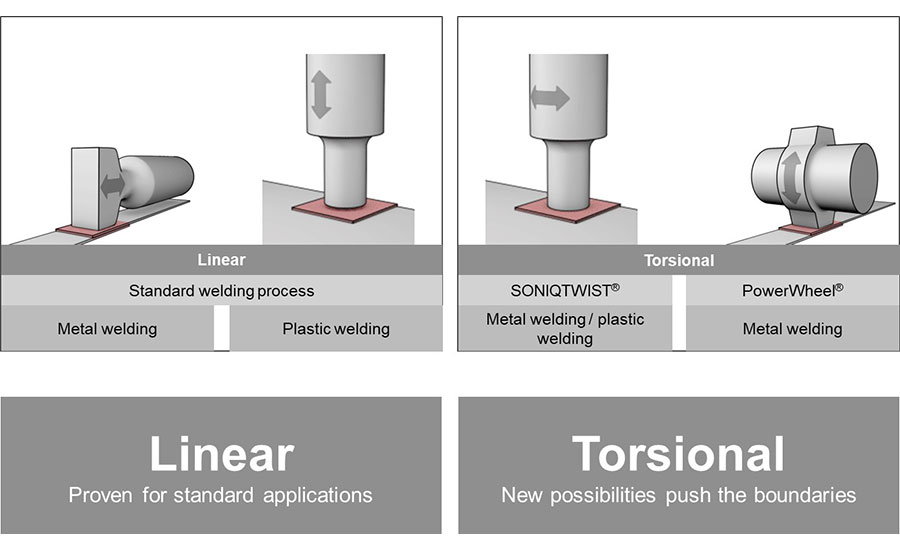
There are two techniques for ultrasonic welding, longitudinal and torsional, which differ based on how vibrations applied to the parts. Photo courtesy Telsonic Ultrasonics Inc.
Suitable for Multiple Tasks
The torsional welding procedure is ideal for joining plastics. However, it is just as effective for bending, riveting, separation, fine forming, and dimensional and shape calibration of functional surfaces. Because it has low impact on the parts being welded, it does not adversely affect sensitive electronic components.
The vibration stress induced on the lower of the two workpieces being joined is only a tenth of the stress induced by linear ultrasonic welding. Moreover, no membrane effect occurs, so filter membranes and other thin parts, such as foils, can be welded with this process. Also, when welding foils, notching effects and material thinning are hardly noticeable. As a result, this method of welding is now being used for various automotive, packaging and medical applications.
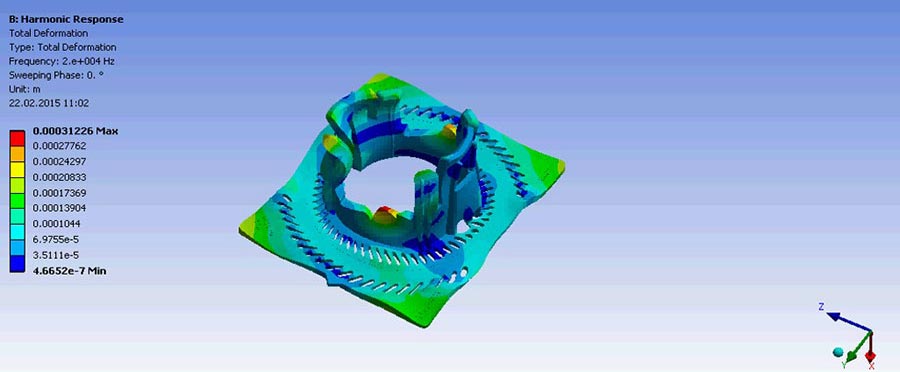
Torsional welding is suitable for welding thin films to plastic. A decoupling design is implemented into the part, and finite element analysis is used to optimize the process. Photo courtesy Telsonic Ultrasonics Inc.
