Man vs. Machine
Industry 4.0 is evolving into human-centric manufacturing.
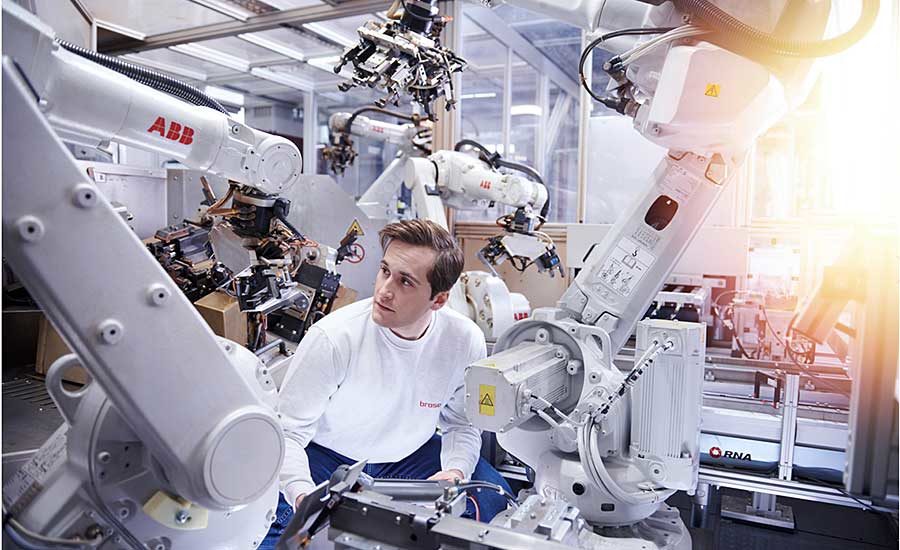



















Many people are afraid of snakes and spiders. But, robots and other machines also create anxiety and trepidation in some humans. While Industry 4.0 technology, such as artificial intelligence, augmented reality, collaborative robots, data analytics and digital twins, now make it easier than ever for humans and machines to work in close proximity, fears persist.
People are still concerned about being replaced with automation and advanced technology, such as AI. It’s a part of the human psyche that has existed ever since cries of “they’ll take our jobs!” were shouted when steam engines first appeared in industrial settings in the early 1700s.
A decade ago, a pair of economists at Oxford University sparked widespread debate when they released a study claiming that 47 percent of American jobs could be replaced by robots in the near future. Today, that fear has subsided and overall sentiment has changed.
Some people are still afraid of robots, but recent advancements in automated guided vehicles and collaborative technology have changed the dynamics of human-machine interaction.
“The general concern about being replaced by robots and other machines will always exist,” says Robert Gao, Ph.D., chairman of the mechanical and aerospace engineering department at Case Western Reserve University. “There’s a natural reason for people to worry about losing their jobs.
“The rapid advancement of AI will be increasingly felt by people,” explains Gao, who has been studying the relationship between humans and robots. “The pandemic has also encouraged many manufacturers to invest in automation to minimize the involvement of human operators.
“Some of the roles that humans have historically played in manufacturing will be replaced or substituted by robots and other machines,” warns Gao. “But, that doesn’t necessarily mean people will be out of a job; they must acquire new skills that enable them to intelligently program, control and work with machines.
“In the future, humans will not lose jobs, despite broader acceptance and engagement with machines,” claims Gao.
“Concern over humans vs. machines is a rapidly diminishing issue,” adds Jon Van Wyck, managing director and partner at the Boston Consulting Group Inc. (BCG). “There are still some legacy feelings and trepidation, but not like it was back in the 1980s and 1990s.
“With Industry 4.0 technologies, the paradigm is shifting,” says Van Wyck. “Today, the goal of automation in many cases is to enable companies to meet their production targets and throughput levels, not to replace operators. Cutting-edge robotics enable manufacturers to operate their factories in a high-value way.”
“In the past, there was more pessimism about the human role in manufacturing,” notes Craig Resnick, vice president of consulting at ARC Advisory Group. “That sentiment has now flipped in the other direction.
