Driving Simulator Relies on Sophisticated Motion Control

The Stuttgart Driving Simulator is the largest and most advanced facility of its kind in Europe. Photo courtesy Research Institute for Automotive Engineering and Vehicle Engines Stuttgart
Simulators are used to train airplane pilots, race car drivers, truck drivers, teenage drivers, ship captains, and operators of heavy equipment, such as tanks and tractors. These high-tech systems enable novices to learn how to operate complex machines safely in virtual world where accidents don’t come with dire consequences.
Simulators are also used for research. Human factors and medical researchers use them to monitor driver behavior, performance and attention. In the automotive industry, simulators are used to design and evaluate new vehicles or new advanced driver assistance systems.
The latter use case was the impetus behind a new driving simulator developed by engineers at the University of Stuttgart in Germany, Bosch Rexroth, and the Research Institute for Automotive Engineering and Vehicle Engines Stuttgart (FKFS), a private, nonprofit research and development center focusing on vehicle technology, engine technology and vehicle mechatronics.
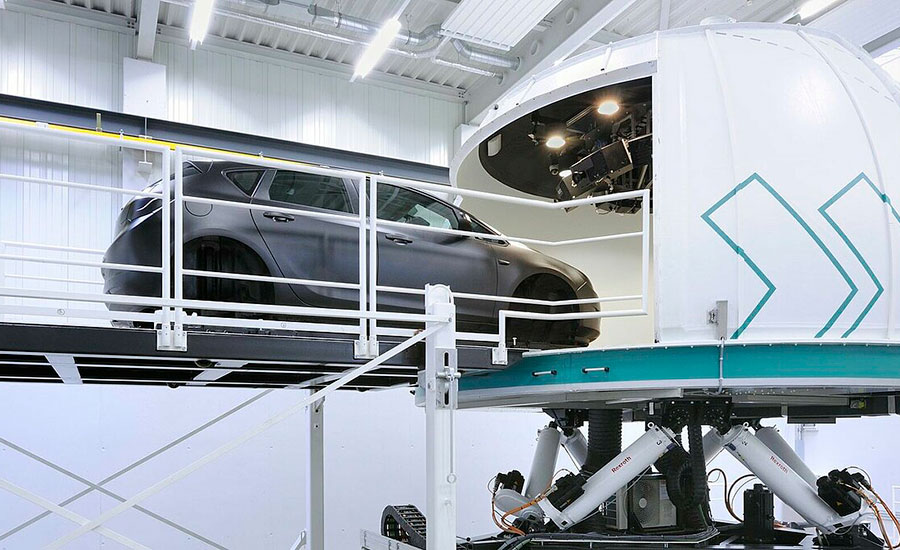
The dome itself sits on an eight-axis motion platform that provides yaw, pitch, roll and heave motion, as well as vibration. Photo courtesy Research Institute for Automotive Engineering and Vehicle Engines Stuttgart
The Stuttgart Driving Simulator is the largest and most advanced facility of its kind in Europe, says Gerd Baumann, Ph.D., head of the vehicle mechatronics division at FKFS. It is open for public research and industrial development.
The simulator consists of a dome 5.5 meters in diameter. Test vehicles can drive directly into and out of the dome, which is equipped with dynamometers for both front- and rear-wheel-drive vehicles. The simulator is being used to test production vehicles, as well as prototypes.
The replication of the visual, acoustic and haptic environment in the simulator is remarkable in every detail. A dozen LED projectors give drivers a 360-degree view of simulated roads, while a multichannel spatial sound system provides authentic ambient noise. An interface allows vehicle electronics to be connected so that the steering wheel, pedals, switches and displays function as usual.
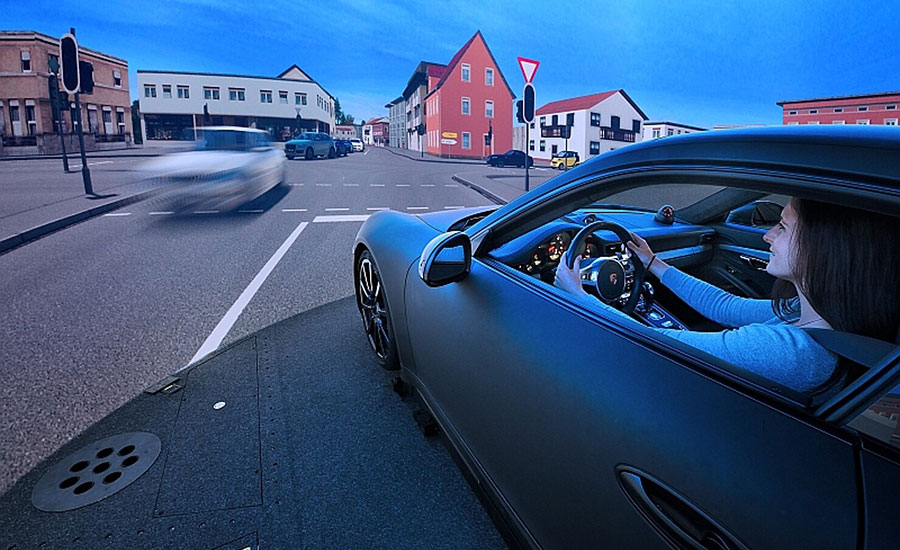
A dozen LED projectors give drivers a 360-degree view of simulated roads, while a multichannel spatial sound system provides authentic ambient noise. Photo courtesy Research Institute for Automotive Engineering and Vehicle Engines Stuttgart
The dome itself sits on an eight-axis motion platform that provides yaw, pitch, roll and heave motion, as well as vibration. Heavy-duty linear actuators generate lateral and longitudinal acceleration up to 0.8 g.
