Alternative UV-Curing Adhesives
A new generation of UV-curing silicones and epoxies are increasingly being used in automotive and electronics applications.
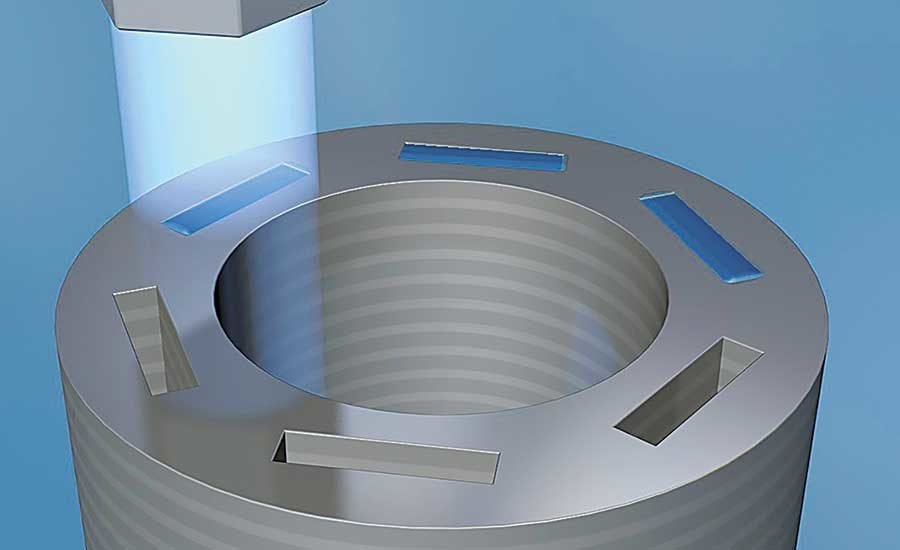
When exposed to ultraviolet light, UV-cure silicones and epoxies cure within 1 to 5 seconds. Graphic courtesy DELO Industrial Adhesives LLC

UV-cure adhesives require special equipment for proper curing, but work fine with standard timepressure and positive-displacement systems. Photo courtesy Epoxies Etc.

Types of UV-cure silicones include adhesives, conformal coatings and cure-in-place and form-in-place gaskets. Photo courtesy Henkel Corp.

The PICO Pμlse valve is able to repeatably dispense microdots as small as 0.5 nanoliter, at up to 1,000 hertz continuously. Photo courtesy Nordson EFD




Every action in life involves a trade-off: The gaining of one benefit at the expense of another, to best meet the needs of the situation at hand. When the situation involves high-volume bonding, sealing or gasketing, manufacturers rely on UV-cure adhesives because they allow on-demand and quick curing (1 to 5 seconds after light exposure).
The trade-off, however, is that these adhesives (acrylic, silicone and epoxy) require a transparent substrate to properly bond, and they cost significantly more than adhesives that cure by other means. Nevertheless, countless manufacturers in many industries have happily made this trade-off for several decades. Many more companies will do so for the foreseeable future. The difference, however, is that engineers will be as likely to use a silicone or epoxy UV-cure adhesive, as one that’s acrylic-based.
“Although we’ve made UV-cure silicones for the last decade or so, in the last three years we’ve had to intensify our selling efforts to keep up with market demand,” notes Doug McKinzie, vice president of specialty products at Novagard Solutions. “Our UV-cure silicone sales have increased 50 percent the past few years. This will lessen some, but we still expect good growth for the next several years.”
Among the biggest users of UV-cure silicones are automotive OEMs, and Tier 1 and Tier 2 suppliers. One Tier 2 supplier uses Loctite SI 5031 sealant from Henkel Corp. to pot terminals in housings for electronic brake-control modules and tire-pressure sensors. The company also uses Loctite SI 5039 to form a UV-cured-in-place silicone gasket around the perimeter of each module. Bill Brown, manager of applications engineering for Henkel, says that both products contain a fluorescent dye to help verify adhesive presence during final inspection.