“Today, humans are perceived as being collaborators with machines,” explains Resnick. “We now look at machines as being part of the digital toolbox that perform routine, mundane and repetitive tasks, while humans focus on optimizing the performance of the machines and making any necessary changes or adjustments. People are better equipped to comprehend a wider variety of scenarios and make final decisions.”
Up With People
Several years ago, when faced with the challenges of automating his flagship factory in Fremont, CA, Tesla’s Elon Musk famously declared that “humans are underrated.” In today’s era of Industry 4.0 technology, many manufacturing experts believe that statement is more poignant than ever.
“Manufacturing still needs humans to combine manufacturing experience and digital capabilities to solve problems,” says Mike Doheny, senior partner at McKinsey & Co. “Technology works best when it’s in the hands of the people—it’s how you create real change in business.
“There are certain jobs automation can’t do, as they are too intricate or have complex variables, such as assembling wire harnesses,” explains Doheny. “On the other hand, there are jobs that favor automation when the business case makes sense—particularly jobs with highly repetitive tasks and few variables that can lead to more consistency in execution and produce a return on investment.
“Modern machines are also becoming more reprogrammable and flexible, which will only expand their application over the long-term,” predicts Doheny.
“Historically, machines are great for highly repetitive, simple tasks that have low variability,” adds Max Reynolds, CEO of Symbio Robotics Inc. The Bay Area startup has been helping legacy manufacturers, such as Ford Motor Co. and Toyota Motor Corp., deploy AI-controlled robots on their assembly lines.
“They’re especially well-suited to roles that would otherwise pose a threat to human safety,” Reynolds points out. “In the context of AI and machine learning, there’s an opportunity for people to focus on more creative work, such as production planning, controls engineering and robot programming. Thereby focusing time and effort on continuous improvement of the manufacturing process and overall equipment effectiveness.”
According to Reynolds, technology should fundamentally reframe existing manufacturing “pain points” by using best practices in areas such as computer vision, human-robot interaction and machine learning.
“As a species, we are very intelligent, adaptable and creative—traits that most machines lack,” says Reynolds. “The key is creating a process for embedding that intuition, domain knowledge and general intelligence into various robotic automation solutions. That’s what we believe will drive success.”
“Machines are good at tasks that are commoditized, manual and repetitive, such as assembling, welding, painting and other [activities] that need to be performed at scale,” adds Maziar Adl, chief technology officer at Gocious, a cloud-based software system for manufacturers with complex product lines.
“[They are also] good at playing out scenarios and testing a wide variety of permutations and combinations of data to help drive decision-making, because humans can’t pour through enough data manually,” notes Adl. “The tasks that humans are still best at are creativity, innovation, decision making and interacting with other humans.”
Prasad Akella, Ph.D., founder and chairman of Drishti Technologies Inc., a Silicon Valley company that is applying AI technology to manual assembly line applications, believes people are much more adaptable than machines. “Humans are better at adaptability and solving contact or force problems,” he points out. “Machines are better at noncontact position control.”
Drishti recently conducted a survey of 400 senior manufacturing executives that underscores the pervasive industry sentiment that people make manufacturing operations more adaptable than machines. In fact, 73 percent of respondents agreed with the following statement: “The more manual you are, the more adaptable you are.”
“There’s a misperception in manufacturing, including in a number of lean manufacturing shops, that the performance of people has reached its peak,” says Akella, who led a team of engineers at GM in the 1990s who pioneered collaborative robot technology. “So, while manufacturers know that people bring a lot of strengths to the table in terms of flexibility, cognition and problem solving skills, they also assume they can’t be any more productive or mistake-proof. That’s simply not the case.
“Despite talk about lights-out automation, we have a long way to go,” warns Akella. “I still see humans on the plant floor 50 years from now.”
Get Ready for Industry 5.0
A team of engineers at Case Western Reserve University, the Missouri University of Science and Technology, Stony Brook University and the University of Florida has been working on a research project to study, predict and optimize how robots will interact with human coworkers in factories of the future. The project, which began in 2018, will wrap up next year.
“While robots have been increasingly integrated into manufacturing since their introduction in the early 1960s, true human-robot workplace collaboration is still in the early stages and is only recently being earnestly studied by academics,” says Gao, who is heading up the research effort.