Automotive OEMs and suppliers are using the simulator to evaluate new technologies. The hope is that the simulator can save time and money in the development of advanced driver safety systems for electric and hybrid vehicles, as well as vehicles that are conventionally powered.
For example, because of the simulator’s high-end motion system, experienced test drivers can distinguish and evaluate different chassis setups interactively. Parameters of suspension, tires, steering and drivetrain can be varied quickly and easily. Active chassis control algorithms—such as front and rear axle steering, active springs and dampers, or torque vectoring—can be integrated into the simulation. Test drives can be performed in a standard virtual environment or on customer-defined test tracks.

Because of the simulator’s high-end motion system, experienced test drivers can distinguish and evaluate different chassis setups interactively. Photo courtesy Research Institute for Automotive Engineering and Vehicle Engines Stuttgart
Engineers can even use the simulator to test vehicle aerodynamics. For example, the simulator can model the effects of transient side winds.
An “electronic horizon” in the simulator provides real-time position and geometry information of other objects, such as vehicles and pedestrians, and thus allows the simulation of advanced driver assistance systems based on optical, radar or ultrasonic sensors. A GPS simulator transmits radio signals for real positioning systems installed in the mock-up. Digital road maps are also available, so assistance systems and user interfaces can be designed and tested for functionality, usability and driver acceptance.
Studies are typically done with ordinary drivers. However, on request, the FKFS can arrange for specific groups of drivers to run tests. Drivers can be selected according to age, gender and driving style.
Dampers Protect Simulator
When designing the simulator, engineers took steps to protect the equipment in the event of accidents or other unforeseen events during operation, such as power outages. In a worst-case scenario, 18 tons of mass at a maximum speed of 2 meters per second would have to be braked at the end position of the most heavily stressed axis. Emergency stoppers with immense power and equally great reliability were required. Failure could lead to massive damage to both the entire structure and the capsule. Injury to the driver would also be possible.
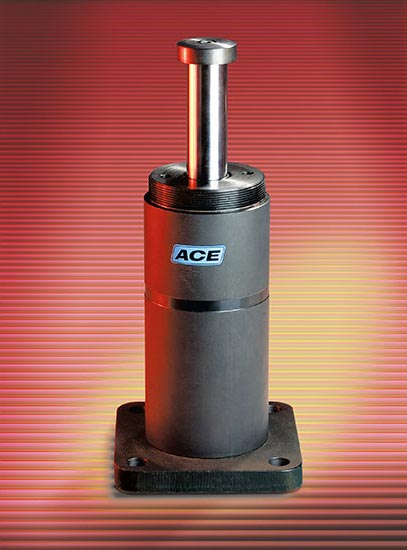
This damper offers a maximum energy absorption of 84,000 newton-meters per stroke. Photo courtesy Ace Controls Inc.
The system would need dampers that could accommodate a wide variety of mass and speed combinations. Eddy van Duivenbode, systems engineer at Bosch Rexroth, turned to Ace Controls Inc. for help.
For the first axis of motion, Ralf Küppers, sales manager at Ace’s German office, recommended SCS50-600EU-F safety shock absorbers, which can safely handle the 18-ton load. The shock absorber has a piston diameter of 50 millimeters and a stroke of 600 millimeters. With a proud weight of around 50 kilograms, the emergency damper offers a maximum energy absorption of 84,000 newton-meters per stroke.
For the second of the eight axes, which also had to be protected, the damper would need to handle a maximum load of 8,700 kilograms at a speed of 3 meters per second. Accordingly, a narrower version of the SCS series from Ace was installed. With a weight of around 35 kilograms, the SCS38-600EU-F model has an energy absorption of 43,200 newton-meters per stroke.
For more information on industrial shock absorbers, visit www.acecontrols.com.
ASSEMBLY ONLINE
For more information on robotic automation, read these articles:
Shock Absorbers for Extreme Temperatures
How to Pick the Right Damper for Your Application
A Tier 1 Supplier Implements Flexible Automated Assembly System
Looking for a reprint of this article?
From high-res PDFs to custom plaques, order your copy today!