This subassembly is then sent to a Tier 1 supplier that inserts additional internal components and connects a PCB to the terminals. A cover is placed over the perimeter gasket to create an environmentally tight seal on the final assembly.
UV-cure epoxy adhesives are also frequently used for automotive and consumer electronics applications. One reason is that these adhesives, like silicones, are specifically formulated to match the wavelength of LED light sources (320 to 550 nanometers), so manufacturers get all of the benefits of LED lighting, such as long life, limited heat and flexible configurations. Another reason is the lower capital costs of UV curing, thereby making it easier for companies to trade up to this technology.
Two Winning Formulations
Quick curing is but one of several benefits that UV-cure silicones and epoxies offer. Manufacturers also like that the products are one component (usually), solvent free (resulting in low VOC emissions), optically clear, allow precise part positioning during open time, and can be dispensed and cured either manually or automatically with small-footprint equipment that easily integrates into an assembly line.
Both types of adhesives were brought to market around the same time—late 1970s to early 1980s—but feature different curing chemistries. Silicones undergo a thermal radical cure, whereas epoxies cure cationically.
Each silicone adhesive is formulated with a photoinitiator that is sensitive to UV light. When exposed to light of the correct wavelength and intensity, the photoinitiator decomposes into free radicals that initiate the formation of monomer chains. After many propagation steps, the chains polymerize within seconds and become fully cured.
Epoxy adhesives also feature a photoinitiator, but it converts into a strong acid when exposed to the correct radiation wavelength. This acid drives the epoxy resins into a chain-transfer polymerization reaction.
UV-cure silicones come in single- and dual-cure formulations that are flowable (up to 5,000 centipoise [cps]) or thixotropic (100,000 to 300,000 cps). Product types include adhesives, conformal coatings and cure-in-place and form-in-place gaskets.
Dual-cure products initially cure with UV light, but require a secondary mechanism to fully cure. They are often used in potting applications or on parts with shadowed areas due to tall components on one side. Ambient moisture and heat are the most common secondary mechanisms. Final cure can take up to 72 hours.
“Because silicone is elastomeric, it remains soft and flexible in temperatures from -60 to 200 C,” says McKinzie. “Plus, it bonds well to a wide range of substrates, including glass, metal and various plastics.”
Silicone also offers high elongation, low shrinkage, long durability, and it can be disposed as a nonhazardous material. In addition, it provides good thermal management by shielding electronics from moisture and environmental stress. The material’s negatives include low tensile strength (often less than 500 psi) and gripping surfaces without chemically interacting with them.
Novagard’s RTV 800-260 is a UV dual-cure silicone conformal coating for PCBs. It is versatile enough to use for potting automotive sensors and light bulbs, and sealing bar code scanners and camera optics. The single-component material is flowable enough (2,000 to 5,000 cps) to be applied with a spray valve, and it contains a UV tracer to ease part inspection. Moisture is the secondary cure mechanism. The cured coating has 100 percent elongation and 100-psi tensile strength.
Loctite SI 5031 is a silicone sealant that flows easily onto parts for sealing, potting and encapsulation applications. The one-part material cures tack-free in 20 seconds or less when exposed to either UV or high-power visible light sources. Once cured, it is a translucent (non-yellowing), medium-strength and flexible rubber sealant that resists moisture, corrosion, and extreme weather and temperatures. It is often used to pot connectors in automotive and electronics applications.
Epoxies offer high sheer strength, low shrinkage, low toxicity and excellent resistance to oils, fluids and chemicals. Several products are designed to inhibit oxygen during curing so the surface is free of tackiness or stickiness. On the downside, they’re harder, more brittle and don’t bond as well as silicones. Plus, they begin to degrade in temperatures above 150 C.
One- and two-part epoxy adhesives are available for assembly applications in viscosities up to 50,000 cps. One-part adhesives cure within seconds via cationic polymerization. But, two-part formulations become gel-like upon initial UV exposure, and finish polymerization through shadow cure at room temperature. The latter process can last up to several days because the generated acids have long active lives in solution form.
