LEDs Prove More Efficient Than Metal Halide Lamps for Factory Lighting

LEDs use about half the energy of metal halides to deliver the same amount of light, and they last seven times longer, on average. Photo courtesy Big Ass Solutions

A 400- to 500-watt metal halide bulb like this one is commonly used to light assembly plants. It can generate 25,000 to 35,000 lumens when initially installed. However, lumen depreciation occurs quickly. Photo courtesy Big Ass Solutions
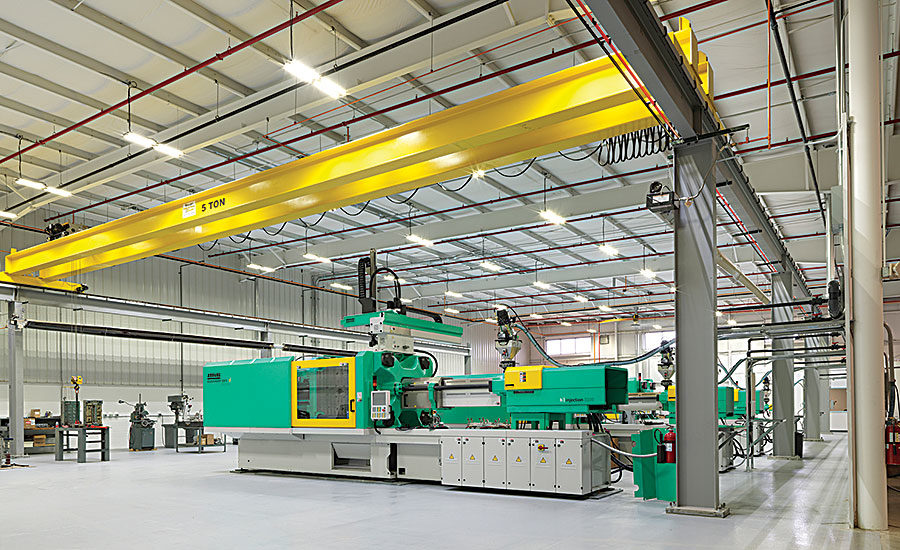
Wisconsin-based job shop Northern Metal Fabrication recently began replacing the metal halide bulbs at its factory with energy-efficient LED lighting. Photo courtesy Big Ass Solutions



There’s a heated debate about energy efficiency in lighting. The question at the heart of it is whether LEDs or modern fluorescents offer the best light for the least lifetime cost.
You might notice that high-intensity discharge (HID) lamps, such as metal halide and high-pressure sodium lamps, are rarely part of the discussion. Now look up. Are your facility’s fixtures round? If so, chances are you’re spending a lot more money, and burning a lot more energy, than you need to.
HIDs—which can easily be spotted by their distinctive round fixtures—are still commonly used for high-bay lighting in factories, assembly plants and warehouses, yet they are by far the least energy-efficient lighting option for indoor, industrial spaces.
In this age of carbon-footprint consciousness, the end of the HID is looming. Eventually, HID lamps will go the way of the incandescent bulb or T12 fluorescent bulb. New energy efficiency standards will make them obsolete. There’s no sense in waiting.
Replacing HID lamps can potentially cut lighting energy costs in half, which means minimal payback time, regardless of whether they’re replaced with cheap fluorescents or pricier, but more efficient, LED fixtures.
Swapping out fixtures can be daunting. Maintaining the same or similar light levels often requires the help of lighting engineers to compensate for differences in light output and beam distribution. However, the first step to a brighter future is to simply take a look at the lights in your facility and remember the following advice: If it’s round, take it down.
Light History
Metal halides are the most common type of HID in industrial facilities. At one time, they were prized for their energy efficiency and long life. Things were different when metal halides were first commercialized in the 1960s—20 mpg was pretty good gas mileage for a family sedan, and the media warned of global cooling rather than the other thing.
Metal halides work similarly to fluorescents in some respects and incandescents in others. They pass an electrical arc through a gas-filled tube like a fluorescent, but, like an incandescent, the arc itself creates bright, visible light. That process isn’t efficient—about 75 percent of the energy metal halides consume is wasted as heat.
Brightness is one of the few remaining selling points of metal halides, which is why 1,000-watt metal halides are commonly used for stadium lighting. For high-bay metal halide lighting, 400- to 500-watt bulbs are most common. They can generate 25,000 to 35,000 lumens when initially installed. However, lumen depreciation occurs quickly. A metal halide bulb’s light output typically decreases by half within a year or two.
When inefficient incandescent bulbs were still commonly found in businesses and homes, a high-bay metal halide’s 80-lumens per watt and rated life of two years were industry leading. Now, they’re trailing the pack.
Inefficient Lighting
Lighting typically accounts for anywhere from 25 to 40 percent of energy used in a business, according to the U.S. Environmental Protection Agency. Facilities on the high end of that spectrum using metal halides could save up to 20 percent on electricity by switching to energy-efficient LEDs.
Northern Metal Fabrication, which cuts and shapes metal for automakers, wastewater treatment plants, railroads and other customers, was one such facility that used metal halides. Last year, the company began phasing in LED fixtures at its 80,000-square-foot facility in Baldwin, WI, as part of an ongoing energy savings initiative. In the first year, utility bills were reduced by $10,000. That doesn’t include savings from reduced maintenance. Changing metal halide bulbs was almost a full-time job, says Jay Burton, a buyer at Northern Metal Fabrication.
“The LEDs have helped from a maintenance standpoint and an energy-use standpoint. It’s a little expensive up front, but it’s a pretty quick payback,” he says. “We determined the LEDs will pay for themselves in about three years; that’s pretty quick.”
LEDs use about half the energy of metal halides to deliver the same amount of light, and they last seven times longer, on average. A 20,000-lumen LED and a 455-watt metal halide produce roughly the same amount of light, but a typical LED fixture uses less than 200 watts to do so.
Additionally, LED fixtures
can start paying for themselves before they’re ever turned on. Many utility companies offer rebates to companies that upgrade to energy-efficient lighting. Burton says Northern Metal Fabrication was reimbursed about $60 per fixture, which totaled $6,000 for the 100 LED fixtures installed in phase one.
Other Problems
High energy use isn’t the only drawback of metal halides. The laundry list of problems includes:
High maintenance. Metal halides have an average rated life of less than 20,000 hours, compared to 35,000 for fluorescents and up to 150,000 for high-quality LEDs.
Long warm up. Metal halides require up to 15 minutes to reach full brightness when first turned on. In addition, they need up to 20 minutes before they can be turned on again when they are turned off.
High heat production. Metal halides produce up to 350 F of heat, compared to only about 100 F for LEDs.
Occasional explosions. Older metal halides can explode with no warning, requiring the use of protective, enclosed fixtures and creating a market for more expensive “explosion-proof” bulbs.
Mercury. Metal halides, as well as many fluorescents, contain mercury gas. It’s generally not enough to harm humans. However, mercury from discarded bulbs can be harmful to the environment.
Burning Money
There is a valid discussion to be had about lighting, and proponents of both fluorescents and LEDs make convincing points. To sum it up, fluorescent light fixtures are cheap, bright and use little energy. LED fixtures are more expensive, but they’re 5 to 10 percent more energy efficient than fluorescents and practically eliminate maintenance costs.
Metal halides offer all of the drawbacks with none of the benefits. Replacing them can improve light levels, reduce energy costs and improve productivity. Consult with a company that has lighting engineers on staff who can help customize a lighting layout that will provide maximum brightness with minimal energy use.
Looking for a reprint of this article?
From high-res PDFs to custom plaques, order your copy today!