Robots and factories are no longer differentiators
Real competitive advantage lies outside of the process of making things.
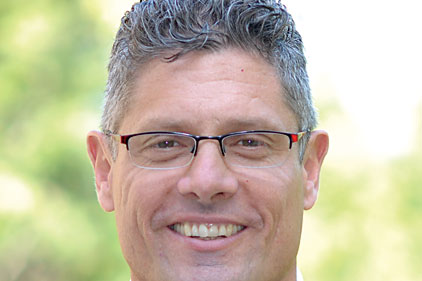
There’s lots of talk about a manufacturing renaissance. Some call it a resurgence, others a revolution, but the name doesn’t matter. There’s also been a lot of argument over the magnitude of the decline in manufacturing and how to measure it. Some say there wasn’t a decline at all. None of that matters, either.
While it’s good there’s more awareness on the importance of manufacturing, it’s troubling to see the narrowly cast theme that cuts across the leading thinking. All the talk is about reshoring, right-shoring and robots. It’s all about improving the efficiency of making.
Yes, factories are important; yes, where to put them is important; and, yes, the level of automation is important. But, these things are no longer differentiators.
Lean manufacturing is pretty clear about where to locate factories: Put them where you sell. Lean is also clear about automation: Automate everything that makes sense, but no more. The principles of lean show the path forward. With a “manufacturing is all about the efficiency of making” worldview, it’s a dog-eat-dog, profit minimizing, race to the bottom. But worse, it’s a level playing field for all, with little opportunity for competitive advantage. Everyone’s rowing the same boat toward a shared destination.
But manufacturing companies do more than make, and that’s where the real competitive advantage lives—outside of making. The real differentiator is product design.
A back-to-the future approach won’t cut it because the context has changed for manufacturing companies. They now must sell products across the globe, and the biggest growth opportunities are in the developing countries. This amplifies the disruptive power of design. In most cases, the product should be customized for each region—unique features, function and feel—so there’s broad appeal. More importantly, the product should have the right cost structure so it’s viable in the region where it will be sold.
The developing world has radically different needs and a whole different pocketbook, and that will drive product design in unfamiliar directions. The developed world’s more-with-less thinking is directionally incorrect. For the developing world, it’s less-with-far-less, in which the product does less and costs a whole lot less. If the cost of the existing product is 100 percent, the developing world needs a solution that costs 10 percent of that to start, followed closely by a 1 percent solution. Improving the efficiency of making won’t cut it. Without radically changing the design—innovation—manufacturing’s race for efficiency runs aground. There’s no sense in highly efficient factories rapidly making products that don’t sell.
It feels silly to say this, but manufacturing companies don’t just make, they invent, innovate, design, market and sell, too. Yet the ruckus around the manufacturing renaissance is limited to factories and robots. I’m not sure why we think of manufacturing strictly as the process of making things, but we do. In truth, the making is a result of all the other stuff. Where’s the ruckus over design? Where’s the national dilemma around innovation?
The singular focus on efficiency has caused designs to converge on the lowest common denominator. The next evolution of manufacturing requires product divergence to create the 10 percent and 1 percent products for the developing world.
Factories and efficiency are important, but not to the exclusion of design. New technologies are needed to reset the cost signature; new materials are needed to do things for a tenth of the cost; and a new mindset is needed to create absurdly different products for the developing world at the expense of watering down existing products. And, yes, we need efficient factories and robots.
The funny thing is the biggest lever for factory efficiency is product design. And, the only way to use robots is to design the product to make it so.
Looking for a reprint of this article?
From high-res PDFs to custom plaques, order your copy today!