“Creating custom UV-cure epoxies is very common for us,” says Torsten Uske, president of DELO Industrial Adhesives LLC, which also makes standard UV-cure epoxies. “Our customers’ complex design requirements continually push us to add more functionality to the adhesives.”
Several Tier 1 automotive manufacturers use DELO-Katiobond 45952 epoxy adhesive to join decorative elements in the dashboard, mirrors to plastic frames for head-up transparent displays, and PBT plastic housings onto PCBs for windshield hygrometers. Milky brown fluorescent in color, the dual-cure thixotropic adhesive uses a patented pre-activation process to bond opaque components. Surfaces to be bonded must be dry and free of dust, grease, oil and other contaminants.
The one-component UV Cure 60-7170 epoxy from Epoxies Etc. is designed to be used as an adhesive, coating or encapsulant. Water clear and moisture and chemical resistant, the product will cure at thicknesses of up to 0.75 inch. Another unique and important feature is the product’s ability to cure in shadowed areas. Once exposed to UV light, it continues to cure in the absence of light.
Al DeSisto, director of technical sales at Epoxies Etc., says the epoxy bonds well to metal, plastic, paper and ceramic. It may also be heat cured as a secondary cure operation. The epoxy is not affected by oxygen and has a rigid, smooth and glossy surface when properly cured. UV Cure 60-7155 is a lower viscosity (1,000 cps) version of 60-7170.
Choose Wisely
“We ask end-users lots of questions when they come to us to buy UV-cure adhesives, because every application is unique,” explains DeSisto. “For starters, we need to know where the epoxy material is to be used, how much will be used each cycle, and how it will be applied.”
That’s important, because UV-cure epoxies and silicones are not inexpensive. For example, using these materials on large PCBs in a high-volume operation may not be economical.
“Price needs to be addressed quickly when recommending UV-cure
products,” says McKinzie. “The typical UV-cure silicone adhesive costs five times as much as standard silicone and twice as much as the standard epoxy adhesive. That’s why UV-cure products are almost always applied in small amounts on millions of parts.”
DeSisto says his customers include low- and high-volume users of UV-cure materials, which are applied to the products either manually or with fully automated equipment. Regardless of production volume, however, he always discusses with end-users the types of stresses the cured material will be subjected to, including shear, tensile, cleavage and peel.
Optimum part bonding requires one substrate to be transparent so the UV light completely covers the joint interface. This is why these adhesives are used extensively with parts having clear plastic or glass features.
“Manufacturers should be honest about their level of UV-cure knowledge, and if an application involves any shadowing,” says McKinzie. “Let’s say that a company decides to use a straight-cure conformal coating for an electronics potting application. If there’s shadowing, the coating may seep into certain components without curing. What’s really needed is a dual-cure coating.”
Substrate and environmental conditions are also important, says Brown. Engineers need to tell their suppliers if any surface contamination is possible on the substrate during application, as well as substrate types, temperature range of the final component and all environmental conditions the adhesive will be exposed to after curing.
“It’s important that the manufacturer determine all of the application requirements before looking for the best UV-cure solution,” summarizes Uske. “Technical and process factors like curing speed, material-to-substrate interaction, material stress and aging requirements, and dispensing method need to be carefully considered.”
Add Equipment to the Equation
UV-cure adhesives require special equipment for proper curing, but work fine with standard time-pressure and positive-displacement systems—so long as all wetted parts (plastic or metal) are compatible with the adhesive, and all plastic components block UV light.
“Jetting valves are increasingly being used to apply UV-cure materials,” says Tom Muccino, regional sales manager at Nordson EFD. “They dispense 1,000 to 1,500 dots per second without even contacting the substrate.”
A couple years ago, Nordson introduced the PICO Pµlse valve, which is able to repeatably dispense microdots as small as 0.5 nanoliter, at up to 1,000 hertz continuously. The noncontact valve’s modular design enables it to jet low- or high-viscosity fluids onto any surface, including uneven and tough-to-reach substrates. Interchangeable parts increase the valve’s versatility. Muccino says users of the valve include machine builders, and makers of medical devices and consumer electronics.
Looking for a reprint of this article?
From high-res PDFs to custom plaques, order your copy today!