“Most researchers anticipate humans taking on the more nimble decision making, while robots contribute by lifting heavy tools or putting the right tool at our side when needed,” explains Gao. “This requires the robot ‘knowing’ or interpreting the human’s body language and hand movements, anticipating what he’ll do next.
“It requires using sensors, computer models and artificial intelligence that we will develop to help make the robot safely and efficiently collaborate with human operators,” adds Gao.
According to Gao, advanced collaboration technology will make factories of the future safer and more efficient as robots take on the more dangerous jobs. “Robots could also help train newer workers by already knowing what tools and parts are needed for a task that the recently hired human may still be learning,” he points out.
Gao and his colleagues plan to “focus on the prediction part of the robot-human collaboration. That means figuring out how to teach robot helpers to reliably recognize sometimes random human motions in a variety of different workplace scenarios.”
Gao says it’s part of natural evolution from Industry 4.0 to Industry 5.0, an emerging concept that addresses human-centric applications in manufacturing.
“Most discussion of Industry 4.0 is focused on machines rather than people,” adds Drishti’s Akella, who is currently writing an article about Industry 5.0 with lean manufacturing guru Jeffrey Liker. “Like Industry 4.0, Industry 5.0 has its roots in Europe.”
The European Union recently published a report on the topic. It claims “Industry 5.0 complements and extends Industry 4.0. It emphasizes aspects that will be deciding factors, not just economic or technological, for the place of industry in the future European society. These factors [also have] environmental, social and fundamental rights’ dimensions.”
According to the EU report, Industry 5.0 “places the well being of the worker at the center of the production process and uses new technologies to provide prosperity beyond jobs and growth, while respecting the production limits of the planet. It complements the existing Industry 4.0 approach by specifically putting research and innovation at the service of the transition to a sustainable, human-centric and resilient European industry.”
“The new concept of Industry 5.0 could not come at a better time,” claims Mariya Gabriel, EU commissioner for innovation, research, culture, education and youth. “Many European industries are reinventing themselves, adapting to the new COVID reality, increasingly embracing digital and green technologies to remain the solution provider for all Europeans. Now is the time to make workplaces more inclusive, build more resilient supply chains and adopt more sustainable ways of production.”
New Roles for Humans
A recent report released by the Smart Factory Institute and the University of Tennessee at Chattanooga does not refer to Industry 5.0 per se, but it contains some similar concepts and ideas. It claims that a human-based workforce will not be replaced by an automated one, and that the greatest projected workforce need is for human-centered technological skills.
According to the report, entitled “Understanding the Impacts of Industry 4.0 on Manufacturing Organizations & Workers,” advancements will require corresponding changes in the workforce, much of which will need to be reskilled and retrained to meet the demands and respond to the opportunities ahead.
The report also dispels the myth that all manufacturing jobs will eventually be automated. In fact, the need for humans with higher and more complex cognitive skills is expected to increase, and the future workforce will rely even more heavily on “human” skills such as leadership, initiative taking and entrepreneurship.
“People are at the core of Industry 4.0 technology,” says Mary Beth Hudson, executive director of the Smart Factory Institute. “Augmented reality, cloud computing, collaborative robots, connected systems and other tools change the nature of work and allow human-machine integration to increase productivity.”
Hudson claims that robots aren’t taking over factories. Instead of a loss of jobs, she believes a shift in roles is occurring.
“Jobs are changing to more strategically oriented and technologically rich roles,” explains Hudson. “Employment opportunities are greater than the potential risks.
“Automation will reduce the need for jobs that are less complex and more routine,” claims Hudson. “The adoption of Industry 4.0 is not a jobs killer in manufacturing. It’s really an opportunity to create new careers.
“Industry 4.0 brings more complex processes, demands and challenges for manufacturing workers,” Hudson points out. “It’s likely to lead to work redesign that creates more strategic tasks, greater responsibility and more decision making power for people.
“One main competency will be systems thinking, which challenges workers to develop a broad, comprehensive understanding of the overall production process and how all of the pieces fit together,” says Hudson. “That means people will no longer just be focused on their individual workstation.”