How It Works
Strictly speaking, Soniqtwist is a high-frequency friction welding process that can be categorized somewhere between vibration welding and traditional ultrasonic welding. The sonotrode oscillates torsionally around its longitudinal axis in both directions. In 0.1 to 0.4 second, a high level of energy is applied to the boundary surface of both parts, with a frequency of 30 kilohertz and an amplitude of up to 55 microns, for plastic. This boundary friction enables both parts to be joined securely and safely.
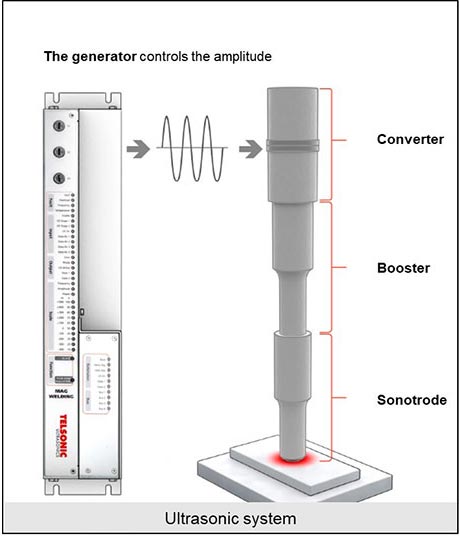
The latest generation of Soniqtwist equipment has been designed to be more compact. This makes it possible to integrate the technology in hard-to-reach places. Photo courtesy Telsonic Ultrasonics Inc.
The design of the torsional devices is similar to that of conventional ultrasonic welding equipment, comprising of a generator, converter, booster and sonotrode. However, in contrast to conventional systems, the sonotrode no longer oscillates longitudinally, but torsionally, which reduces the load on the parts. Nevertheless, ultrasonic energy can be transmitted via the sonotrode with a power of up to 14.4 kilowatts (for metal welding). Even with difficult materials, this allows for weld strengths that are difficult to achieve using conventional ultrasonic welding.
The latest generation of Soniqtwist equipment has been designed to be more compact. This makes it possible to integrate the technology in hard-to-reach places.
Operating at a frequency of 30 kilohertz and with power of 2.4 kilowatts, torsional technology is beneficial for welding parts with thin walls or for processes in which the use of linear ultrasonics may be too harsh. With linear ultrasonic welding, parts typically have to be around 3.2 millimeters thick. By comparison, torsional welding can achieve welds on parts less than 2.5 millimeters thick without read through. Pull forces of greater than 200 newtons per weld are achievable.
Torsional welding eliminates the membrane effect from ultrasonics and distributes amplitude in a horizontal direction, which means that it is also suitable for welding thin films to plastic. A patented decoupling design is implemented into the part and finite element analysis is used to optimize the process. Decoupling is necessary, as it focuses the energy over the energy director and minimizes impact to the remainder of the part.

Torsional welding can be used to assemble a variety of automotive components. Photo courtesy Telsonic Ultrasonics Inc.
The benefits of torsional welding include:
- Low vibration stress in the lower part—only a tenth of the stress induced compared with linear ultrasonic welding.
- Short welding time—often less than 1 second.
- Good accessibility, as only one vertical movement is required.
- High weld strengths.
- Comprehensive process control options.
- Far zone welds in the centimeter range.
- No membrane effects in foils, tissues and thin parts. There’s no energy concentration in the center and no hole effect.
- Great welding depth.
- Rectangular shapes can be welded securely. Parts do not have to be round.
- Power up to 2,400 watts is possible.
- Foreign bodies in the welding seam do not impair the process.
ASSEMBLY ONLINE
For more information on plastic welding, visit www.assemblymag.com to read these articles:
Ultrasonic Welder Assembles Satellite Instrument
Ultrasonic Welders Speed Assembly of Rapid COVID Tests
Ultrasonic Welds Strengthen Wearable Medical Device
Looking for a reprint of this article?
From high-res PDFs to custom plaques, order your copy today!