“Human-machine collaborative technology opens up new opportunities, especially for individuals who may not have been able to work in manufacturing in the past when it was considered a physically demanding environment,” adds Denise Rice, president and CEO of Peak Performance Inc. “As more physical or repetitive job tasks become automated, new positions that require greater critical thinking. trategy and technical skills will become more relevant.
“That will open up additional pathways for nontraditional manufacturing workers to join the sector,” explains Rice. “But, to prepare for that change, manufacturers must change their recruiting and selection processes.
“That may help support efforts to overcome negative perceptions about manufacturing—that it’s ‘boring, dirty, hot and repetitive’—that hinder our ability to attract and retain skilled workers,” notes Rice.
The introduction of these new job is also going to lead to changes in work design, such as increased communication and collaboration among workers.
“The remarkable transformation we are anticipating will require a blended approach of human, machine and human-machine augmented work arrangements supported by advanced technologies,” says Chris Cunningham, Ph.D., a professor of psychology at the University of Tennessee Chattanooga. “This is exciting, because there’s a potential for work to take on a higher degree of meaning, which would give [people] a chance to become more engaged and identified with their work.
“That has long been a challenge for many areas of manufacturing,” laments Cunningham. “Often, the people doing assembly tasks can’t always see the impact that their work is having. But, when you start to empower them with more information and more data, it helps enrich their job and gives them an opportunity to take more ownership over it. That will help with the recruitment and attraction of new individuals.
“It’s an opportunity to market and rebrand manufacturing in a different way so that people understand that we’re no longer talking about mindless work,” explains Cunningham. “It’s not about trying to plug people in and make them part of a machine.”
The Soft Side of Automation
Despite recent advancements in artificial intelligence, collaborative robots and other cutting-edge automation, humans play an important role in determining the effectiveness of machines.
“People are still much better at high-level thinking and cross-functional coordination,” says Ryan Martin, industrial and manufacturing research director at ABI Research. “Machines are better at handling tasks that require fast cycle times and continuous flow processing.”
“Technology such as digital tools and collaborative robots enable people to be more efficient,” adds BCG's Van Wyck. “Humans are better suited for tasks that require dexterity, judgment and variation. Therefore, they should focus on manufacturing activities that drive higher throughput and yield.”
One manufacturer that is embracing next-geneation automation, but not forgetting the human connection, is Brose North America Inc., a leading producer of automotive cooling fan modules, door modules, seat systems and other components. The Tier One supplier has focused heavily on hiring and retention efforts.
“During the fourth industrial revolution, machines will not replace people, but a new category of worker will emerge, right between white and blue [collar],” predicts Arnd Herwig, vice president of engineering at Brose North America. “The convergence of products and automation complexity creates a perfect manufacturing storm.
“The need for this ‘new collar’ job category, such as advanced manufacturing, cybersecurity and mechatronics, highlights the inadequacies of education today, as industry progresses faster than curriculum,” explains Herwig, who oversees Brose’s apprenticeship program.
“At times, automation has been villainized and seen as something related to downsizing,” adds Frank Langro, director of product market management for pneumatic automation at Festo Corp. “Many people fear change, so its’s important to be transparent and communicate with employees who may be impacted by automation investments.
“For instance, focus on the benefits of automation that workers who are impacted directly by it can see and relate to,” suggest Langro. “If it’s something that can make their jobs safer or easier, few people should be opposed to something like that. Automation can also give workers an opportunity to learn new skills.
“When you get buy-in, your project will run smoother and have a much higher chance of success,” claims Langro. “However, it’s also important to pay attention to some of the soft facts about automation that need to be communicated to upper management.”
According to Van Wyck, manufacturers that deploy new automation also tend to be more successful if they invest in a period of “hyper care.”
“For a period of time, operators should receive an extra layer of support as they adopt new technology and learn how to use it and integrate it into their daily work flow,” explains Van Wyck. “During this transition period, an onsite change coach should help with the deployment of technology such as collaborative robots and digital tools. This period of intense support is gradually reduced over time.”
Looking for a reprint of this article?
From high-res PDFs to custom plaques, order your copy today!